27.01.2021
Digital Twin platform controls automatic sequence feedback and
eliminates manual scan steps
In the individual manufacture of large construction machines, such as that of our customer, almost all production steps have to be carried out manually, as well as accounted for after completion of assembly and moved from one cycle to the next. With a huge selection of model variants to be produced, the question arises as to how this high variance of production parts can be monitored and all quality standards mastered. This concerns quality assurance as well as scanner-based booking and cycle control of individual production steps on the assembly line. The production plant of our customer consists of several pre-assembly and main assembly lines.
For an international agricultural and
construction machinery manufacturer
Our customer is a German, internationally operating manufacturer of agricultural and construction machinery. In one of the most modern production facilities in Europe, all-wheel steered wheel loaders, teleloaders and telescopic loaders for the construction industry, agriculture, gardening and landscaping are manufactured in individual production.
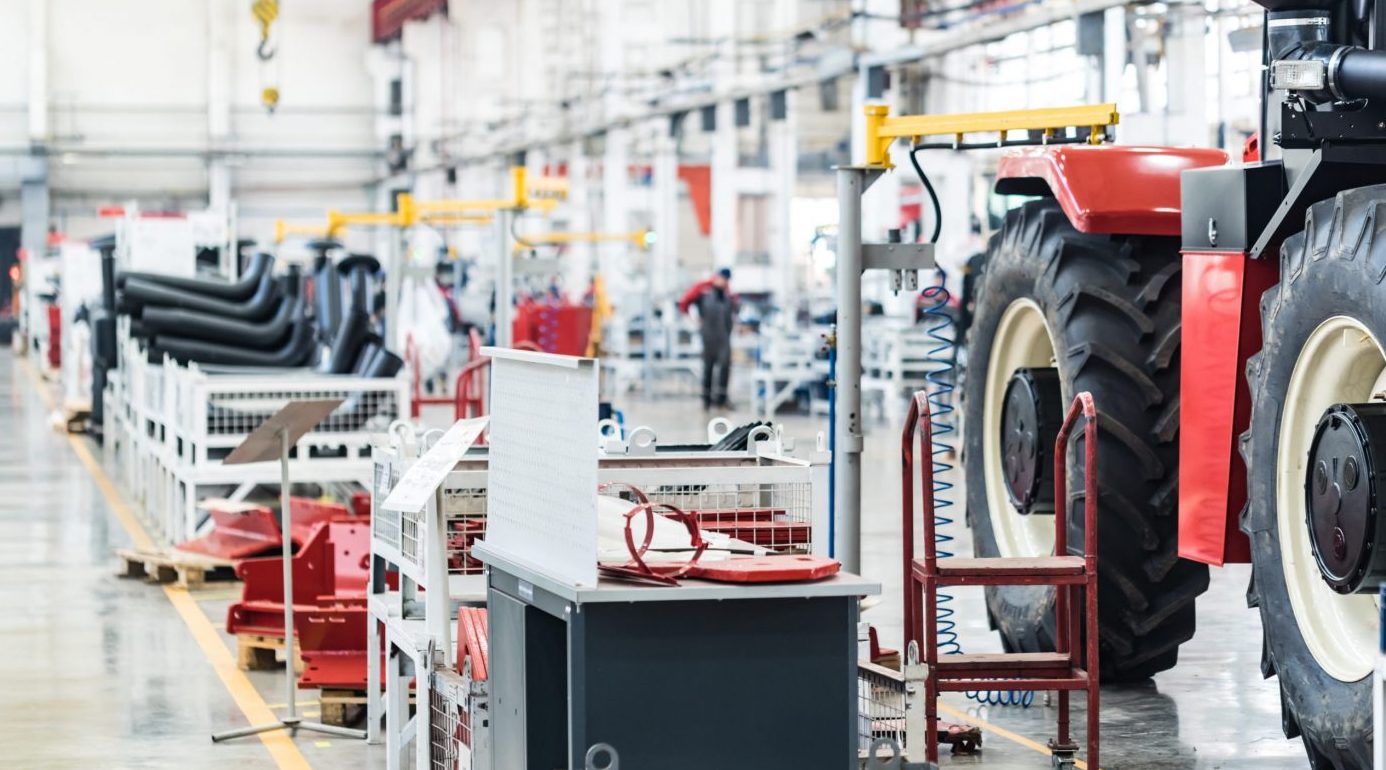
Requirements of our customer
-
1
Assembly Line Real-Time Location Tracking
Precise (±) 10 cm real-time localization information where all assembly steps are located as well as about the boxes, containers, load carriers and racks located on the assembly line, which are manually pushed from cycle to cycle.
-
2
Automatic sequence feedback
Partial automation of status information by automatic clock update so that following clock can start.
-
3
Eliminate scanning and
posting stepsManual scanning processes, such as material, takt-related transaction posting or plausibility checks, are replaced by auto-ident postings (auto-ID).
-
4
Sequence-related
automation triggersProduction-related information can be called up virtually; in addition, setup processes start automatically by means of programmable logic control (PLC).
Solution from INTRANAV
We enabled our customer with the intelligent production control a smart solution, which serves the company as a basis for all further Industry 4.0 – digitization steps. The INTRANAV Real-Time Location System, based on ultra-wideband technology, is to form the foundation for further automation solutions in production and logistics. The production line was equipped with the INTRANAV.RTLS system, which provides workers with accurate real-time information about the production status and location of boxes, containers, load carriers, and racks located on the assembly line. The information is digitized and visually displayed as a Digital Twin via the INTRANAV.IO RTLS platform. Workers can thus see in real-time: which material is used in which cycle, where material replenishment may be required, whether the production steps are running synchronously or whether there are time deviations, or to what extent delays are to be expected.
Individually defined virtual cycle zones (geofences) mean that the production cycle is automatically recorded as completed when the production piece and the load carrier are moved through the virtual zone. This means that the next cycle is informed in real time about the status and can start with the next step. Automatic cycle feedback ensures quality standards and eliminates errors, so that no process step is omitted. This also saves workers time, as manual scanning is no longer necessary.
With INTRANAV, virtual zones (geofences), which are individually defined by the customer for each cycle via the INTRANAV.IO platform, replace manual scanning and booking processes with auto-bookings (auto-ID). The manual process of the worker by scanning the barcode of the machine card in order to book operations or material is now automated for each cycle.
Further triggers were set via the geofences to call up production order-related information (options), as well as to start additional setup processes for fixtures, e.g. by means of a programmable logic controller (PLC).
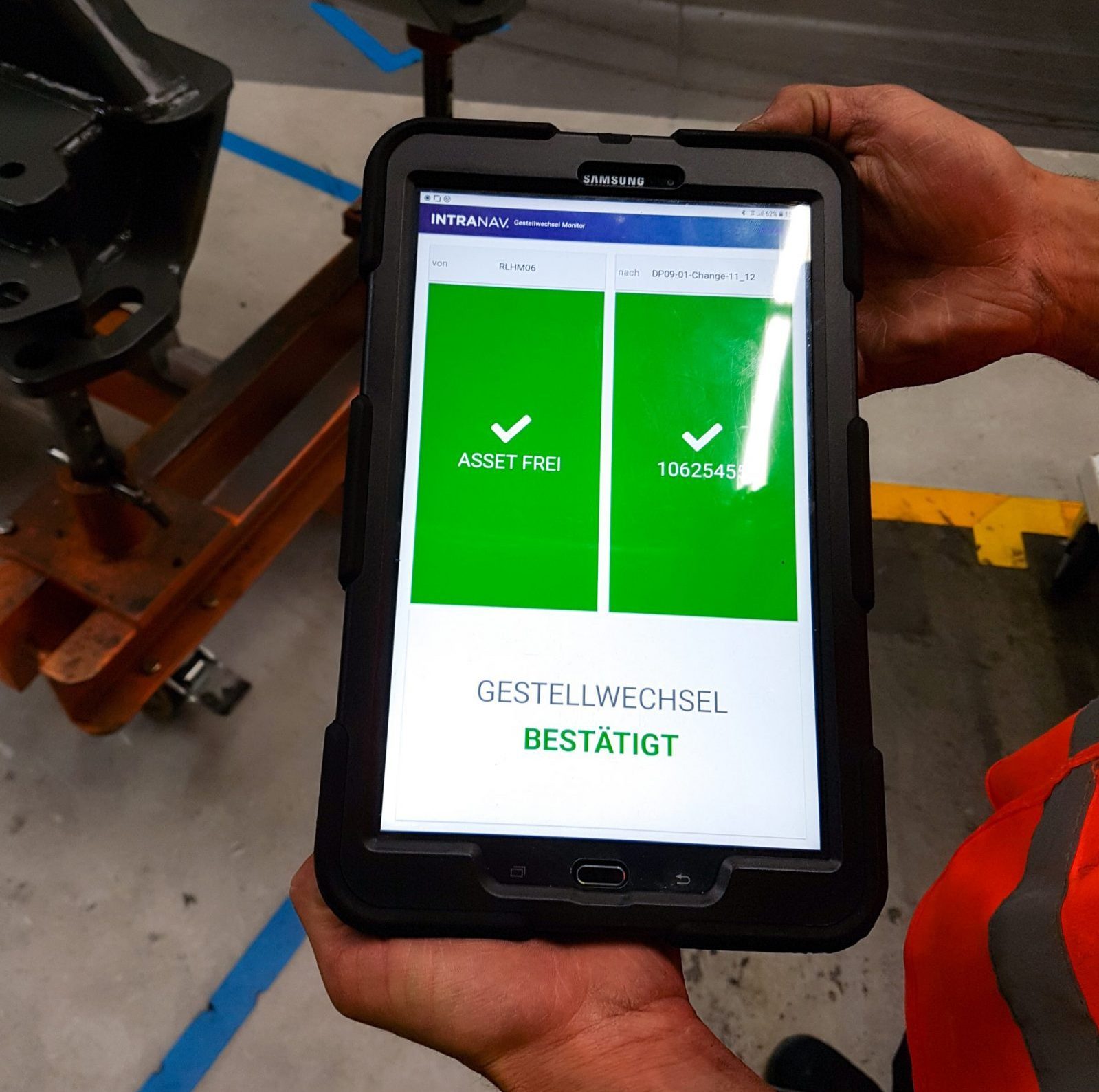
Result
The basis for plausibility of pre-assembly and main assembly synchronization of cycles, cycle-related picking (large components), generation of driving orders, cycle-related option display are implemented by INTRANAV. The process transparency gained by the integrative, independent IoT RTLS platform ensures compliance with quality assurance and individual manufacturing steps.
Non-value-adding activities, manual scanning processes that are now replaced by automatic cycle feedback, are reduced. The time that is now “freed up” can either be used to accelerate or increase the output quantity or to implement quality assurance measures. The elimination of sequencing errors leads to the avoidance of rework, as well as empty cycles/idle times and the avoidance of excess material on the delivery area. The availability of limited special load carriers is increased, as all workers are informed about the real-time location status of the respective assets.
INTRANAV Benefits with the intelligent production control system
- Real-time assembly line overview and process transparency of the entire variant production, digitally retrievable as Digital Twin
- Automatic clock feedback via virtual zones
- Replacing manual scanning operations with Auto-ID bookings
- Cycle-related automation triggers ensure automated retrieval of worker information, e.g. checklists
- Coupling to PLC enables triggering of additional clock-specific production processes
- The RTLS is very cost effective and tracks accurately up to (±) 10 cm.
- Fast project implementation & integration of the turnkey RTLS solution
- INTRANAV.IO offers a modern and attractive user interface that works optimally on the desktop screen as well as on the smartphone/tablet.
- Various innovative interfaces enable the connection to all common ERP, EWM and CRM systems and databases as well as to Power BI, SQL Server and some others. With data coupling, further processing and use for optimizing logistics and supply chain processes as well as the entire information flow is possible.
- With the OPEN IO Device interface, the INTRANAV can acquire position and sensor data from multi-technologies such as UWB, GPS, DGPS, RFID, BLE, xMesh and LiDAR.
- It also meets the highest data security standards through end-to-end security and can be rolled out on-premise and in the cloud.
INTRANAV offers a highly flexible and cost-effective enterprise solution, ideal for automotive, aerospace, logistics or healthcare. Further fields of application are for example warehouse automation, collision avoidance, yard management, tool, equipment and small load carrier tracking, as well as supply chain monitoring or health safety environment.
Our INTRANAV Production Solution is also of interest to you, contact us to discuss optimization possibilities for your manufacturing and logistics workflows today!