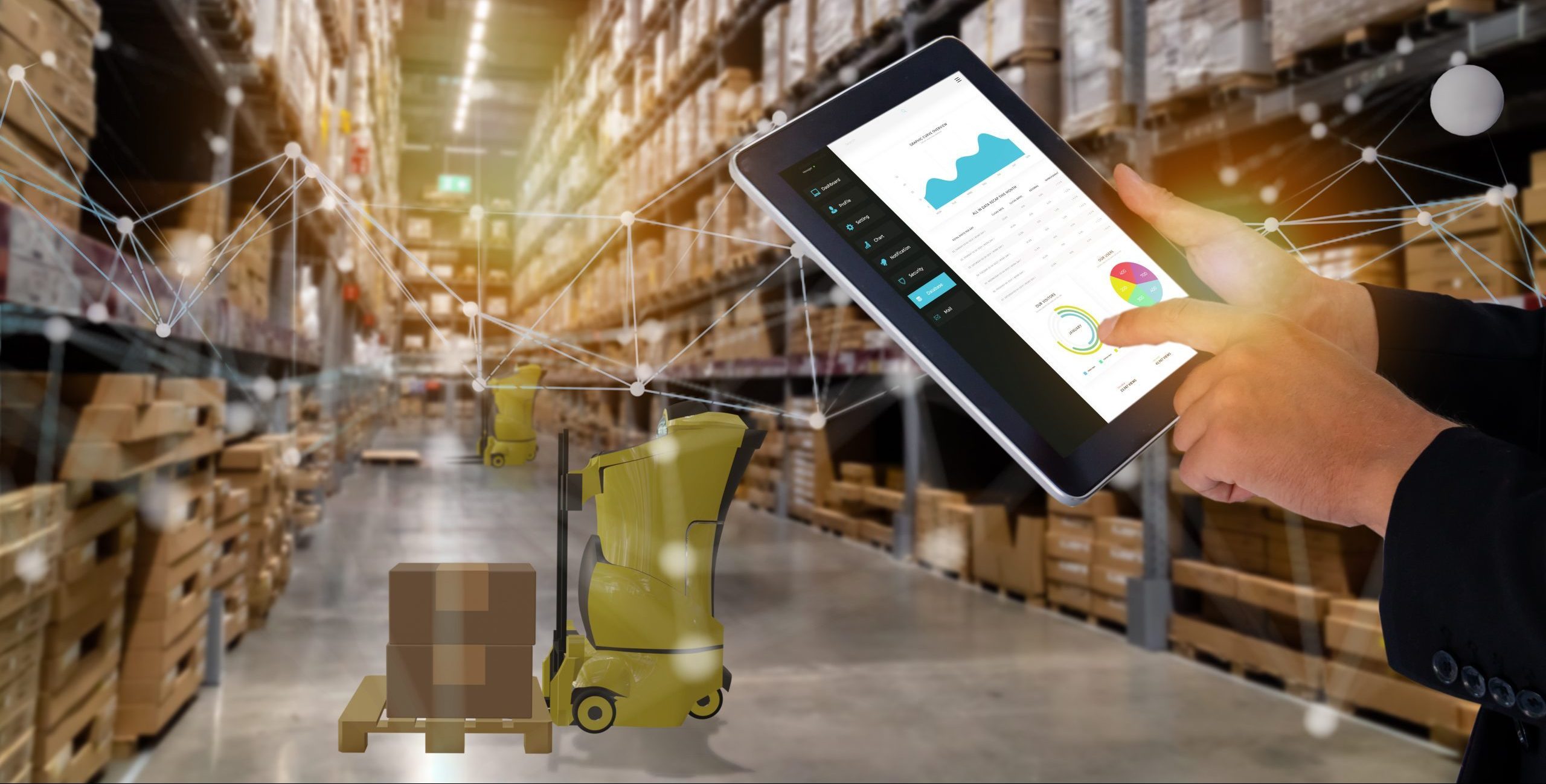
INTRANAV Warehouse Automation
Digital Warehouse Solution
Digital Automation & Collaboration
for your SMART Warehouse
Within the intelligent warehouse, all assets (physical objects such as boxes, tools or aids) as well as (autonomous and manual) vehicles are uniquely addressable and identifiable so that any change in status can be detected and reacted to through digital networking.
Industry 4.0 provides various technology solutions for automatic identification (AutoID), such as UWB, RFID (and others), which can all be implemented and managed with the INTRANAV Multi-Technology Stack platform. INTRANAV Real-Time Location Data is the prerequisite for reliable and automatic order, freight, and shipping information acquisition. With real-time data via the Digital Twin, you ensure a smooth exchange of information between all store floor participants.
INTRANAV Real-Time Location Data
controls your intralogistics
- Automatic identification of status, booking and process steps
- eKanban: Automated process-trigger trough virtual zones
- Intelligent container management as package compound (bulk process)
- Assistance Guiding & Control for AGVs
- Paperless Factory & Keyless Control
-
Via the INTRANAV.IO platform, you can define virtual zones (geofences) on any area of your logistic shopfloor to identify booking processes scanerless, such as incoming and outgoing goods, intermediate storage, or transport processes in real-time to book them fully automatically coupling to an ERP/WMS system.
INTRANAV.RTLS TAGs are attached to the respective asset, the INTRANAV.RTLS NODEs read the location information in real time and transfer this information to the IoT RTLS platform.
-
Similarly, the initiation of further (eKanban) processes works, except that in this case an “if-then scenario” must be defined via INTRANAV.IO, which is automatically recognized by moving into a geofence (virtual zone). Scenarios in connection with the ERP/EWM system can be synchronized, updated, and simultaneously triggered automatically.
INTRANAV.RTLS and INTRANAV.IO, in connection with other systems, control the entire logistics process in the warehouse using real-time location data: from the entry of incoming goods, to incoming goods control, storage, consolidation, and outgoing goods.
-
INTRANAV Warehouse Solutions allows for automatic incoming goods inspection as a bundle (bulk process) using RFID TAGs, which guarantees complete real-time batch tracking of all containers.
In this process, the cardboard boxes are provided with RFID TAGs by the supplier, and labeling of the individual items within the boxes is not necessary. By linking the SSCC (number of the shipping unit) and carton number to the RFID TAG UID (Unique Identifier), a consistent number range is created, which creates the reference from the goods content to the RFID label. So that the cardboard boxes, which must be equipped with an RFID gate, can be checked for completeness when passing through the goods receiving area. The packages are then loaded onto pallets according to their type. You already save one scan step!
The finished package groups are also transferred to the ERP system as a virtual package group. The INTRANAV.IO platform uses real-time data to generate the digital twin of the booking and warehouse processes. The data of the parcel network is then transferred to the SAP Business One ERP system via INTRANAV.IO interfaces.
Precise INTRANAV real-time positioning eliminates the need for further scanning processes even when the parcel network is (put into and taken out of) storage in the high-bay warehouse system. This is because the intelligent INTRANAV UWB VehicleTAG with external RFID sensors recognizes the parcel compound as well as the storage location and posts them automatically and in real-time as “goods posting”.
Read our Digitization Success Story from the field of eCommerce Logistic!
-
Driverless transport systems (AGVs) are extremely efficient, but they lack the overall view, i.e. real-time status information of all assets, vehicles, and persons on the store floor. With our intelligent AGV software add-on, AGV manufacturers can obtain real-time information about obstacles, changes, and location from other road users and load carriers, and use it to optimize their routes and alternative routes:
⦁ Avoid blind driving and collisions due to limited laser scanner range. The reference information of the SLAM card must be updated due to the changes on the large footprint. The area and paths are so large that the laser scanners with limited range can no longer detect any contours. The vehicle drives “blind”. INTRANAV SMART sensors can use location information as supporting information for “re-referencing” to avoid blind driving and to prevent it in the first place.
⦁ Intelligent, automatic maneuvering of AGVs on constantly changing logistics areas, as well as in confusing floor areas or around repositionable machines.
⦁ Automatic location of load carriers and collection after process completion (e.g. production of production pieces) by if-then control. INTRANAV Suite the exact position of the load carriers to be picked up, either as updated parking space information or as geo-coordinate suitable for the AGV coordinate system. The transport order is constantly updated with the current parking space information, or if it changes, this information is passed on to the AGV control software.
⦁ Assistance Guiding for AGVs to avoid traffic jams in transport aisles. INTRANAV distributes the latest real-time information at all times. AGVs can thus look “around the corner” and take action in advance. Route routes can also be optimized so that congestion situations can be avoided in advance. With this additional information, the AGV can bypass the problem.
Read our Customer Success Story: Sixth sense for AGVs “Mission Control in the Warehouse”!
-
[ Paperless Factory ]
INTRANAV relies entirely on the paperless factory, so we even do without e-labels or e-ink. All logistics data, such as transport orders, handling unit data, shipping bills or delivery note data of the respective asset are stored on the corresponding INTRANAV.RTLS TAG. The data is linked via ultra-wideband and communicated to the IoT platform. The variable data set can thus be retrieved at any time throughout the entire supply chain and supplemented with additional information.
Manual searches are no longer necessary, as all relevant data can be retrieved on the shopfloor using tablets, for example. The employee has all necessary data of the entire store floor in his hand.
[ Keyless Control ]
With INTRANAV Door Control you can ensure that dangerous or critical work areas are only entered by authorized personnel through automatic door control, without any danger of unauthorized persons entering.
INTRANAV RTLS Automation
Features
Real-Time Location Data and SMART Sensors for integrated networking and communication of all assets in the warehouse
-
Digital Twin of your assets,
± 10 cm accuracy -
Condition Monitoring
with INTRANAV SMART sensors -
Real-time alerts
-
Blind runs &
collision avoidance -
AUTO-ID &
Auto-Control -
Freely definable
virtual zones (geofences) -
(If-Then)
Rule Manager -
Goods receipt
bulk procedure -
Real-Time Analyses
(Trails, material flow etc.)
INTRANAV Warehouse Automation
Benefits
- Increase material turnover and reduce searches by eliminating manual scanning
- Unambiguousness about inventory
Reduction of error-proneness Posting steps (storage of goods, intermediate storage, transfer posting, write-off) - Early fault detection ensures quality improvement throughout the entire process
- Reliable, data-based information on the content, status, and position of goods in the warehouse, storage duration, and quantity
- Automatic and consistent implementation of FiFo, LiFo procedures
- Fully automated goods receipt including real-time goods receipt control, coupling to ERP systems ensure the necessary automatic activation of intralogistic follow-up processes
- Fewer IT interfaces:
No more need for additional programs for the individual preparation and structuring of notification data - Avoidance of email traffic in case of e.g. delivery errors (automated notifications / alerts)
It’s that simple!
-
Activate the INTRANAV
Plug & Play Solution -
Attach INTRANAV.RTLS AssetTAG (Tracker) at the asset, load cariier or AGV
-
Real-time tracking & sensor data monitoring of load carriers via the INTRANAV.IO platform
-
Scale INTRANAV Digital Twin Suite to any device