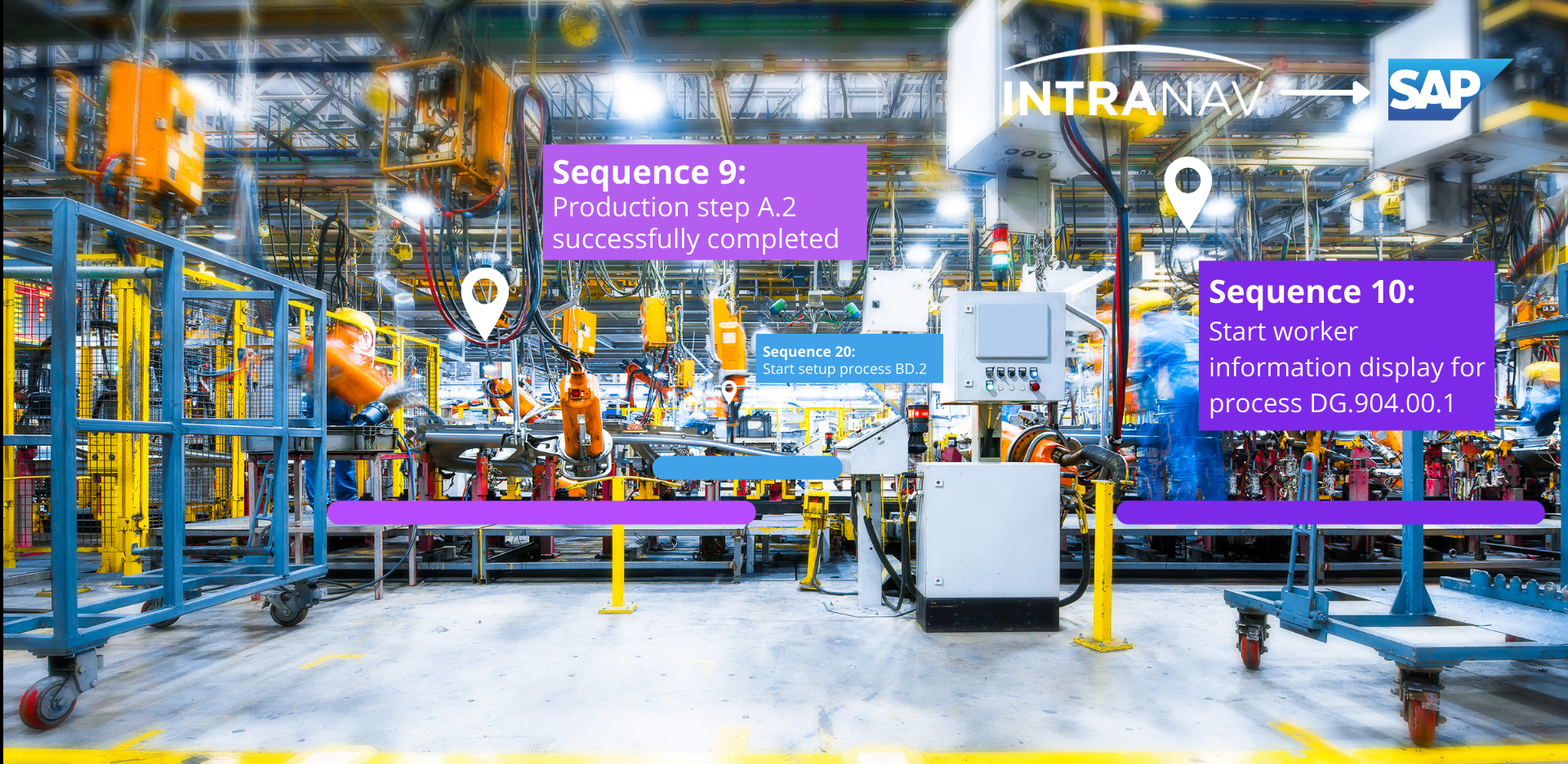
INTRANAV Smart Manufacturing Solution
Digital Twin Controls Industrial Manufacturing Complexity:
Automating Manual Manufacturing Steps with Production Line Digitization from INTRANAV
With an ever-increasing range of model variants to be produced, the question arises as to how the high complexity of production, especially in variant production, can be monitored, time-consuming and error-prone scanning processes dispensed with, and all quality standards continuously maintained. The key to success is the combination of process virtualization with real-time indoor track & trace data and digitized workflows that automate previous manual processes in manufacturing to a high degree. For production to flow smoothly, pre-assembly and main assembly must be synchronized, otherwise specified order time windows cannot be met and production delays occur. Plausibility checks prior to main assembly must be reliable and automatic, as incorrect assembly can lead to considerable time and cost expenditures as well as safety risks. INTRANAV provides valuable real-time location data for process optimization and automation to optimize your production processes as well as material supply and flow. With INTRANAV, documentation and traceability of your processes is available at the push of a button via reports. With the new automated processes and workflows through highly accurate real-time location data, you are able to avoid bottlenecks, shortages, errors and significantly reduce search times.
Optimization Potential in Production
-
Basis for plausibility of pre- and main assembly synchronization of the cycles
Reduction of material merging errors
Thanks to continuous real-time tracking of the frames, the entire manufacturing process is transparently mapped as a digital twin. System comparisons with SAP check the plausibility of the components for the further assembly process.
-
Scan-free infrastructure
Reduction of booking efforts and errors
Through virtual zones, all cycle-related production feedback is automatically posted to SAP in real time.
-
Improve cycle utilization and control
Reduction of idle cycles and idle times
The Real-Time Digital Twin enables production planners to plan material and production times in advance.
-
Control of variant production
Compliance with the quality assurance of the individual production steps
End-to-end tracking of the load carriers in the respective cycle enables production managers to check at any time whether the production steps are running synchronously and to be alerted in case of KPI deviations.
-
Optimized material flow of the production line
Minimization of production planning effort through retrograde real-time analyses
Through real-time data collection and KPI reconciliations of the new automated processes, bottlenecks, shortages, dwell times, cycle time, unnecessary stops, disruptions, delays, process length or total time taken to complete a cycle can be analyzed.
-
Automatic and efficient material replenishment
Reduced material delivery times through automated replenishment control
Through real-time data-driven production line feeding by tugger train or the digitized forklift fleet.
INTRANAV Smart Manufacturing Solution:
Real-Time Data-Driven Process Automation
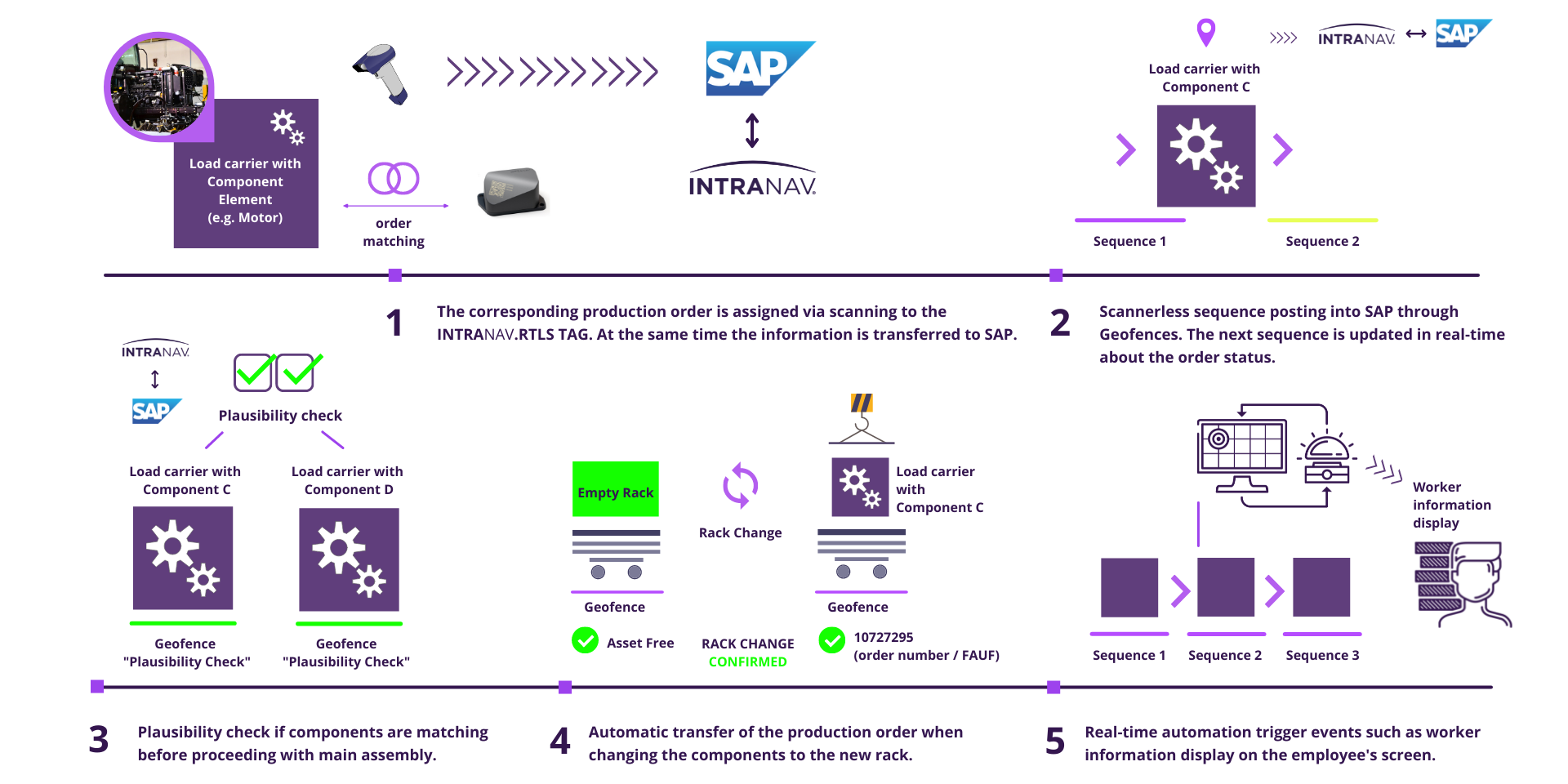
How Smart Manufacturing Works With INTRANAV
-
Order Matching with RTLS – Generation of the Digital Twin
Before a single component runs through the assembly, an order matching (systemic marrying) of the INTRANAV.RTLS TAG with the component in the SAP system must take place, so that the material flow can be tracked during the entire production process and automation processes can be triggered to the correct component. With the INTRANAV.APP “Order Matching”, an initial scan step in the Start Zone/Paring Zone systemically marries the corresponding production order (FAUF) with the TAG located on the rack. In addition, further manufacturing accompanying documents can be stored virtually in the system, enabling digital, paperless handling throughout the entire manufacturing process. This ensures process reliability throughout the entire assembly process, thus eliminating the possibility of production information being lost or accidentally mixed up. -
Real-time location along the production line
By equipping INTRANAV.RTLS on the production line, the workers receive (±) 10 cm accurate real-time location information of all assembly steps as well as of the boxes, containers, load carriers and racks located on the assembly line, which are manually moved from cycle to cycle. This real-time information is digitized in INTRANAV.IO and sent to the SAP PP (Production Planning and Control) system via an interface. The entire production flow is completely transparent and can be tracked in real time as a Digital Twin.
Workers can thus see in real time: which components and which material are in the respective cycle, where material replenishment may be required, whether the production steps are running synchronously or whether there are time deviations, or even to what extent delays are to be expected in individual sections.In the event of KPI deviations, production managers are notified immediately by alerts so that they can initiate appropriate intervention measures.
-
Automatic (scan-free) cycle feedback on the production line: INTRANAV transmits real-time data to SAP ERP
INTRANAV controls the production line by automatic feedback after each started and completed production cycle. The tracked racks on which the production pieces are located are manually pushed from cycle to cycle, each time passing through a virtual zone, whereby the cycle sequence is automatically posted as “completed” in SAP PP, so that the next cycle is informed in real-time about the status and can start with the next step. Automatic cycle feedback ensures quality standards and eliminates manual scanning within the line. Booking errors are thus eliminated so that no process step is omitted. This saves time for the workers, as manual scanning is no longer necessary. Late or early posting due to manual scanning can have critical consequences for the production line, such as excess material at the tightly scheduled storage/assembly area or idle time, which in turn leads to inefficiencies in the entire supply chain process flow. With the link to SAP PP (Production Planning and Control) and SAP EWM (Extended Warehouse Management), information can be provided at higher levels, triggering follow-up order and information processes. -
Elimination of scanning and booking steps
By means of virtual zones, which are individually defined for each cycle via the INTRANAV.IO platform, manual scanning and booking processes are replaced by auto-bookings (auto-ID). The information is transferred to the SAP PP system via the interface. Time-consuming manual processes carried out by workers, such as scanning the barcode of the machine card in order to book operations or material, are automated on a cycle-by-cycle basis with INTRANAV. This reduces incorrect bookings and speeds up the production process, as the workers can now spend more time on value-added work.INTRANAV Auto-ID alone enables automatic material postings, cycle-related operation postings, plausibility checks.
-
Sequence monitoring: Automatic (scanner-less) plausibility check of the components
The real-time location data is collected within the production line using INTRANAV.RTLS TAGs, which are installed on the assembly carts. These each contain corresponding ID group addresses to tell the system which TAG is responsible for which assembly area. Thus, for the assembly trolleys (racks) of “Product A”, there is a separate numerical group for the pre-assembly of the “engine”, for example, as well as for the assembly trolleys in the main assembly line. Analogously, this also applies to production line B. Thus, each INTRANAV.RTLS TAG has its own, area-internal address. This means that the assembly units are digitally networked and can track the production orders paperlessly in all assembly branches.
With the INTRANAV.APP “Assembly Check” the final plausibility check takes place whether the components may be assembled with each other. In two geofences, it is checked whether the individual component fits to the corresponding assembly before it goes on to the main assembly. This involves a systemic comparison in SAP. A monitor shows whether the components fit together or not.This important component check ensures that only matching components and groups are assembled together. This avoids particularly time-consuming and costly rework, and ensures the ongoing quality and correctness of the processing of all further production steps. Process assembly errors are avoided.
The basis for the plausibility of pre-assembly and main assembly synchronism of cycles, cycle-related picking (large components), generation of transport orders, cycle-related option display are implemented by INTRANAV.
-
Automatic (scanner-less) order transfer when changing the rack
At a defined point in the assembly process, a rack change must be carried out for production-specific reasons. An event trigger triggers the release for the rack change via two geofences. The components are transported from one rack to a new rack. Since the racks are equipped with the INTRANAV.RTLS TAGs, an automatic transfer of the information of the FAUF from the old rack to the new rack must also take place here. The INTRANAV.APP “Rack Change” ensures the automatic transfer of the FAUF from the old to the new rack. No scanning process is necessary. The TAG of the old rack is automatically reset so that new information can be written to it. The INTRANAV.APP “Rack Change” displays “Rack change confirmed” via a monitor as soon as this process has been successfully completed.
This process step ensures seamless transition of information transfer and secures further production tracking. Manual, erroneous and time-consuming scan-based handling is no longer necessary, and the dangers that arise from paper accompanying slips, such as the risk of confusion or loss, are completely eliminated with INTRANAV. -
Cycle-related automation triggers
INTRANAV.IO can be used to set up additional geofences and triggers to call up production order-related information (options), as well as to start additional setup processes for fixtures, e.g. by means of a programmable logic controller (PLC).This includes for example:
– Checklist call at Q-gates
– Option display of worker information
Production Controlling for Result-Oriented Lean Production Planning
With the new automated processes and workflows through highly accurate real-time data, you are able to avoid bottlenecks, shortages, errors and significantly reduce search times. The generated real-time location data helps you identify optimization potential on the production line and detect weak points and waste. With an automated and intuitive database, retrograde analyses and calculations can be performed at any time. This gives you an overview of the past with the potential to minimize planning effort and production forecasting of the material flow in the future:
- KPI comparisons as a status report: dwell times, throughput time, unnecessary stops, disruptions, delays, process length.
- FLOW Status Report: The total time taken for a complete cycle, including dwell times and cycle time can be analyzed at the push of a button
- TRAIL Reports: Analyze whether your vehicle fleet follows predefined and at the same time efficient routes (e.g. for line feeding)
- HEATMAP Reports: Identify high-traffic intersections and the duration of stay of your transport vehicles and materials, as well as where traffic jams, waiting and control times are particularly frequent.
- ZONE REPORTS: Analyze, for example, which buffer zone, which production cycle was occupied and for how long, in order to optimize and adjust capacity planning. Or whether transport vehicles actually supplied the prescribed zones on the production line and how long they stayed in the areas.
- Real-Time Analytics Dashboards: By connecting to third-party providers, INTRALYTICS offers the ability to visualize your valuable INTRANAV Real-Time Location & Sensor data via an unlimited number of analytics dashboards. Use reports that meet your needs to ensure long-term optimization success for safe process operations and lean production.
Improving Material Supply at the Assembly Line through Dynamic Material Replenishment
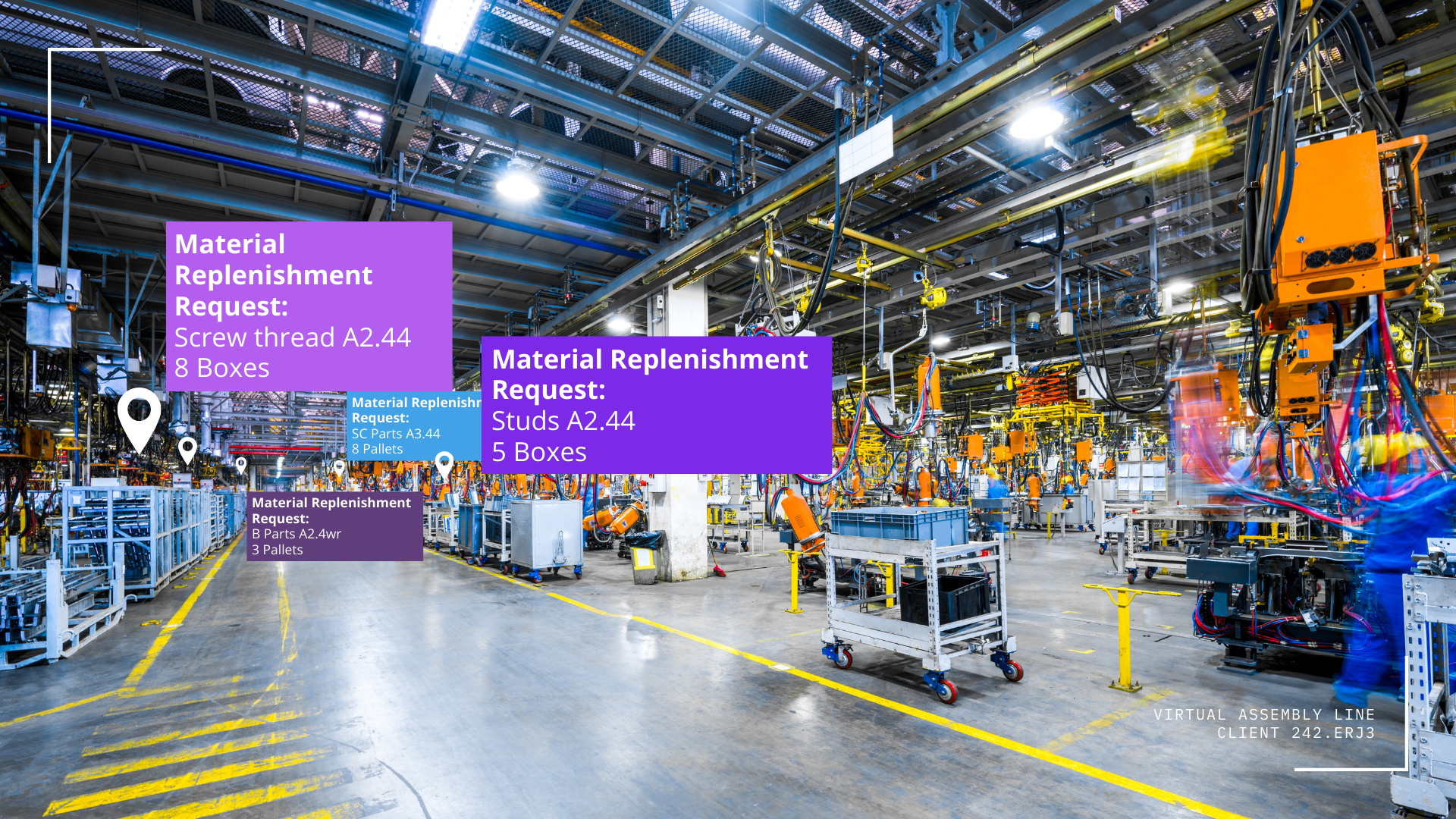
Dynamic line feeding with tugger trains
Take your material replenishment to the next level, reduce up to 40% of empty and throughput times with dynamic route train management. Integrate INTRANAV Real-Time Location Data (RTLS) with SAP Extended Warehouse Management (EWM) to enable process-safe and time-efficient transportation flow management for route trains. Reduce the error rate of the replenishment process by INTRANAV real-time status monitoring in the SAP Warehouse Management Monitor. Actual and target comparisons of processing times help you calculate routes. Manual bookings during the replenishment process are replaced by automatic system bookings. Automated replenishment control ensures efficient and timely material availability at the line.
Replenishment with the digitized forklift fleet
Real-time data-driven transport orchestration and scan-free material transport with the digitized forklift fleet help you optimize material supply on the production line. Driver navigation speeds up material delivery via the shortest path, and integrated safety sensors ensure collision avoidance. Improve your replenishment by detecting bottlenecks, downtimes and transport interruptions through flow status reports with INTRANAV. Benefit from INTRANAV’s process virtualization platform by transforming your manual workflow into a fully automated workflow with Auto-ID for automatic goods and transfer order posting!
Learn more ➜ Virtual Material Replenishment on the production line: Route train vs. forklift truck
True Value through the
INTRANAV Smart Manufacturing Solution
-
- Benefit: From the “production black box” to a 100% real-time assembly line overview and thus to full process transparency in the entire (variant) production – digitally retrievable as a digital twin.
- Benefit: Cost/benefit and time expenditure caused by assembly errors, cycle delays, manual scanning, and inspection efforts are significantly reduced.
- Benefit: Reduction of search times
- Benefit: Control capacities are now 100% scalable
- Benefit: Scanner-based posting now takes place 99% end-to-end through automatic cycle feedback and work step posting in SAP PP. (*1% exception due to the first initial scan step)
- Benefit: Booking errors are eliminated
- Benefit: The plausibility check increases process reliability and enables a potentially higher work speed through automated part matching, which can only be automated through constant real-time tracking. Quality assurance for the further assembly process is thus guaranteed.
- Benefit: Material merging errors significantly reduced
- Benefit: INTRANAV.APPs enable a seamless transition to tracking of the production piece including FAUF, where normally scanning processes or other manual operations are necessary for data transfer. Process assurance and associated material flows are optimized.
- Benefit: The cycle-related automation triggers ensure automated retrieval of worker information, such as Q-Gate checklists. The work process flow is thus significantly facilitated
- Benefit: The link to the PLC enables the automated triggering of cycle-specific production processes. The material flow is thus accelerated and at the same time made safer
- Benefit: Material availability is optimized by dynamic line feeding
The INTRANAV EDGE IoT Suite.
An enterprise platform that combines all RTLS competencies and technologies.
-
The Digital Twin platform manages the real-time location data generated for all assets. Basic configurations such as creating and editing geofences, rules, filters, flaggs are done directly in the platform. Live map view provides process visibility throughout the manufacturing flow. Alerts provide immediate notification of KPI deviations. Predictive maintenance in this case is mainly used for TAG management (battery life, etc.).
➜ Learn more about the industrial IoT RTLS platform!
-
02.1 _INTRANAV.APP Order Matching
Before a single component runs through assembly, an order matching (systemic marrying) of the INTRANAV.RTLS TAG with the component in the SAP system must take place so that the material flow can be tracked throughout the production process and automation processes can be triggered to the correct component. With the INTRANAV.APP “Order Matching”, an initial scan in the Start Zone/Paring Zone systemically marries the corresponding FAUF to the TAG located on the rack.
____________________
02.2 _ INTRANAV.APP Assembly Check
The INTRANAV.APP “Assembly Check” is used for plausibility checks of the great diversity of components in variant production. In two geofences, before moving on to the main assembly, it is checked whether the individual component fits the corresponding assembly. This involves a systemic comparison in SAP. A monitor shows whether the components match or not. This important component check ensures that only matching components and groups are assembled together. This avoids particularly time-consuming and costly rework, and ensures continuous processing of the subsequent production steps. Process assembly errors are thus avoided.
____________________
02.3_ INTRANAV.APP Rack Change
At a defined point in the assembly process, a rack change must be carried out for production-specific reasons. An event trigger triggers the release for the rack change via two geofences. The components are transported from one rack to a new rack. Since the racks are equipped with the INTRANAV.RTLS TAGs, an automatic transfer from the old rack to the new rack must also take place here. The INTRANAV.APP “Rack Change” ensures the automatic transfer of the FAUF from the old to the new rack. Here, no scan process is necessary. Furthermore the TAG is made automatically with the old rack an automatic reset of the information, so that this can be written again with new information. The INTRANAV.APP “Rack Change” displays “Rack change confirmed” via a monitor as soon as this process has been carried out successfully.
➜ Learn more about the INTRANAV.APPs !
-
INTRANAV.RTLS NODEs
The INTRANAV.RTLS NODE is a Time-Difference-of-Arrival (TDoA) intelligent UWB antenna and is part of the INTRANAV.RTLS tracking infrastructure. The Node receives the signals from the INTRANAV.RTLS TAGs and calculates the positions in the backend. At least 4 NODEs are needed to calculate a 2D/3D position. The NODEs are precisely wireless synchronized and very easily scalable and virtually maintenance free. They are designed for harsh industrial environments and still have an attractive design.
____________________
INTRANAV.RTLS AssetTAG Pro
INTRANAV.RTLS AssetTAG Pro is our high performance UWB-TAG (tracker) with superior battery life, even at very high data rates. It is robust and specially designed for racks and load carriers. Thanks to the Lithium Baby-C primary cell, the AssetTAG Pro is ideal for runtimes up to 10 years at wide temperature ranges.
-
04.1_INTRANAV Fiori App integration into SAP PP
Through the SAP Launch Pad tile, the necessary one-time order matching is performed before the first takt of pre-assembly begins.
The INTRANAV Real-Time Location data is integrated into SAP through the open interface. The production orders are thus referenced in the SAP Production Planning and Control System, assigning an order to all associated assembly trucks; from pre-assembly and main assembly to loading of the machines in the plant, to staging in the yard and handover to the shipping company.
____________________04.2__SAP OData interface
The interface to OData enables the automatic posting “Component completed in cycle X” into the SAP system.
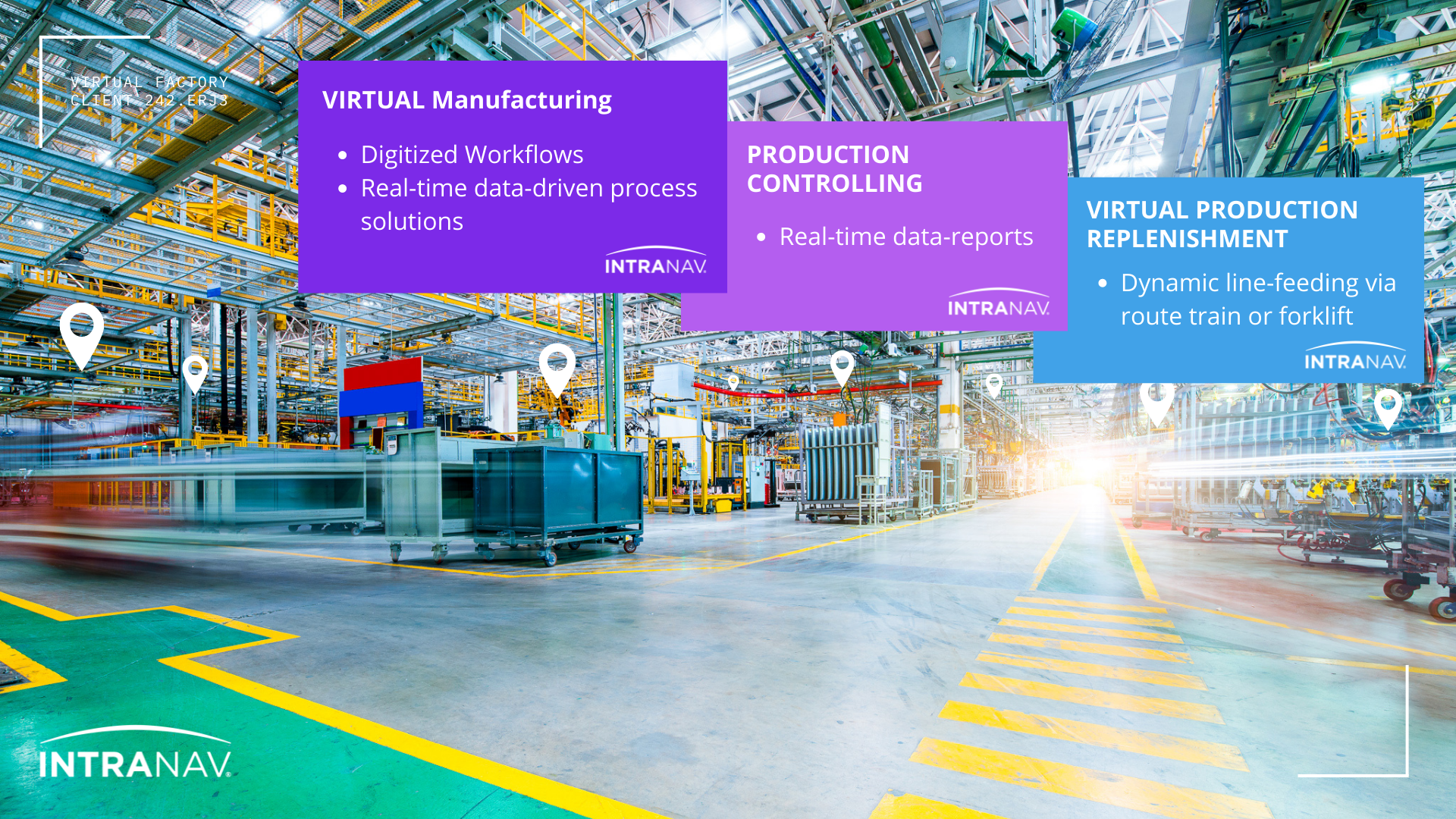
Advantages of Using the
INTRANAV Smart Manufacturing Solution
➜ End-to-end transparency over the production line through virtualization of all production cycles.
➜ Basis for the plausibility of pre-assembly and main assembly synchronization of cycles
➜ Cycle-based picking (large components)
➜ Automatic generation of travel orders
➜ Cycle-related information display for workers
➜ Compliance with quality assurance of individual production steps
➜ AutoID: Hundreds of daily manual scanning operations on the production line are replaced by the automatic cycle feedback provided by INTRANAV
➜ Acceleration of the production process, or increase of the output quantity
➜ Reduction of procurement costs for scan products
➜ Minimization of sequencing errors
➜ Reduction of expensive rework costs
➜ Empty cycles and idle times are minimized by the predictive, transparent workflow created with INTRANAV
➜ Avoidance of excess material on the delivery area; only the material that is actually needed is ordered via automatic production triggers. This saves valuable space, which is generally limited on the line
➜ The provision of limited available special load carriers is increased by INTRANAV. The transport routes, as well as the arrangement of the special load carriers, can be optimally planned in advance according to work requirements or requested from workers at short notice.
Contact us!Process transparency and workflow automation
with the INTRANAV.IO Suite
-
INTRANAV.IO
Learn more -
Digital Solutions
Learn more -
RTLS Applications
Learn more