18.01.2023
How BMW Group’s Design Division Uses Real-Time Location Technology and Software for Intelligent Inventory Management
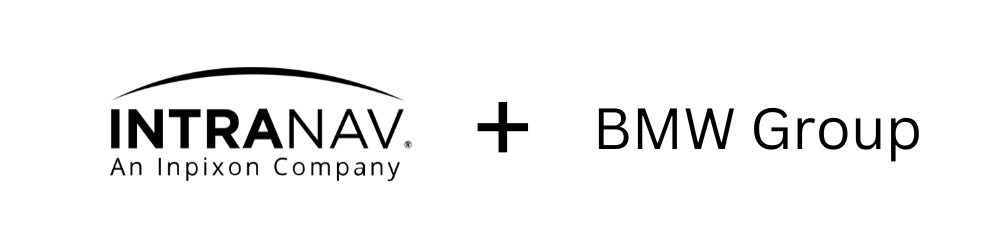
The Company
German premium car manufacturer of luxury vehicles and motorcycles, Bayerische Motoren Werke AG, commonly referred to as BMW, has a dedicated team to deploy, manage, and store design models of BMW Group vehicles. This team requires a simple and efficient inventory management and retrieval system for multiple models of BMW Group vehicles across numerous warehouse locations. As their previous inventory management system became outdated, they searched for an innovative approach to fulfill their growing needs and streamline their process.
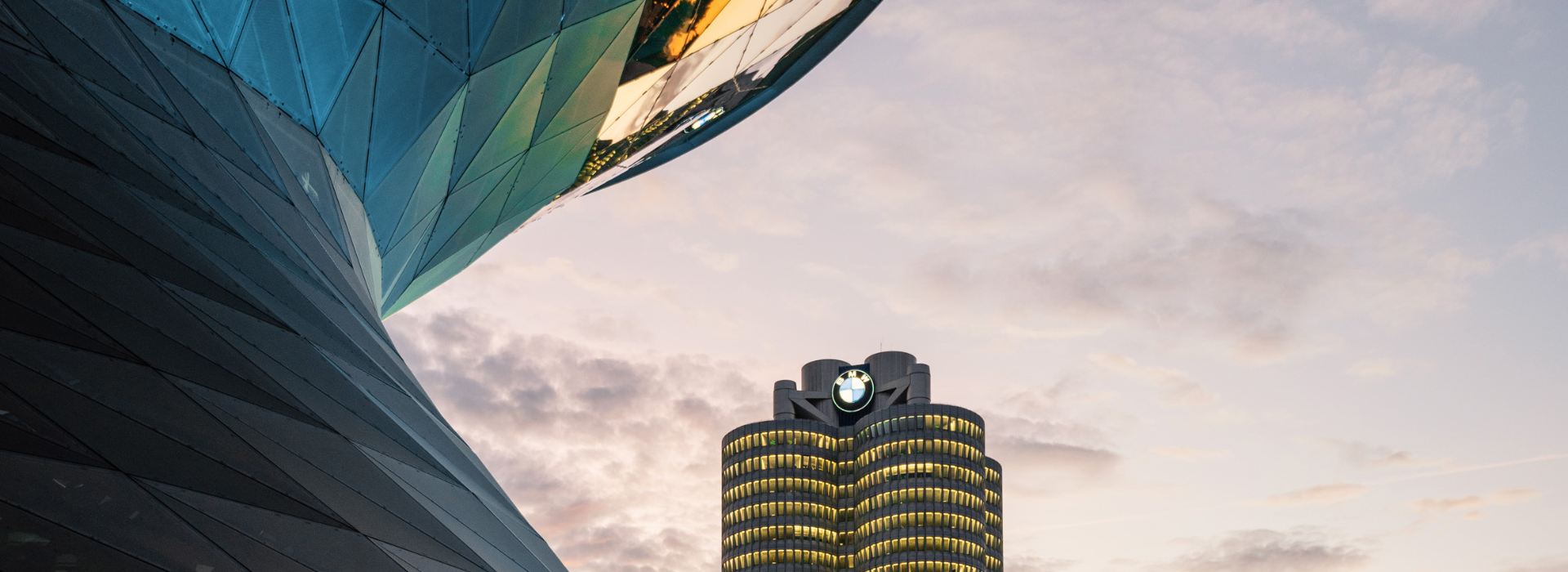
The Challenge
Prior to the implementation of its new inventory management solution, BMW Group faced many challenges.
First, their legacy software, a check-in & check-out inventory management system, was about to expire. This meant that they would no longer receive support from the vendor for the maintenance of their solution and that there would be no further updates or new features.
Second, search times for BMW Group vehicle models were often long and resource-intensive with their old solution. Once a model was no longer in its checked-in storage location, or check-out was missed, the logistics team started a manual search – sometimes across several storage facilities. There was also a lack of information on return times for the off-site lending of models, such as for trade shows. In addition, their previous inventory management system was based on barcode technology, which the team wanted to move away from due to the high degree of manual handling required.
On top of these issues, BMW Group needed to find a hardware system that would fit with the company-wide radio frequencies management policy. Their new solution had to prove that operations would not impact the functionality of their existing radio-based deployments (such as Wi-Fi).
As a result, BMW Group was looking for a one-stop solution that could automatically capture inventory, track the location of vehicle models in real-time, and also help their team manage the inventory of vehicle models with modern features such as reminders, alerts, and more.
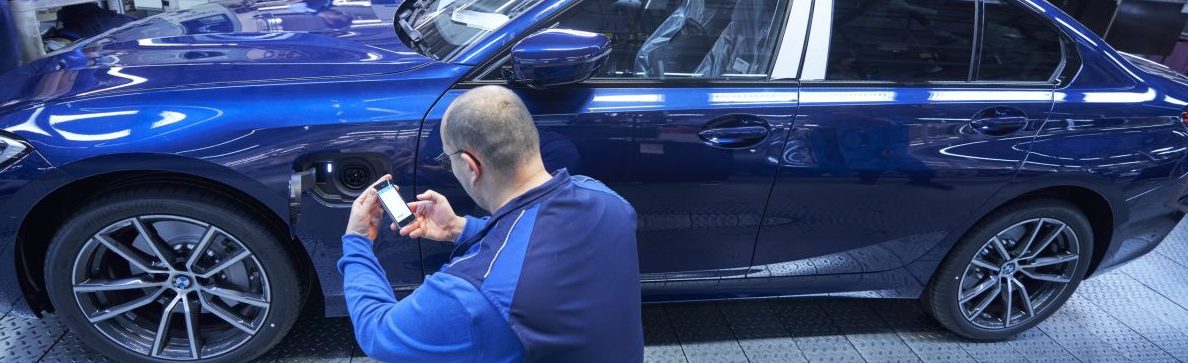
Customer Requirements
-
1
Reduce Search Times
Know where their vehicles are at all times and have a process in place to track their movement.
-
2
Inventory Management
Enable intelligent inventory search and management, filtering, and documentation.
-
3
Automatic Tracking
The real-time movement and location of each model is automatically tracked without the need for scanning during storage and retrieval.
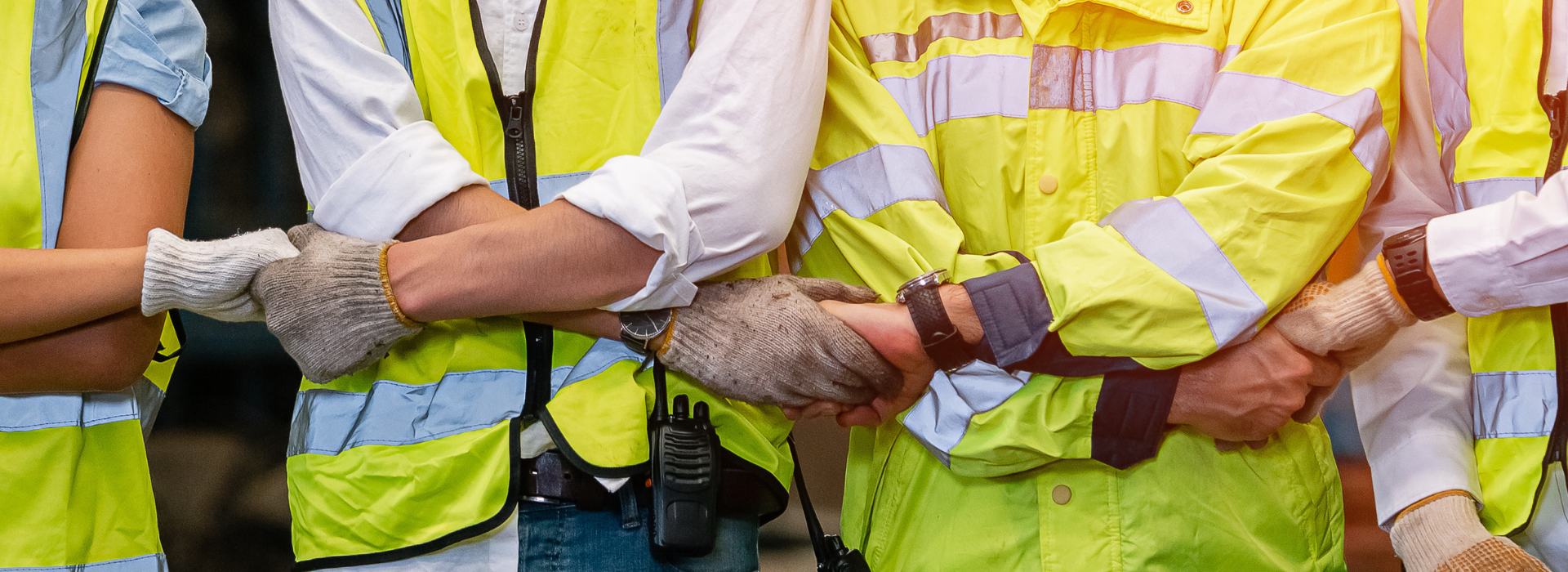
The Journey
In their search for specific tracking solutions, the logistics team came across Bluetooth beacons & sensor hardware provider ELA Innovation and, through them, connected with our technology partner, Wirepas, who specializes in wireless mesh connectivity technology for enterprise IoT systems, enabling fully battery-operated coverage and low total cost of (hardware) ownership. Through Wirepas, BMW Group was then introduced to INTRANAV, an Inpixon company, as BMW Group needed a software platform that was capable of mapping its inventory management use case.
-
Integrations
-
Inpixon
Real-time location and inventory management via advanced IoT platform. -
Wirepas
Battery-powered mesh connectivity technology. -
ELA-Innovation
Bluetooth Low Energy (BLE) hardware tags.
Integrations
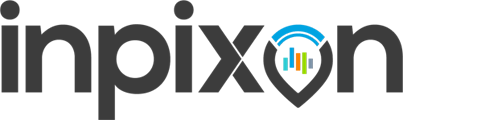
Inpixon
Real-time location and inventory management via advanced IoT platform.
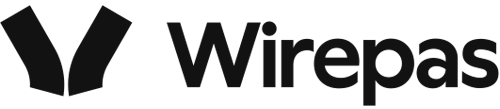
Wirepas
Battery-powered mesh connectivity technology.
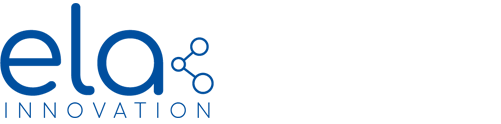
ELA-Innovation
Bluetooth Low Energy (BLE) hardware tags.
The Solution in the Design Division of BMW Group
The integrative solution from INTRANAV, an Inpixon company, and its technology partners Wirepas and ELA Innovation was exactly what BMW Group was looking for: inventory management software and localization in one system. We implemented our industry-leading software solution, which is easy to install, as well as comparatively low-cost, and battery-powered RTLS hardware. The tracking technology used, combined with device connectivity, enables a seamless inventory tracking approach across multiple warehouse locations.
1. Creating Real-Time Transparency Around the Locations of Their Entire Inventory, Leading to a Reduction in Search Time
Adding new vehicle models to the system only requires entering details (vehicle model name, responsible personnel, as well as the tag ID, etc.) via data entry into the INTRANAV Inventory Manager. In this step, the tag is also merged with the vehicle model and the INTRANAV.IO platform. Thanks to this updated workflow, the INTRANAV Inventory Manager makes the daily process of searching for vehicles more efficient and saves time. Previously, if a vehicle had not been scanned, it would need to be searched for at multiple locations, which can be very time-consuming.
With the INTRANAV Inventory Manager, once everything is initially entered into the system accurately, there is no need for any manual searching or other scanning. Vehicles can be moved freely across multiple locations and can be found immediately using the platform.
2. Offering a Search and Filter Function that Simplifies Inventory Management
With the help of search and filter functions, entire vehicle groups can be identified and moved into the system as required. For example, as soon as several vehicle groups are lent out, this can be quickly recorded in bulk information instead of having to create a custom, manual reminder. This makes inventory management in the design warehouse less error-prone, resulting in greater time efficiency for staff.
3. Reducing Errors Through Alerts and Proactive Messaging
Through our geofence-based messaging system, the appropriate department personnel are alerted when a vehicle leaves the BMW Group premises. Their new system also prompts the user to note where the vehicle is being taken in this case, such as a trade show, which helps ensure the vehicle’s whereabouts are tracked properly and in a timely fashion.
4. Storing Inventory History and Other Key Information on Each Vehicle
The INTRANAV Inventory Manager enables real-time inventory management of all prototype models, including the retrievability of the respective internal identifier of each individual model, which also provides further information about the model’s condition, type, and special features. Its inventory history is used for research purposes when it is necessary to check whether a vehicle model has already passed through various departments. The uncomplicated access to this throughput information, as well as to supplementary files, such as pictures or an operating manual, simplifies the daily handling of vehicles for their team, making it faster and more accurate overall.
5. Being Compatible with Existing Radio Frequencies & Technologies
The on-site frequency manager at BMW Group ensures that frequencies do not interfere with each other when new systems are introduced. BMW Group has verified by conducting its own measurements in the lab that the system has no further impact on the functionality of other systems – especially Wi-Fi. Thus, official operating permission has been given by BMW Group for this technology.
The INTRANAV Inventory Manager
Inpixon’s INTRANAV Inventory Manager is a complete solution for managing enterprise inventory, such as equipment, prototype models, rotating equipment, tools, products, boxes, and valuable loaners.
The advantage of the software is that RTLS (Real-TIme Location System) based on technologies like BLE, UWB, Chirp (CSS), or GPS, as well connectivity technologies like Wirepas, can be connected to track inventory in real-time. This enables real-time inventory management, allowing the system to improve visibility, efficiency, and productivity in the facility.
The inventory management system has an automated inventory notification feature that can send notifications to staff to check on specific inventory items.
Here is a brief overview of some of the features:
Add Inventory
INTRANAV Inventory Manager has an input screen that allows the user to add inventory objects to the system. The user can also add custom filters and fields to meet the internal inventory requirements.
Inventory Search
INTRANAV Inventory Manager has an advanced and simple search form. This can be customized to the specific needs and requirements of the customer. It offers the possibility to search for specific identification numbers, inventory types, tracker numbers, item group types, and much more.
The user can get a comprehensive overview of the stored and managed inventory. Important parameters such as disposal information or file attachments can be quickly retrieved.
Inventory List – Detail Selection
Searches can be performed via the inventory list or the search function. Here, the detailed selection from the inventory list is displayed. Next to the object name, the map shows where the inventory object is located.
The Result of Optimization in the Design Division of the BMW Group
BMW Group achieved many key outcomes by implementing Inpixon’s INTRANAV inventory management system, including:
- Greater efficiency and reduced search times for employees utilizing the system. This led to notable time and costs savings for the company.
- A fast, smooth and successful installation process of the complete solution. The Wirepas-operated ELA anchors were installed within two days with no disruptions to their current operations.
- The complete shutdown of their legacy system. They are currently powering down their old process, citing that there was no comparison between their previous method and Inpixon’s INTRANAV IoT software solution and the wireless mesh technology from Wirepas.
- Daily time savings due to fewer inventory management errors. Since fewer vehicles are lost, personnel can be deployed for value-added work.
- Greater cost savings, efficiency and simplicity in searching and locating individual vehicles. Employees no longer need to carry a device with them at all times – they can use the INTRANAV.IO mobile app to search for vehicles on their phones. This leads to a much faster process, making it easier for employees to be productive. It also leads to significant cost savings for BMW Group, because they no longer need to maintain and replace scanning/reader devices for their employees.
- A fully functional inventory management tracking solution that operates on a frequency that doesn’t interfere with other operations. This ensures the smooth operations of all systems, new and existing, in their facilities.
- Easy commissioning of additional models as the system autonomously detects newly tagged assets.
Inpixon offers a highly flexible and cost-effective enterprise solution, ideally suited for automotive, aerospace, logistics or production.