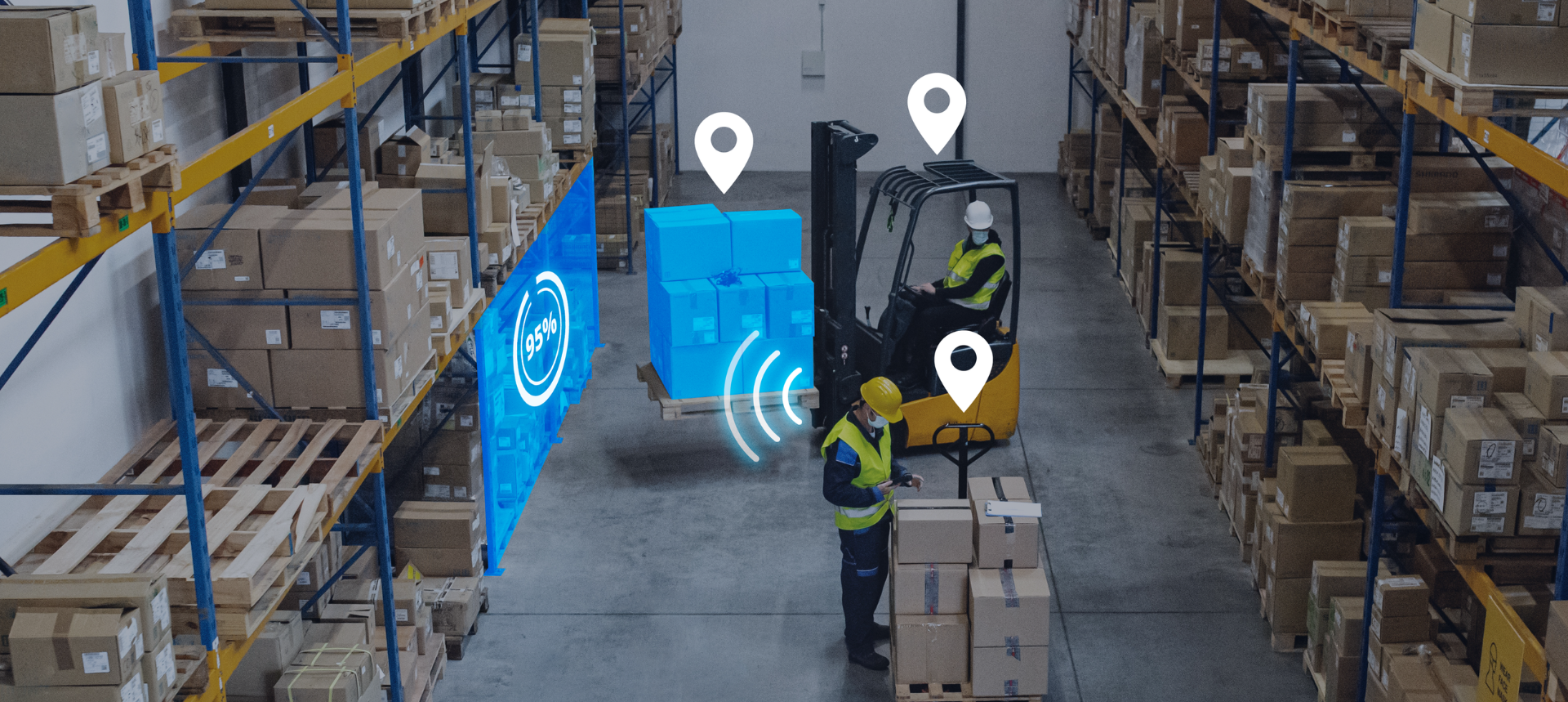
INTRANAV Smart Warehouse Solution
Intelligent and automated transport and goods handling processes for higher productivity in the warehouse
We track industrial assets in motion and ensure that you increase the overall efficiency of your goods and transport flows with INTRANAV. The main goal is to reduce manual handling in intralogistics and replace non-value-added activities with quality-assuring, value-added processes. INTRANAV’s innovative IIoT platform enables process automation with location/RF technology.
By digitizing your forklift fleet, you optimize the entire flow of transport and goods. Scannerless end-to-end movements from inbound to outbound process, eliminate time-consuming and error-prone manual work processes. Automated transport flow management allows goods movements to be automatically recorded and tracked, Auto-ID solutions with integrated UWB & RFID technology enable fast and process-reliable processing.
Warehouse optimization potential
through INTRANAV
-
Optimization of material handling
+25% Optimization of material flow utilization (OEE)
Through intelligent networking of location & sensor data from MHE & Material together with modern ERP and WMS management systems.
-
Efficient use of shop floor resources
-40% reduction in idle and throughput times
Through real-time optimization of transport orders, resources, intelligent routing and the elimination of barcode scanning through AUTO-ID and recognition systems.
-
Optimizing the workflow utilization
-15% Reduction of inefficiencies and errors in workflows
Through real-time process interlocking, digitized workflows, machine learning-based plausibility checks, predictive analysis and warnings.
-
Planning on-time delivery and ensuring quality
+10% Improvement of assembly line availability (up-time)
By reducing incorrect transports, misdirected shipments, process errors, and security risks as well as optimizing JIS and JIT production deliveries to the line with modern MES execution systems.
Maximum process optimization already achieved by customers with INTRANAV.IO & –RTLS
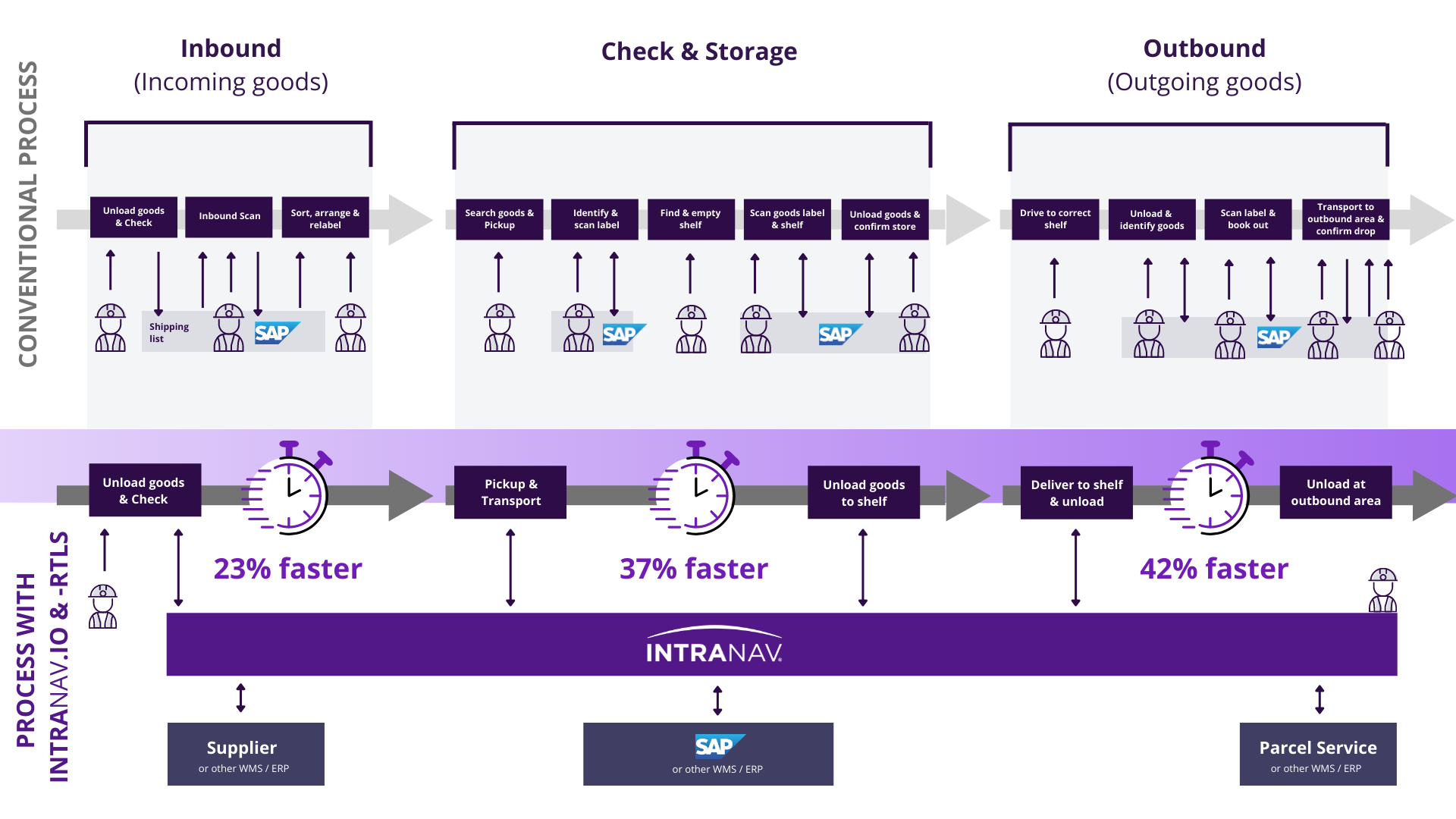
INTRANAV Smart Warehouse Solution
- Process Overview
- Inbound Shipments
- Instruction for Optimized Sorting and Palletizing of Goods
- Genration of Transport Jobs & Auto-ID
- Instructions for Forklift Driver
- Automatic Goods Posting into WMS
- Digital Twin of Shelf Occupancy
-
INTRANAV Smart Warehouse provides a comprehensive solution for the optimization of goods transport and warehouse processes. The application combines INTRANAV.RTLS hardware and software, including RFID, UWB and ultrasound, to efficiently manage the transport of goods (assets, load carriers, vehicles) in intralogistics and on the premises.
The INTRANAV.RTLS VehicleTAG+ is installed on the vehicle fleet (forklift, AGV, tugger train) and enables an optimized and scanner-free transport of goods. This eliminates manual scanning efforts for real-time registration of pallets, boxes and containers.
The application controls the flow of transport and goods using software-events. Automatic transport orders for the vehicles are controlled, and INTRANAV ensures optimal distribution of transport orders through a transport order pool. Forklift availability and optimized vehicle routing are taken into account.
The INTRANAV software also enables automatic booking of goods in the Warehouse Management System (WMS). This ensures accurate inventory management and seamless integration with warehouse management.
-
INTRANAV provides a practical overview of expected deliveries. By reconciling with the Warehouse Management System (WMS), the application enables a reliable display of expected deliveries in real-time.
With this feature, users can see at a glance which deliveries are expected in the near future.
Advantages:
– Real-time information: The application provides access to real-time information about expected deliveries. Users can be sure that they always have the most up-to-date data to make informed decisions.– Improved communication: The application facilitates communication between different departments and stakeholders. All stakeholders can access the same information and thus collaborate more effectively to ensure that expected deliveries are handled smoothly.
-
INTRANAV software optimizes the sorting and palletizing of goods by providing clear instructions to employees. An RFID reader on the scissor belt automatically scans each carton, eliminating the need for manual scanning. INTRANAV counts incoming goods and displays them clearly on a screen for employees. At the same time, the goods are posted as “Received” in the WMS.
The application also supports logistics employees in loading pallets according to type. The cartons are already provided with RFID labels by the supplier; alternatively, a QR code can also be used. If the supplier does not attach QR codes or RFID labels, the cartons can also be scanned once upon arrival at the warehouse.
Advantages:
– Efficient goods handling: the instructions for optimized sorting and palletizing enable faster and more efficient handling of goods.– Error prevention: The use of RFID readers or QR codes reduces human error in identifying and processing goods. The application ensures that the correct cartons are loaded and sorted, resulting in higher accuracy.
– Time savings: Clear instructions and the use of RFID labels or QR codes allow pallets to be assembled quickly and efficiently.
-
The INTRANAV software automatically creates a transfer order as soon as the goods are ready palletized and assigns it to the nearest forklift driver. In doing so, no manual creation of orders or assignments is required.
Furthermore, the application enables automatic identification of the picked pallet when the driver picks it up. No manual scanning is required. Instead, the driver is shown on the display which pallet he has picked up.
Advantages:
– Time savings: automatic creation of warehouse transfer orders eliminates the need for manual entry and assignment of orders.– Error reduction: Automatic identification of the pallet picked up minimizes the risk of errors during assignment.
– Increased efficiency: errors in allocation are avoided as the driver is clearly shown which pallet he has picked up.
– Real-time information: The application provides real-time information about the created transport orders and their assignment to the driver.
– Improved communication: the automatic creation of warehouse transport orders and their assignment to the driver improves communication between different employees and departments. All parties involved have access to the same information and can collaborate effectively.
-
The INTRANAV software automatically creates a transfer order as soon as the goods are ready palletized and assigns it to the nearest forklift driver. In doing so, no manual creation of orders or assignments is required.
Furthermore, the application enables automatic identification of the picked pallet when the driver picks it up. No manual scanning is required. Instead, the driver is shown on the display which pallet he has picked up.
Advantages:
– Time savings: automatic creation of warehouse transfer orders eliminates the need for manual entry and assignment of orders.– Error reduction: Automatic identification of the pallet picked up minimizes the risk of errors during assignment.
– Increased efficiency: errors in allocation are avoided as the driver is clearly shown which pallet he has picked up.
– Real-time information: The application provides real-time information about the created transport orders and their assignment to the driver.
– Improved communication: the automatic creation of warehouse transport orders and their assignment to the driver improves communication between different employees and departments. All parties involved have access to the same information and can collaborate effectively.
-
The INTRANAV software enables automatic booking of the goods in the WMS when the pallet is placed on the shelf, using RFID labels or QR codes on the shelf. This eliminates the need for the driver to dismount to check or scan the goods.
The application uses auto-ID technologies such as RFID to identify goods and locations. This enables precise recording of stock levels and accurate allocation of goods to the correct shelf locations.
In addition, INTRANAV uses position data by using Inpixon UWB-RTLS (Ultra-Wideband Real-Time Locating System) to locate forklifts in real time. This allows precise tracking of vehicles and their current positions in the warehouse.
Ultrasound is used to detect loading by sensing the goods on the forks of the forklift. This enables accurate monitoring of loading and prevents overloading or misloading of pallets.
Advantages:– Time savings: automatic booking of goods in the WMS during storage eliminates the need for manual recording and documentation. This saves time and reduces administrative effort.
– Optimization of warehouse processes: Automatic booking, precise identification of goods and storage bins, and accurate load recording all contribute to the optimization of warehouse processes. This leads to more efficient warehouse management, reduced effort and improved inventory management.
– Minimizing errors: The use of RFID labels or QR codes to identify goods and storage locations minimizes the risk of errors in inventory management. Accurate allocation of goods to the correct shelf locations reduces mix-ups and facilitates picking.
– Real-time monitoring: The use of Inpixon UWB-RTLS enables real-time location of forklifts in the warehouse. This allows warehouse staff to track the location of vehicles and identify bottlenecks or delays early and act accordingly.
– Accurate load detection: Sensory detection of goods on the forklift fork using ultrasound ensures accurate monitoring of loading. This helps to avoid overloading or incorrect loading, which improves the safety and stability of the transport.
-
INTRANAV enables visual representation of all shelf occupancy in the warehouse. With this application, you can see at a glance the current status of the rack capacity by visualizing the free racks in green color and occupied racks in red color.
Advantages:
– Real-time monitoring: users can instantly see which shelves are free and which are occupied without having to physically be on site.– Efficient use of resources: employees can quickly see which shelves are available and use them specifically for storing new products.
– Planning and optimization: INTRANAV enables better planning and optimization of warehousing. By analyzing shelf occupancy, companies can identify bottlenecks, predict space requirements, and improve inventory efficiency.
– Reduced out-of-stocks: with the help of the digital twin of shelf occupancy, companies can reduce out-of-stocks. Real-time monitoring enables warehouse staff to react quickly and order replenishment in time to avoid empty shelves.
– Error detection: the application helps detect errors in shelf stocking. If a shelf is incorrectly displayed as occupied, employees can correct the error and restore the correct occupancy.
Digitizing your transports with the intelligent Forklift
- Orientation: Recognition of vehicle direction for process safety
- UWB: RTLS Optimization for process areas and safety zones
- GPS-Precise: Nathless process tracking in indoor and outdoor areas
- RFID: Scanner-less goods transport (incl. Virtual Pallets)
- Fork Sensor: Detection of loading status and fork height
- Open API: Readout and use of vehicle data for process automation
- INTRANAV.IO: Automatic order processing from the central system (ERP, WMS, MES) and virtual orchestration
The VehicleTAG+
[ Precise transport vehicle location for indoor and outdoor tracking based on
UWB + RFID + GPS + LTE + WIFI technology ]
The new INTRANAV.RTLS VehicleTAG+ is dedicated to optimize efficiency (OEE), as well as to increase quality and flexibility in production & warehouse intralogistics.The VehicleTAG+ gets easily mounted on material transport vehicles such as forklifts and automated guided vehicles (AGV). With its precise and industrial proven real-time location Ultra-Wideband (UWB) sensor technology and Auto-Ident Technology based on RFID, the VehicleTAG+ enables the real-time Digital-Twin of your fleet in order to automate, optimize and simplify your material handling processes. Reduce manual barcode scanning and material identification to zero. Manage your mixed fleets and start to introduce a standardized layer for generating true values and benefits by using INTRANAVs prebuilt SMART Warehouse and SMART Production Solutions.
NEXT LEVEL production & warehouse intralogistics
with VehicleTAG+ as a digitization building block
- Transport optimization through digitalization of the forklift fleet
- Route optimization through navigation and route utilization reports
- Digital yard management; transport flow management through precise indoor and outdoor positioning
- Cost reduction through AutoIDent with integrated UWB & RFID RTLS technology
- Safety management enables collision avoidance and social distance management
- INTRANAV.IO: Automatic order processing from the central system (ERP, WMS, MES)
NEXT LEVEL IoT RTLS Technology
- Precise tracking of industrial trucks, forklifts and autonomous vehicles, suitable for indoor and outdoor use
- VehicleTAG+ is based on a multimodal technology layer with UWB, D-GPS RTK, Wifi and LTE
- Fast deployment through use of standardized technologies
- Sensor Hub for multiple RFID readers, height and weight sensors
- Fork sensor: Detect and record loading status and fork height
- Alignment: Detect vehicle direction for process reliability
- UWB location: RTLS optimization for process areas and safety zones
- Precise RFID scanners: Scanner-less goods transport (including “virtual pallets”)
- Open API: Readout and use of vehicle data for process automation
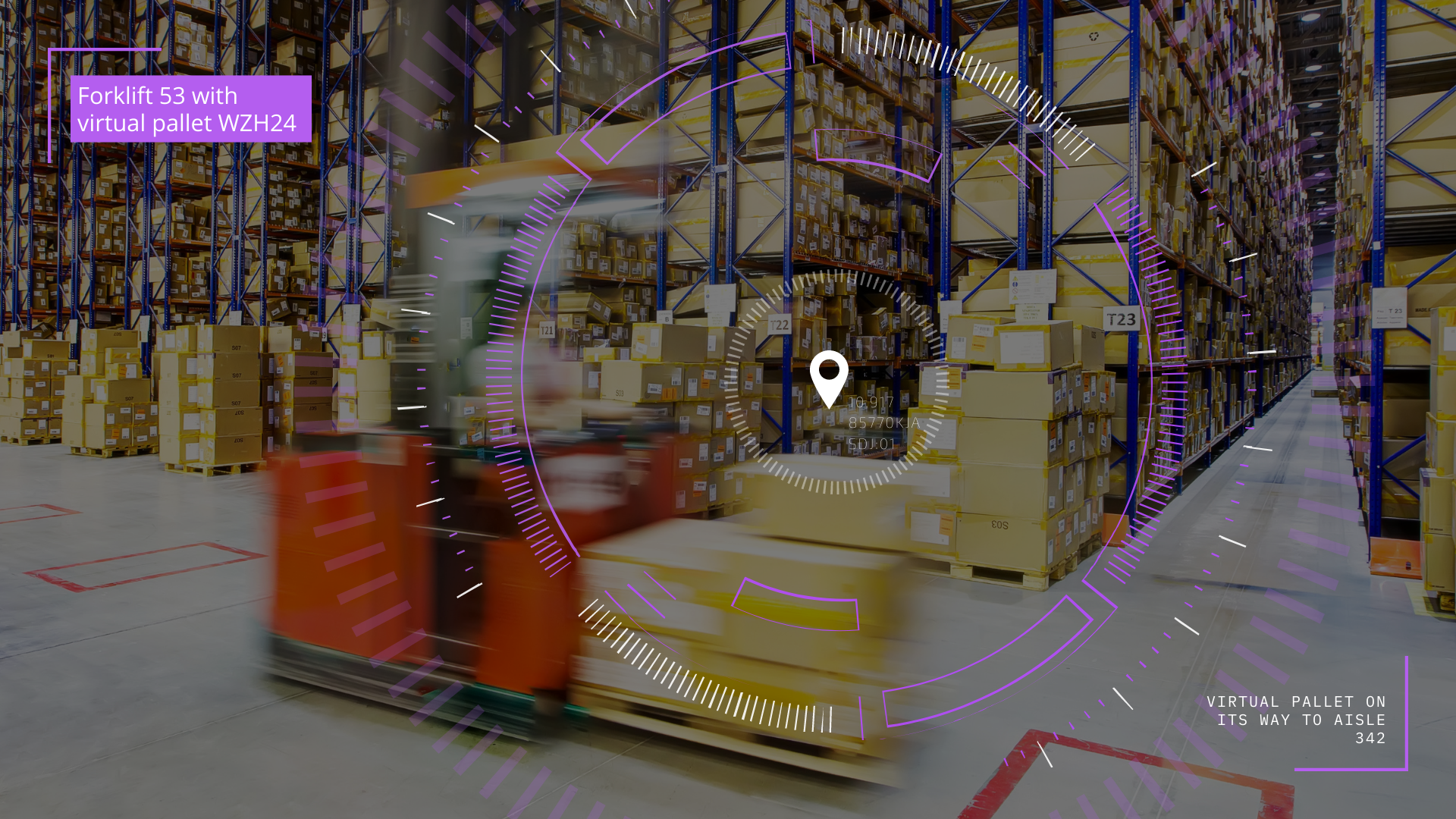
True values of using the
INTRANAV Smart Warehouse Solution
➜ End-to-end real-time visibility and digitization of the entire flow of goods and transport (assets, load carriers, vehicles) for intralogistics and the yard
➜ Automated warehouse control through warehouse trigger and process virtualization
➜ Transport optimization through digitization of the forklift fleet
➜ Scannerless goods transport
➜ Cost savings through Auto-Ident and integrated UWB & RFID technology
➜ Transport flow management through precise indoor / outdoor positioning
➜ Increase in goods flow order processing through driver navigation
➜ Route optimization through navigation and route utilization reports
➜ Virtualization of the actual storage location in the rack warehouse
➜ Safety management enables collision avoidance
➜ Automatic order pool processing from central systems (ERP, WMS, MES)
➜ A central system and process dashboard as RTLS control station
➜ Industrial interfaces and API for implementing RTLS data into your applications
➜ SAP-based instruction display for loading unmixed pallets and simultaneously automatic verification of unmixed pallet loading
➜ Goods bulk recording and booking in the SAP system with RFID
➜ Integrated multi-stack location engine with numerous setting options for filters and data preprocessing
Contact us!