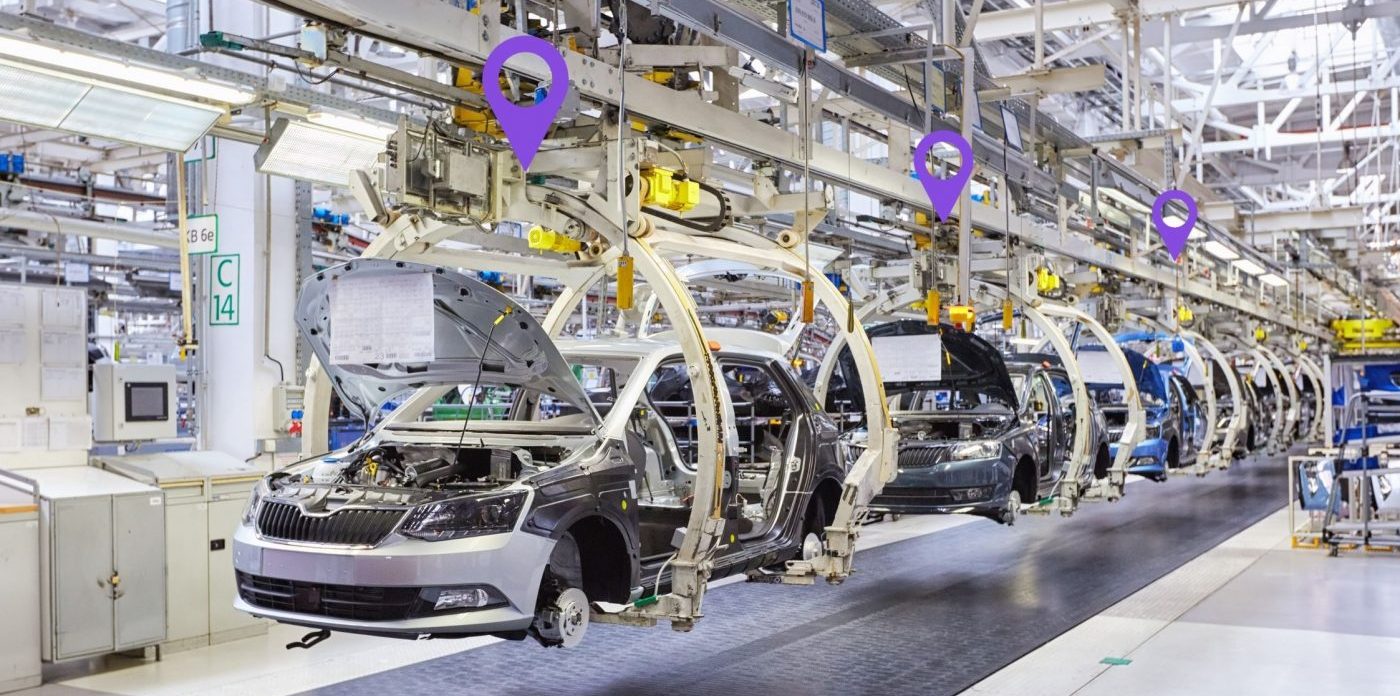
INTRANAV Production & Assembly Line Automation
SMART Factory
Enabling lean production with INTRANAV
INTRANAV provides integrated Track & Trace and networking of all assets, components, boxes and vehicles in the production hall through intelligent automation solutions to improve productivity, such as shortening product throughput times. In addition, you optimize product quality through constant, automatic quality control and process analyses. Contribute to error prevention with Real-Time Location Data, ensuring “just-in-time” and “just-in-sequence” of the entire production process. At the same time you increase the flexibility of the production equipment by linking it to several production systems. Thus you avoid waste, such as rework or multiple data entry or waiting for (superfluous) stocks.
Real-time location intelligence
for self controlling manufacturing processes
- Automatic sequence feedback
- Line Balancing / Production-Levelling
- „Just in Sequence” – Supply for the right sequence
- Add-on for worker information system (Paperless Production)
- Zone based control of automatic plant systems
-
By equipping the INTRANAV.RTLS IoT Suite with your production assets, you can track every production step of your production line in real time. This way you can see the entire production process as a digital twin via our IoT RTLS platform (INTRANAV.IO).
INTRANAV controls your production line already (partially) automated through individually defined, virtual clock zones (geofences). When the production piece is moved through the virtual zone, the production cycle (cycle sequence) is automatically booked as completed, so that the next cycle is informed about the status in real time and can begin with the next step. With the automatic cycle feedback you ensure quality standards and exclude that no step in the process is forgotten. This also saves time for the workers, as manual scanning is no longer necessary!
► Important: Posting too late or too early due to manual scanning processes can have critical consequences for the production line, such as excess or idle time, which in turn leads to inefficiencies in the entire supply chain process flow.
By linking to ERP (Enterprise Resource Planning) and EWM (Extended Warehouse Management) systems, you can provide information at higher levels, which triggers further information impulses.
-
INTRANAV helps you to keep your production output constant through granular cycle measurement. With INTRALYTICS ZONE Reports you analyze zone dwell times and can then evaluate whether manufacturing stations, i.e. work cycles, are correctly dimensioned or whether adjustments, so-called “smoothing”, are necessary.
► [ An example of the use of INTRANAV as an early warning system, from pre-assembly: ]
The pre-assembly lines are not (always) physically connected to the main production line, so that, among other things, congestion can sometimes occur at the line. This in turn leads to missing parts, whereupon the production process has to be interrupted again and may even lead to downtimes.
INTRANAV.IO acts as an early warning system!
It recognizes predictively, by measuring the real-time position data of the production parts, when changes in the production line occur and can issue alerts to initiate countermeasures through “events”, which enables the worker to react to the situation even before the production stops.► [ Further “Line Balancing” Cases with INTRANAV: ]
– Employee Tracking: How do employees move around the product/ or production line? Was work actually carried out at the intended location on the conveyor belt?
– Tool Tracking: Were the quality standards met with the appropriate tools during assembly?
– Load carrier tracking: Was the container placed at the intended location?
-
An essential safety aspect in the avoidance of errors in production is the plausibility check (batch testing/assembly test) of the corresponding assembly materials & components for the right cycle.
With INTRANAV, virtual zones (geofences) can be automated and recorded in real time if a semi-finished product, sub-assembly or component is not part of the leading product/assembly (e.g. car – correct tire).
A tire that does not belong to the intended car can be blocked for further production by If-Then Rules and real-time event location triggers. In addition, a warning message can be issued that the wrong part has been provided here, so that there are no downtimes on the conveyor/production line in the first place.
-
Production schedules & information about any manufacturing component, can be stored paperless production on INTRANAV.RTLS TAGs.
If the assembly piece is now moved from cycle to cycle, the necessary assembly information is given to each worker via tablet or screen. In addition, the necessary production information can also be provided depending on the level of training of the worker.
-
With INTRANAV, automated systems or production instruments can be automatically configured according to the cycle (production sequence).
Real-Time Location makes it possible – Through virtual zones (geofences) and/or system coupling to interfaces such as Profi-Bus (OPCOA) or programmable logic controllers (PLC), the system programming adapts to the possible assembly step.
► Here you save valuable time of your workers, because manual sequence system adjustments are not necessary. Furthermore, automatic identification is much less prone to errors!
INTRANAV Real-Time Location &
Sensor Data Monitoring Features
Production & Assembly Line Automation
-
Digital Twin of your
production facility -
Condition monitoring with
INTRANAV SMART Sensors -
Rules & Alerts
-
Hazard monitoring
-
AUTO-ID
-
2D/3D Zones and Events
-
INTRALYTICS
Produktionsanalysen -
Paperless Production
-
Coupling to PLC
control systems
INTRANAV Benefits
for assembly line automation
- Real-time location tracking as a prerequisite for intelligent lean material flow
- Optimization of the overall equipment effectiveness (OEE)
- Automatic (scannerless) production step booking (Auto-ID)
- Track and Trace reduces search times (boxes, palettes)
- For workers, precise tracking represents a special safety factor, especially in critical situations in confusing environments
- Improved plant utilization leads to cost optimization
- Fast reaction time to production changes
- Throughput times are improved, resulting in optimized cost-efficiency
- The entire production process becomes transparent, more flexible
- Reduction of unused capacities
- Immediate rework of defective products or product parts
- Avoidance of waste in production and procurement
- Constant production circulation
- Control and analysis of the production stages
- Status and position of the workpiece
- Coupling to ERP, EWM, OPCOA, SPS (and many more)
It’s that simple!
-
Activate the INTRANAV Plug & Play Solution
-
Attach INTRANAV.RTLS TAG (tracker) to box or vehicle
-
Real-time tracking & sensor data monitoring of your load carriers via the INTRANAV.IO platform
-
Scale INTRANAV Digital Twin Suite as desired per device
Finally process transparency with
INTRANAV.IO Suite
-
INTRANAV.IO
Learn more -
Digital Solutions
Learn more -
RTLS Applications
Learn more