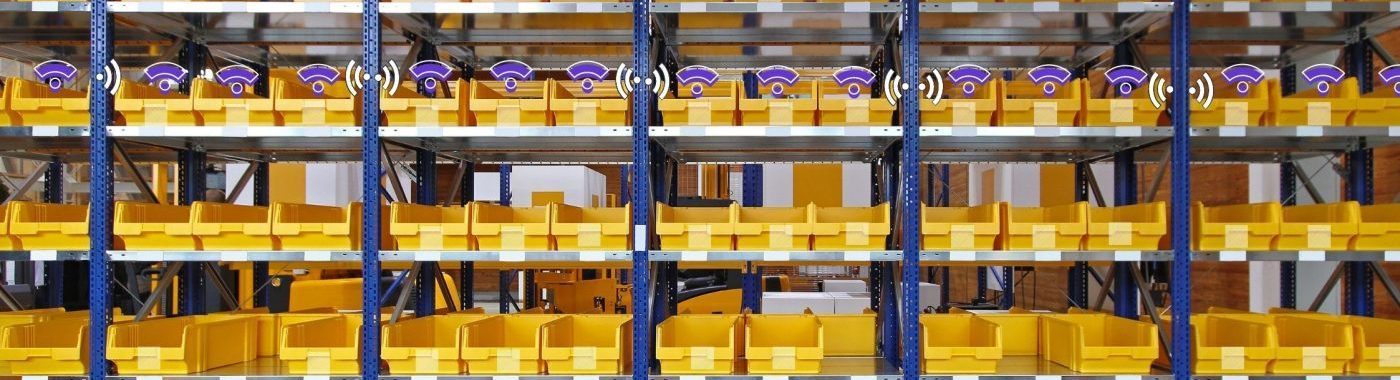
Intelligent Material Flow Control for Optimal Material Supply (eKanban)
Smart Factory
Kanban production control enables logistics companies to control the supply chain in a particularly cost-optimized way through the multi-level integration chain. One part of it is the provision of materials in production, with eKanban this is done automatically, so that a fast and steady flow is created by the pulling production. Risks and costs can be better calculated and minimized at the same time. By digitizing the material supply with INTRANAV and monitoring the entire production process, delays can be avoided and deviations in the process can be reacted to early. The combination of eKanban and Real-Time Location Production Tracking enables flexible deployment and adaptation of production workflows and a forward-looking determination of requirements.
eKanban Material Replenishment &
Real-Time Production Process Tracking
-
Automatic replenishment & material supply
(eKanban) - Automatic plausibility check of boxes & containers for the assembly line
- Process stability and simplification of variant production
- Just in Sequence – Provision for the right sequence
- Securing the linefeeding specifications
-
With INTRANAV you control and monitor, through the eKanban process, the automatic material replenishment in the entire production and intralogistics. With the pull-principle, the worker orders the immediate replenishment by pressing a button or scan trigger, so that the required production material is available again in time and the production line continues to run in circulation.
► [ INTRANAV controls your eKanban process ]
When equipped with BLE or RFID sensors on KLT containers, INTRANAV.IO, in connection with EWM / ERP systems, automatically registers the material requirement message of the worker. This is done by container removal or empty container provision in the eKanban rack. The empty container is automatically scanned via RFID gateways or the worker activates the push sensor, which is connected to the material management. The rack sensors continuously monitor the container location and report status changes (as “occupied” or “free”) directly to the INTRANAV.IO platform.
The IoT system thus ensures that the respective material supply status is updated in real time and initiated if necessary. The sensor ID is linked to the box of the respective material ID. INTRANAV thus ensures an automatic and reliable material replenishment process.► [ Wireless eKanban Solution & Predictive Material Replenishment ]
Wireless sensors ensure continued automatic material supply in production areas where the eKanban racks are regularly moved. Predictive material replenishment and monitoring is also possible by coupling additional sensors to roller conveyors. In connection with EWM / ERP systems, automatic ordering procedures can also be determined.► [ Monitoring of the production and replenishment process with Real-Time Location Data ]
For a fully intelligent material flow control, workers need real-time information about the positions of all assets and vehicles in the hall! With INTRANAV you can monitor live the entire replenishment process via the INTRANAV.IO Digital Twin platform (provided all assets, boxes, containers and transport vehicles are equipped with TAGs). On the tablet or desktop, every worker can see where the transport feeder is or where the material order is located. The real-time location and status information is the basis for better decisions. Workers can better organize themselves and plan workloads more efficiently! -
A major source of error in material replenishment on the assembly line and in production is often due to the incorrect provision of boxes and containers and parking them in the wrong place, which leads to undesirable consequences such as wasted time and costs. Cycle interruptions or even belt standstill are the result, which is caused by wrong parts or missing parts.
► With INTRANAV you avoid high reworking requirements due to incorrectly picked parts or incorrect assembly. Continuous real-time tracking of the material boxes and containers and the use of virtual zones (geofences), which you can create according to your needs via the INTRANAV.IO RTLS platform, ensures a live plausibility check during material supply on the line. If a semi-finished product, sub-assembly or component is placed in the wrong place, this is recorded in real-time and reported back to the system.
► A container that does not belong to the intended cycle, i.e. is parked in the wrong place, can be blocked for further production by If-Then Rules and real-time event location triggers. The carrier can also use the IoT platform to call up where the box must be placed correctly. In addition, a warning message can be issued that the wrong component box has been provided here, so that there are no downtimes on the conveyor/production line in the first place.
► An essential safety aspect in avoiding errors in production is the plausibility check (batch check/assembly check) of the corresponding assembly materials & components for the correct cycle.
-
The mastery of variant production requires a holistic product-process segmentation in the production environment as well as in intralogistics. INTRANAV provides clear location and product status information about the suitability of the correct sequence through real-time tracking of the component pallets and boxes and thus helps to prevent the risk of mix-ups during picking or to avoid reworking in order to completely rule out consequential damages that can result from incorrect assembly, such as complaints due to incorrect installation.
► With the equipment of INTRANAV Ultra-Wideband TAGs on boxes and containers, workers can always check whether the container in front of them is the right one. The Pick-by-Light feature of INTRANAV.RTLS TAGs also ensures fast and safe manual retrieval when several variant pallets are available for processing at the assembly line.
-
An essential safety aspect in the avoidance of errors in production is the plausibility check (batch testing/assembly test) of the corresponding assembly materials & components for the right cycle.
► With INTRANAV, virtual zones (geofences) can be used to automate and record in real time if a semi-finished product, sub-assembly or component is not part of the leading product/assembly (e.g. car – correct tire).
A tire that does not belong to the intended car can be blocked for further production by If-Then Rules and real-time event location triggers. In addition, a warning message can be issued that the wrong part has been provided here, so that there are no downtimes on the conveyor/production line in the first place. -
Linefeeding refers to the provision of the exact material stock required (Six-R rule: right material, at the right time, at the right place, in the right quantity, in the right quality and at the right cost) on the production line, in order to avoid flat goods or overproduction and to be able to fully utilize space resources on the line.
► Securing the line feeding:
With INTRANAV you can monitor the entire material supply process in real time. Should an unforeseen amount of material be provided on the line, the INTRANAV Indoor Live Map allows you to see exactly where the excess or surplus material is located and you can have it removed or delivered again immediately.
As soon as the material boxes (which are equipped with INTRANAV UWB TAGs) move into the virtual zone (geofence) on the conveyor, the INTRANAV system automatically recognizes in real-time, through coupling to ERP (Enterprise Resource Planning) and EWM systems (Extended Warehouse Management), if a surplus or too few boxes have been delivered.
Live alerts provide immediate notification to the worker to take countermeasures such as replenishment or withdrawal.► With INTRANAV you ensure a dynamic and consumption-oriented material supply in terms of the pull system (Lean Management).
INTRANAV Real-Time Location &
Sensor Data Monitoring Features
eKanban Material Replenishment & Process Tracking
-
Digital Twin of the load carrier
-
Condition monitoring with
INTRANAV SMART Sensoren -
Real-time alerts
-
Hazard monitoring
-
AUTO-ID & Auto-Blocking
-
2D/3D Zones and Events
-
Paperless Production
-
Multi-Technology Stack
(IoT Plattform) -
Live & Retrograd Analysen
(Zonenverweilzeit ..)
INTRANAV eKanban Material Replenishment & Process Tracking Benefits
- Real-time demand alerts
- Flexible adaptation to changes in material requirements
- Automatic refill
- Process reliability through foresighted determination of requirements
- Overview of the entire internal material flow
- Reduced material replenishment times and excess capacities
- Protection against overpopulation or idling
- Permanent overview of the stock of fast-moving items
- Intelligent protection against overpopulation or idle
- Process reliability through foresighted determination of requirements
- Intelligent protection against overpopulation or idle
- Flexible adaptation to changes in material requirements
- Minimizes unnecessary excess material on the belt
- Reduced safety stocks thanks to demand-oriented material provision
- Additional process reliability through automatic replenishment control
- Flexibility in using the eKanban rack
- Fully integrated recording of material consumption in real time
It’s that simple!
-
Activate the INTRANAV Plug & Play Solution
-
Attach INTRANAV.RTLS TAG (Tracker) to KLT Box
-
Real-time tracking & sensor data monitoring of your load carriers via the INTRANAV.IO platform
-
Scale INTRANAV Digital Twin Suite as desired per device