20.07.2021
INTRANAV SMART production:
Real-time location tracking of AGVs, automated workflows,
paperless factory & Co.
One of the most successful international formwork and scaffolding manufacturers was looking for a solution to control and monitor the material flow between production and the galvanizing plant. In order to transport the produced goods from A to B across the large area with the various loading stations, driverless transport systems are used to handle the material transport fully automatically. The routes are operated according to strict time specifications. So far, it was not possible to monitor how the routes were actually executed and where the AGVs are located in the daily process. In case of interruptions in the process flow, this has always meant: long search times for the employees, including identification and determination of the cause. This resulted in delays in further processing. In addition, manual handling, such as the issuing of production documents, inhibits the advanced flow of materials.
In order to comply with first-in-first-out in the galvanizing plant, the high input also required an immediate solution that allows automatic identification of the produced goods.
For a leading international manufacturer
of formwork and scaffolding systems
The Company Group is one of the leading international suppliers of innovative formwork and scaffolding systems with customized logistics, service and engineering services for construction, maintenance, and refurbishment, employing around 10,000 people worldwide.
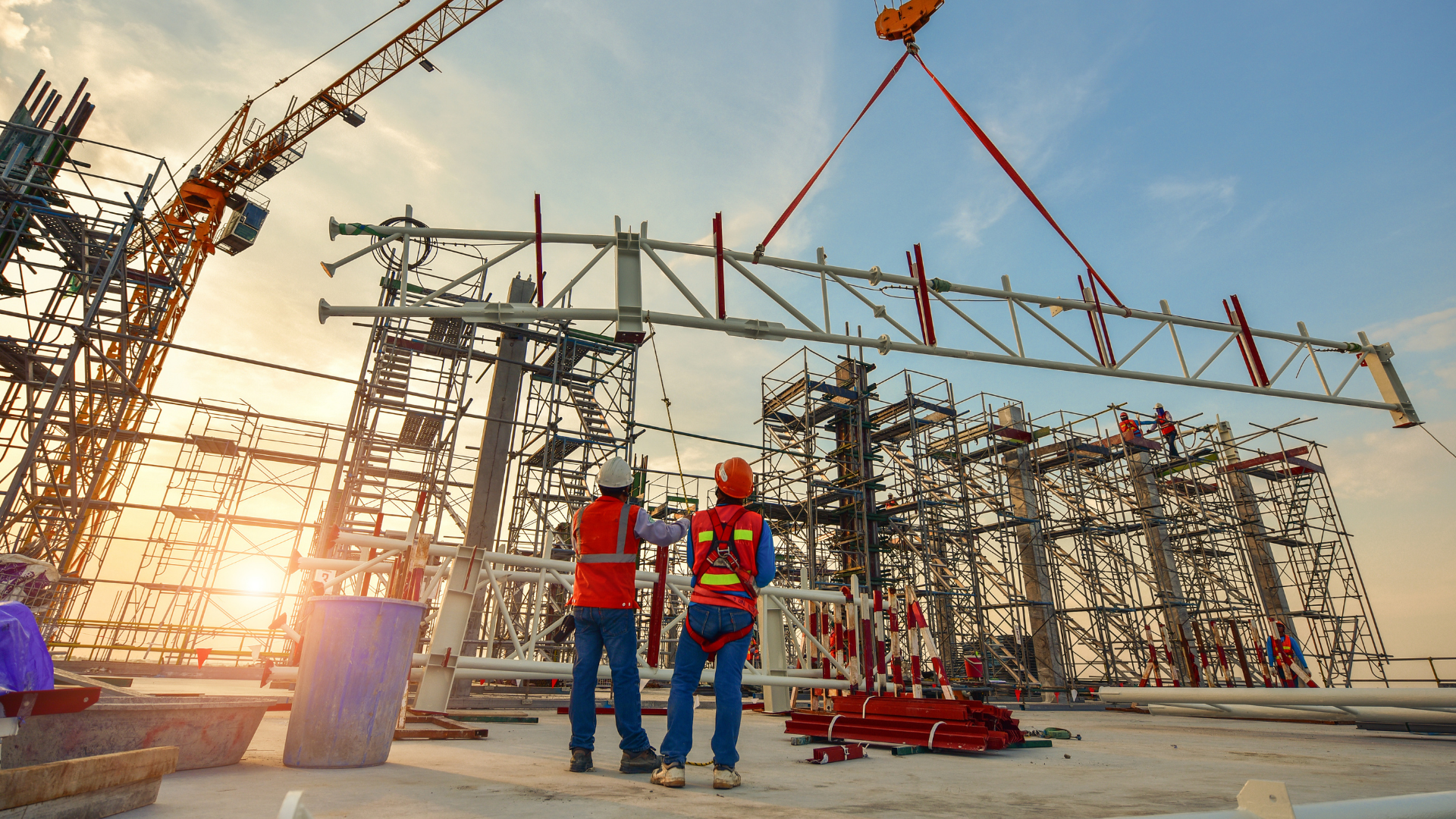
Requirements of our customer
-
1
Real-time location information about the load carriers in the plant
Accurate (±) 10 cm real-time location information by tracking load carriers for scaffolding systems in production.
-
2
Implementation of the FIFO process
Implementation of the FIFO process in the material buffer of the galvanizing plant through time stamping. INTRANAV.IO recognizes the different loading points of individual production plants, buffer locations & their loading situation.
-
3
Material flow analyses for the optimization of material flow processes
Analysis of resource utilization, zone dwell times, routes, etc. of the load carriers and AGVs.
-
4
Paperless Factory
Association and digitization of transport documents with INTRANAV.RTLS TAGs.
-
5
Visualization of loading information
Visualization of the loading information (part number & quantity) by means of third-party software interface (automation & visualization software).
Solution from INTRANAV
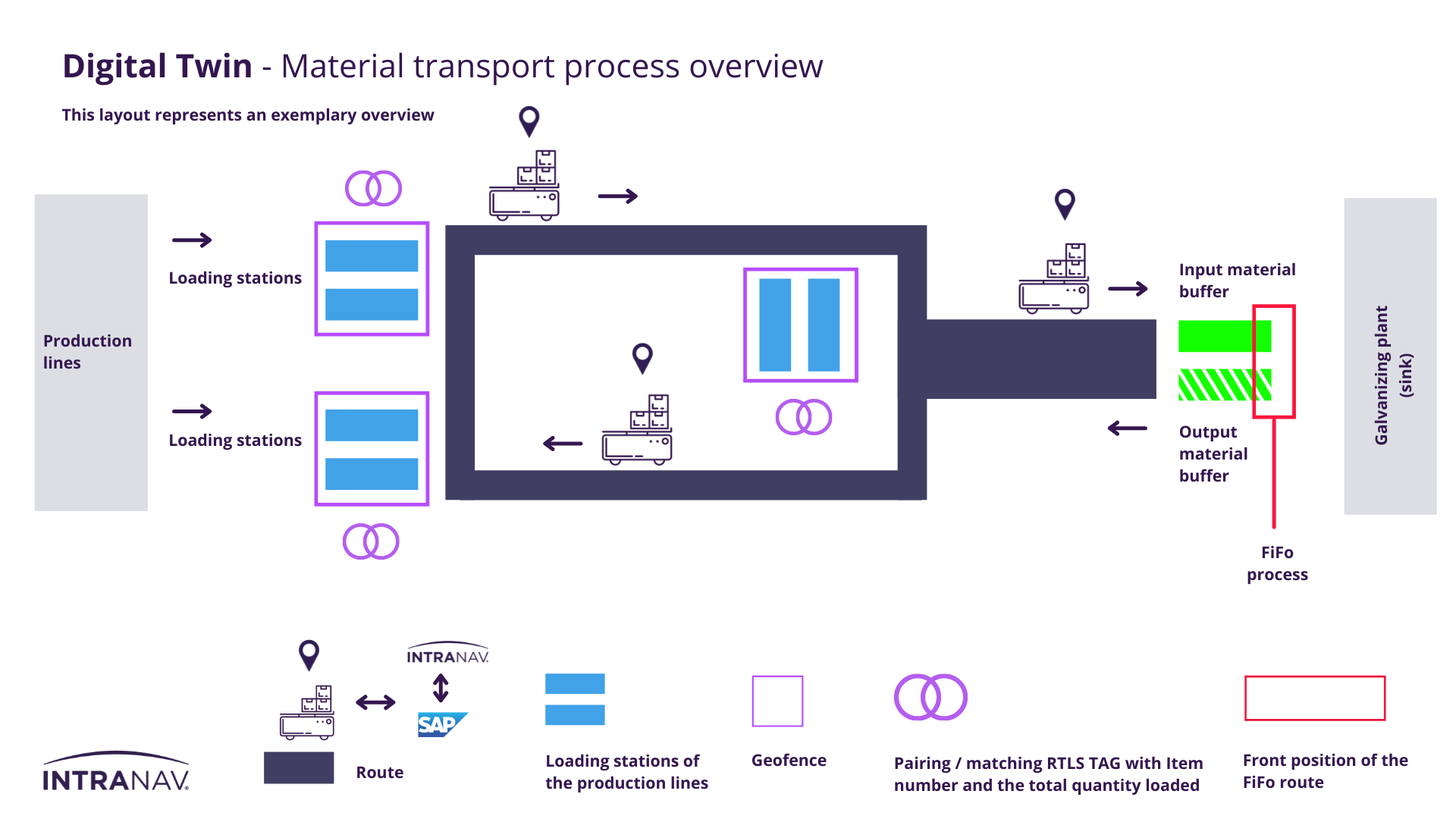
The INTRANAV.IO RTLS system is used for real-time location of transport racks loaded with articles or unloaded, which are on their way from the metal processing plant to the galvanizing plant. The transport racks are carried by driverless transport vehicles (AGVs). The material flow between the fully automated but also partially semi-automated production is tracked in real-time.
The information “article number & quantity” from the corresponding production line in the metal processing area is linked to the INTRANAV.RTLS TAG in order to display it by a monitor, ordered according to the FIFO process in the galvanizing plant. One monitor per material buffer (FIFO line) is installed, which displays the information of the corresponding material buffer.
The information linked to the INTRANAV.RTLS TAG has to be retrievable by an employee at any time, which is ensured by a barcode on the TAG. The information is displayed using a browser app in the company’s internal WLAN via a website of the contractor.
Automatically integrate transport racks
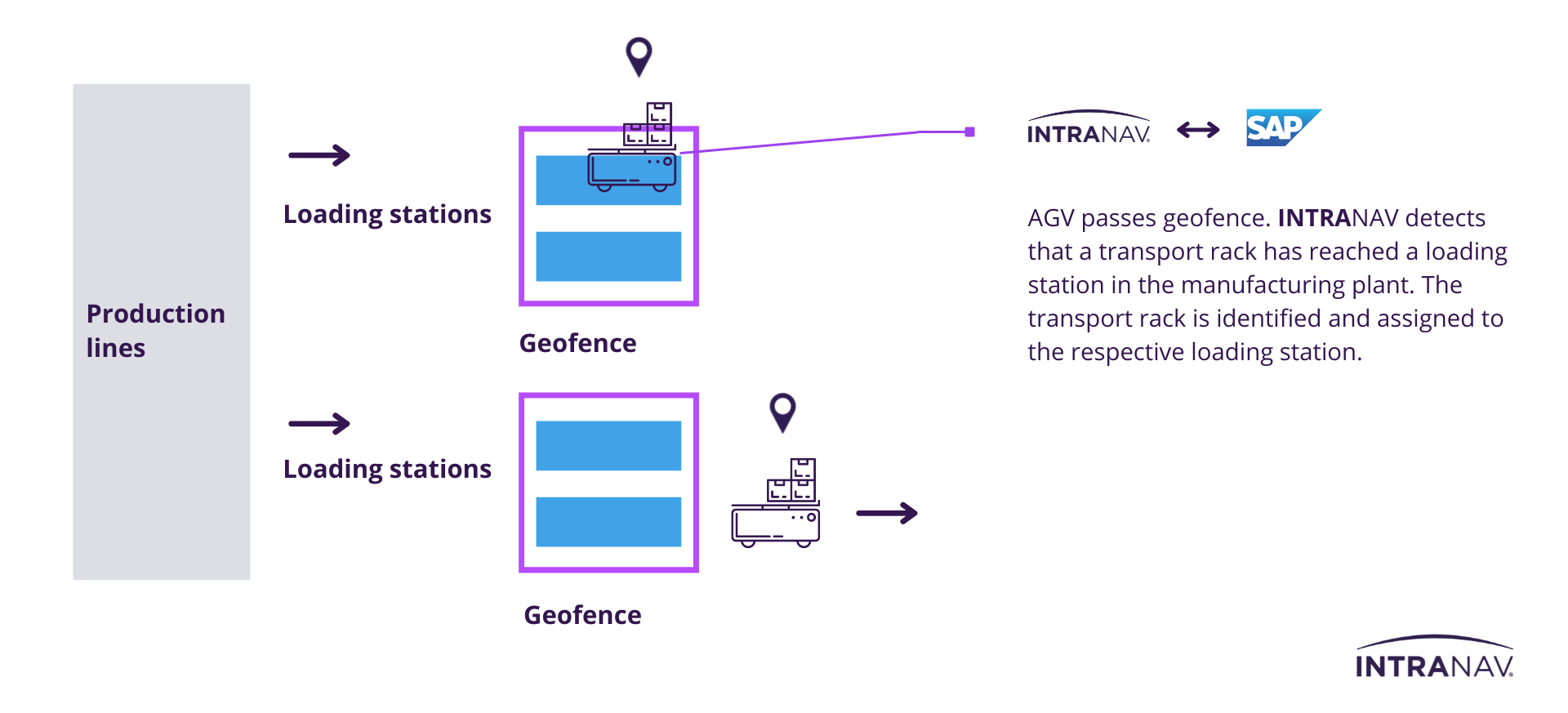
The INTRANAV.RTLS identifies via virtual zones (geofences) as soon as a transport rack from the production plant reaches one of the loading stations. The transport rack will be assigned to the respective loading station. The system or the machine operator afterwards loads the transport rack.
Association of the transport and article information with the RTLS TAG
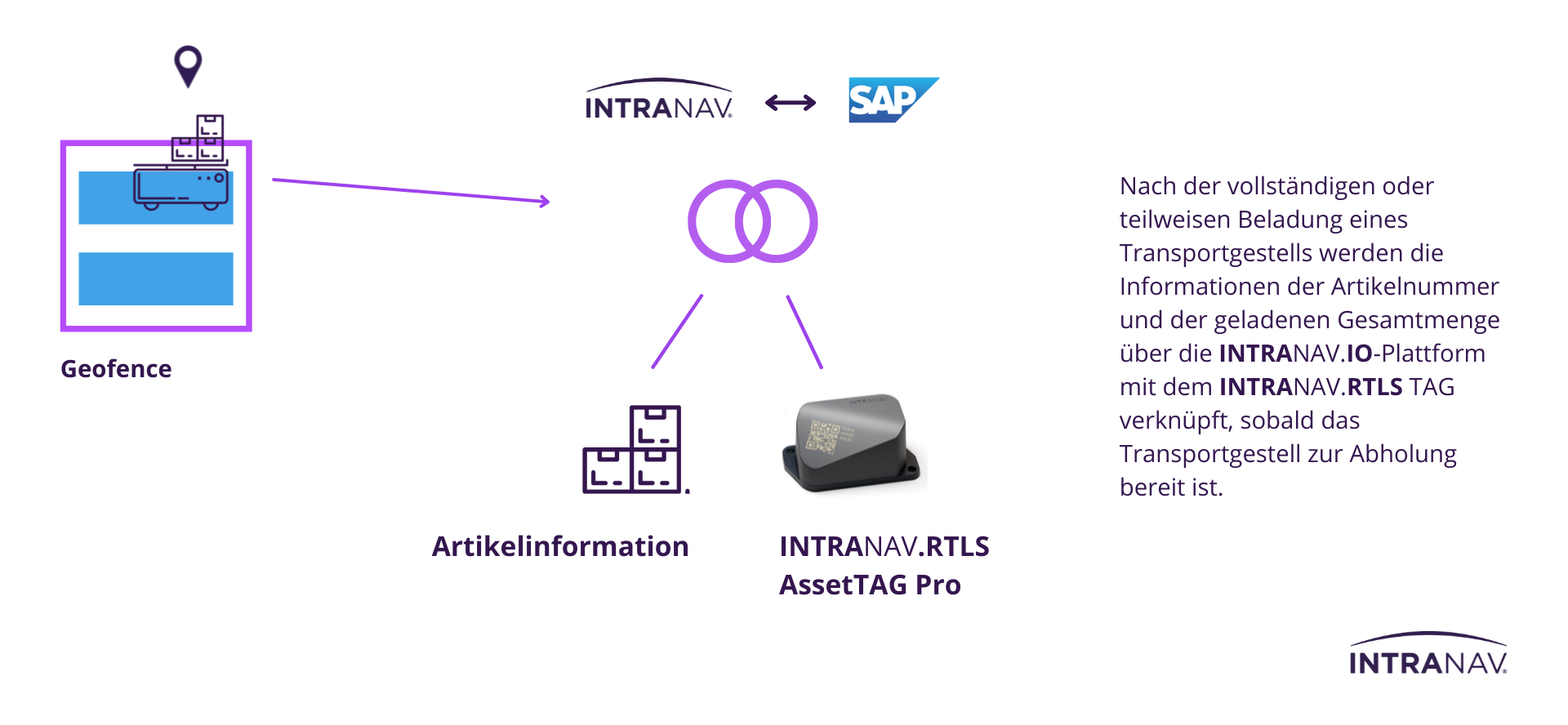
After complete or partial loading of a transport rack, the information of the article number and the loaded total quantity is linked to the INTRANAV.RTLS TAG via the INTRANAV.IO platform as soon as the transport rack is ready for pickup. The trigger for updating the information (after completion of the loading process) is provided by the plant control system itself in the case of fully automated production plants and by the employee using an Android, iOS, or Windows device in the case of semi-automated production plants. INTRANAV.IO accesses the data (article number/number of pieces) via an interface and links it to the TAG (the TAG ID) as described above.
Real-time location tracking of the load carriers
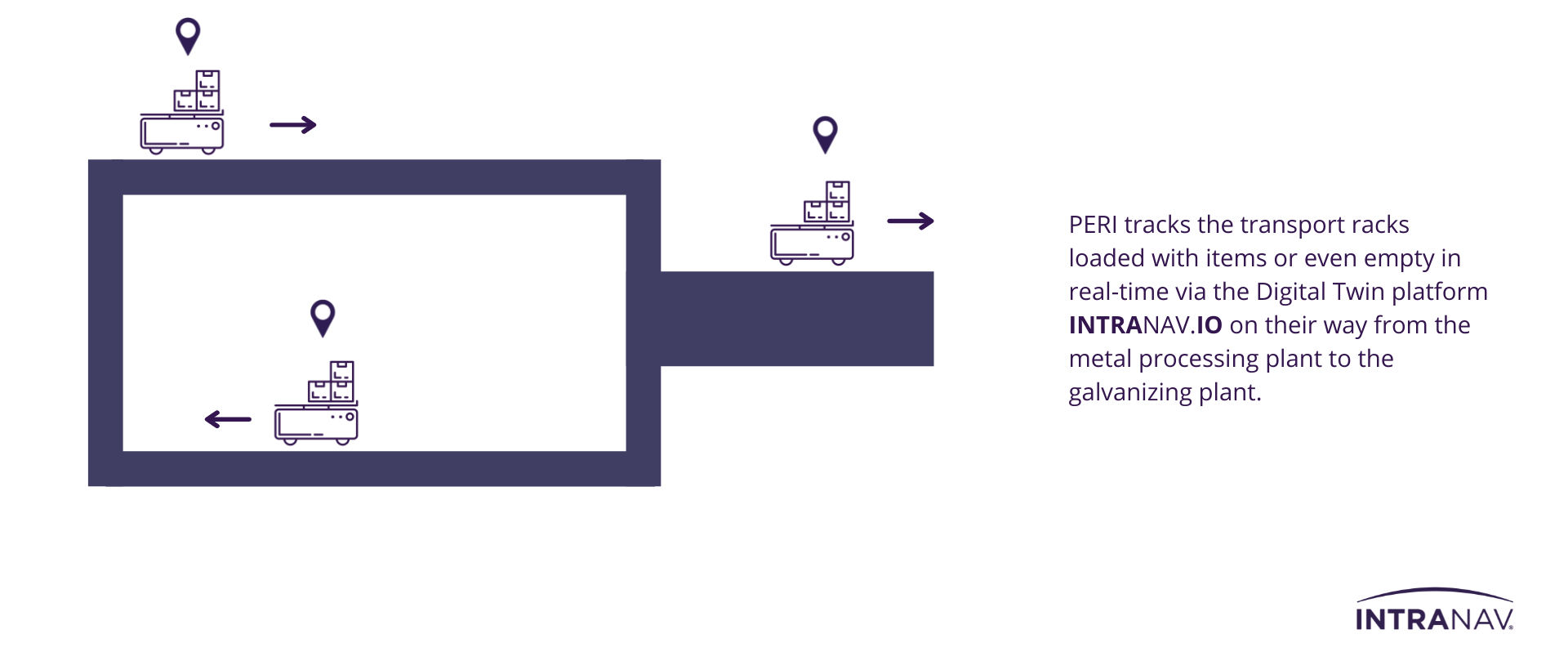
The scaffold manufacturer tracks the transport racks loaded with articles or unloaded in real-time via the Digital Twin platform INTRANAV.IO on their way from the metal processing plant to the galvanizing plant. The entire material flow between the fully but also partially semi-automated production, which is carried out by driverless transport vehicles (AGVs), is digitized via INTRANAV.
The IoT platform is displaying live the production progress with the transport orders of the AGVs and their quantities. In the event of disruptions or bottlenecks, an alarm indicates the process deviation so that responsible employees can intervene immediately.
Dynamic FIFO Process
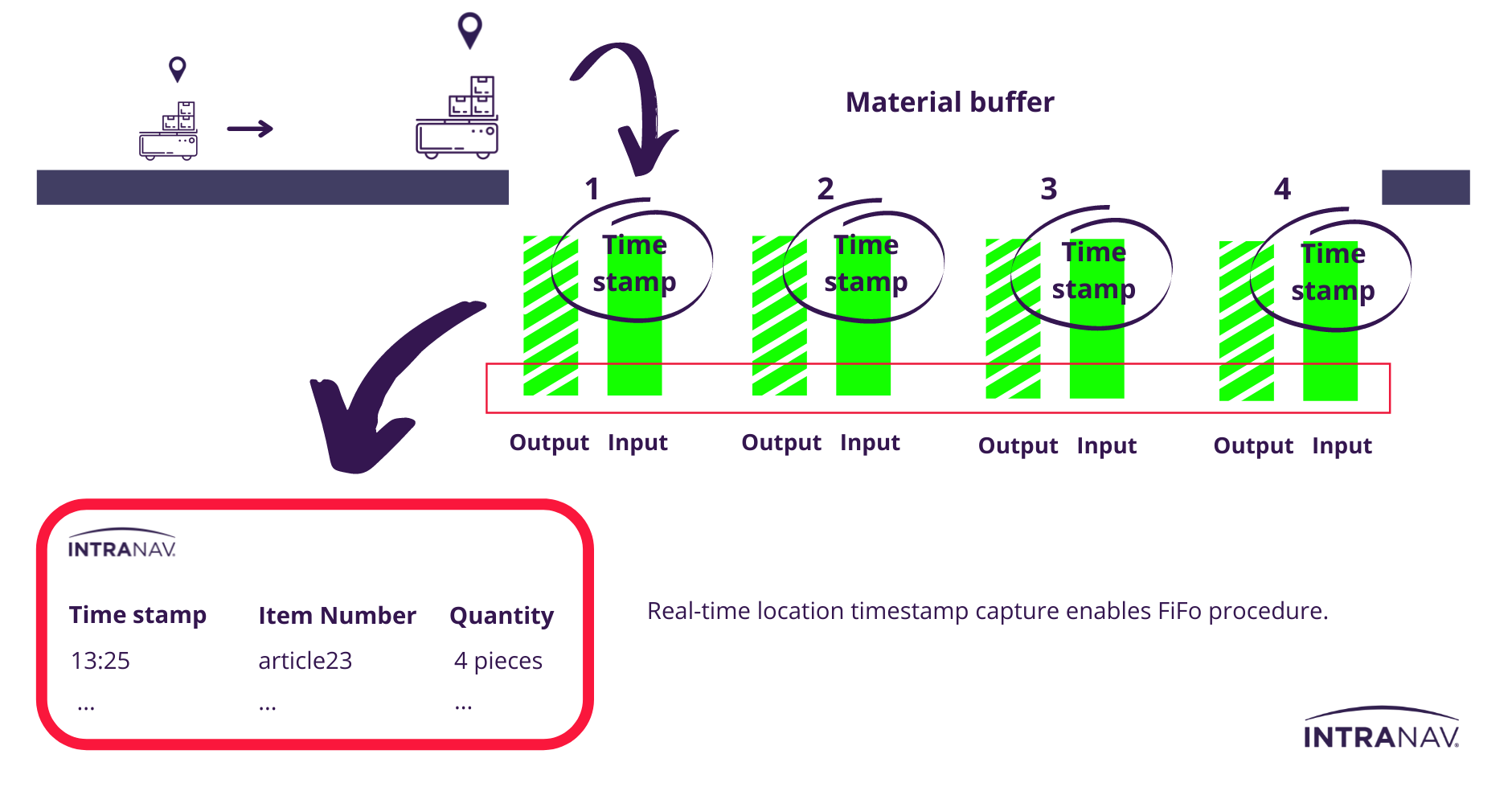
After transport by AGV/FTS, the transport rack is unloaded into one of four material buffers (depending on the article) at the galvanizing plant. By a conveyor system, articles are hung up in the galvanizing plant according to the FIFO principle.
The transport point of the FIFO line must be identified and article number and quantity must be displayed on a screen at the FIFO line. Here, the sequence of the transport racks is defined on the basis of the timestamp of the import into the respective geofence. The real sequence of the transport racks must be mapped accordingly on a screen via INTRANAV.IO. The respective following transport rack in the material buffer lies with its long side directly against the previous transport rack. If the transport rack leaves the material buffer on the output section of the material buffer, the information on the monitor disappears and of the following information of the transport, rack appears. The distance between the input and output sections is at least 3,000 mm (length of the transport rack).
Analysis of resource utilization
Through an interface, the real-time tracking data is imported in a structured format into industrial analysis software, which analyzes the overall resource utilization of AGVs and transport racks. The examination of the utilization and transit times, such as downtimes or throughput times, help to identify weak points and improve them for the further course of production.
Solution
Through the INTRANAV Digital Twin, the progress of the control station of the material and transport process can be checked at any time. The integration of the article data into the respective rack allows to completely eliminate the use of paper accompanying slips. The evaluation of the real-time position data helps the manufacturer to constantly optimize the transport and production processes.
Summary of the results achieved by our customer with INTRANAV:
● The automatic allocation of the transport racks in the loading stations avoids the risk of mistakes, which helps to speed up the loading process.
● The real-time location tracking of the load carriers ensures direct traceability and real-time-based status determination of the transport. The production progress can be tracked in real-time via the control station using the indoor map. The alert function increases the process reliability of the material transport, enabling fast intervention in the event of process delays.
● The dynamic FIFO process enables implementation and compliance according to the lean production design.
● With the practical, paperless material and transport handling, no manual data entry is required anymore. Individual retrieval times such as article number & quantity of transport racks and articles are automated via a monitor.
● The evaluation of the real-time data by integrating it with other analysis software enables the continuous and deeper optimization of the resource utilization of the transport process within the production.
Benefits of the INTRANAV SMART Factory Solution
- Benefit:100% process transparency about the material transport of the AGVs
- Benefit:Search times are significantly reduced
- Benefit: Increasing the process reliability of transport handling
- Benefit: Minimization of process deviations
- Benefit: Real-time timestamp reduces process deviations of the FIFO process
- Benefit: Minimization of idle time and throughput times by analyzing resource utilization
- Benefit:Digital handling eliminates manual data entry efforts. Freed-up working time can be invested in more value-added work.
- Benefit: Control capacities are 100% scalable.
INTRANAV offers a highly flexible and cost-effective enterprise solution, ideal for automotive, aerospace, logistics, or production. Further fields of application are for example in the field of production line automation; automatic clock feedback into SAP systems, line balancing/production leveling by INTRANAV SMART Warehouse Solutions, “Just in Sequence” – provision for the right sequence, plausibility checks, or zone-based control of automatic programmable logic controllers.
Our INTRANAV Production Solution might also be interesting for you, contact us to talk about optimization possibilities for your production and logistics workflows!