27.05.2021
Increased picking productivity and clarity through automated block storage with the digitized electric pallet truck and forklift fleet
In block storage, all goods are stacked on top of each other in boxes, pallets or wire mesh boxes in blocks on the floor. In floor storage, single-variety items are usually stored in a block to ensure quick and easy access. The LIFO (Last in, First out) storage strategy is used to keep the logistical effort as low as possible. The block storage system is particularly suitable for medium to very high goods throughput.
Material handling challenges in block storage:
● High access times, due to narrow aisles, the goods are difficult to reach.
● High search times, since this storage can be changed variably at any time and there is no unique designation as in the shelf warehouse, for example.
● Long control process during picking: Longer control times are required to be sure that the correct goods have been picked.
● Time-consuming, manual posting processes: Material postings are made by manually scanning the inventory card
● Idle time of the transport fleet, due to uncoordinated order processing.
● Detours that occur due to search times
● Scanning processes are carried out incorrectly
● And more
Increase in overall productivity through
virtual material handling in block storage
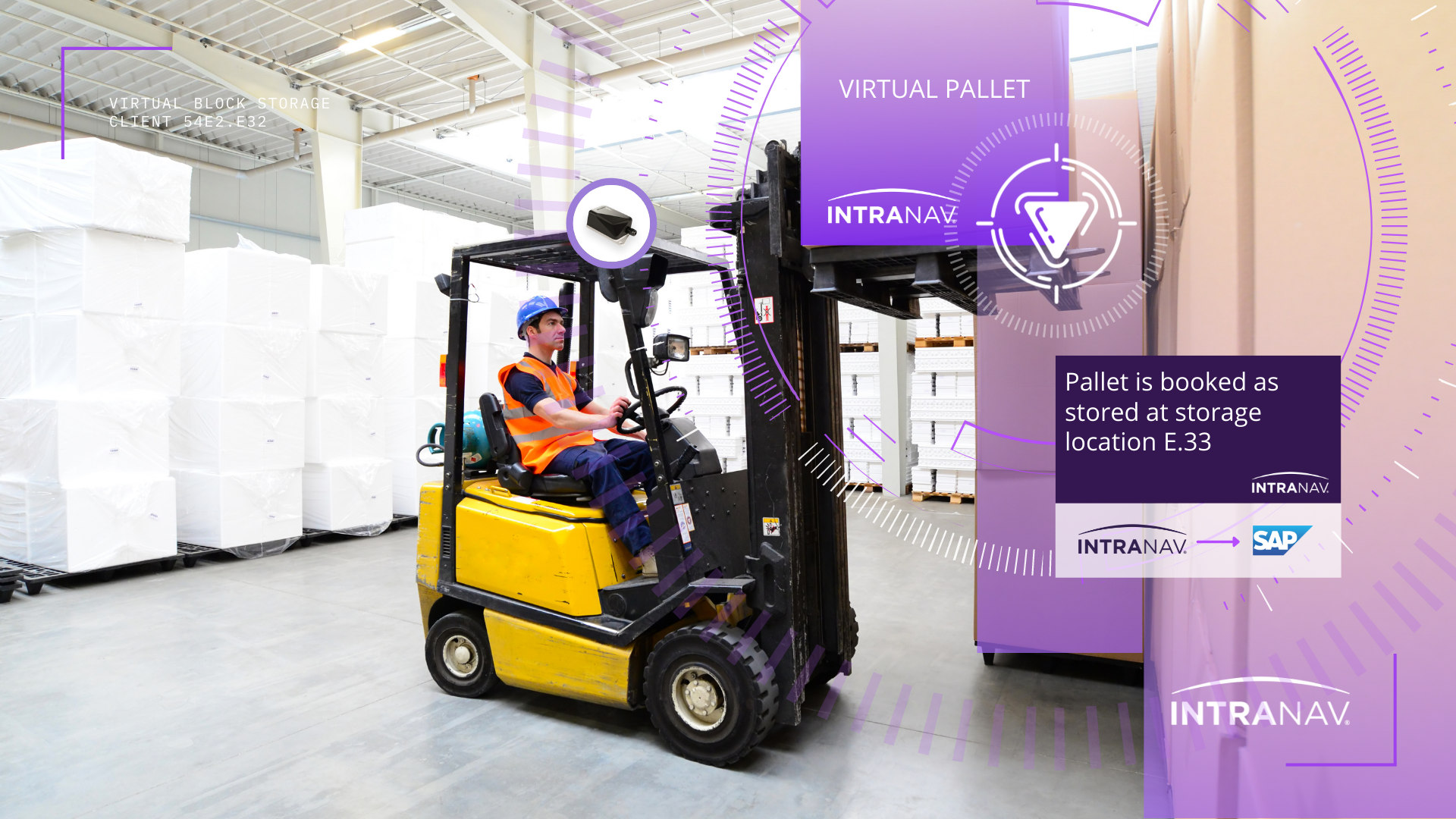
1. Real-time overview and transparency of the entire stocks in the block storage reduces search times: The INTRANAV.APP “Virtual Storage” virtualizes and visualizes the entire warehouse inventory based on the last storage location (store point) as a Digital Twin.
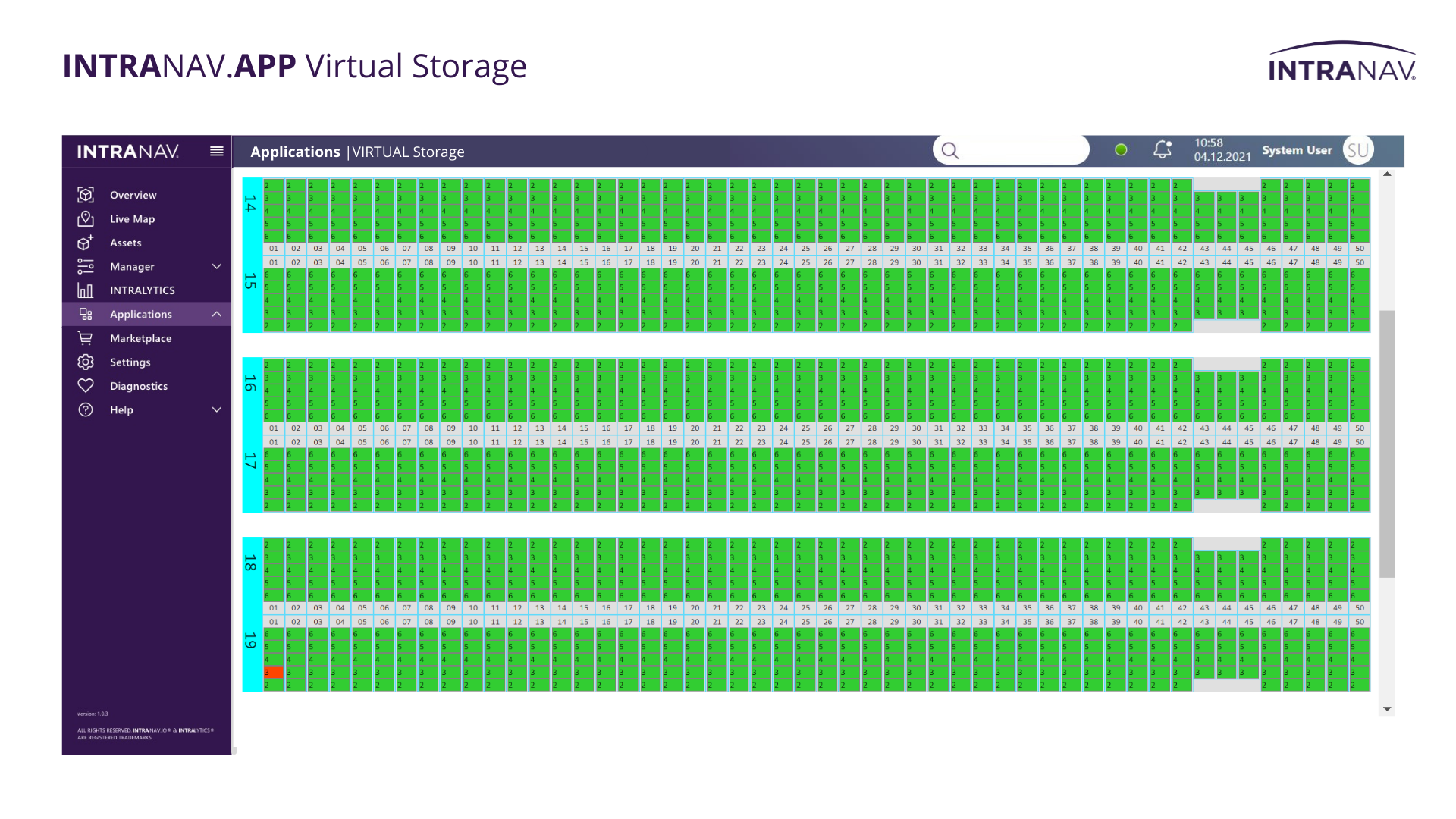
2. Automatic entry and exit of goods (AutoID) through Storepoint technology accelerates productivity: By picking up the goods with the forklift fork (equipped with RFID and UWB sensors), the first order matching takes place. The pallet is tracked from the first touchpoint (order matching with the fork) to the final putaway. The system understands the putaway on the shelf as a virtual endpoint until the next retrieval and automatically posts it in your warehouse management system accordingly. The process is carried out solely by the sensors on the fork; equipping the goods/pallets with RTLS hardware is no longer necessary!
3. Software-based picking process ensures clarity and reduces manual inspection times: In the stacker cockpit, the INTRANAV.APP “Transport Driver” displays which pallet has been picked and is on the fork, including associated information such as a number of packages, unmixed pallet or brand. Manual control times are thus significantly reduced. In addition, the system lists which job is currently being executed and how many transport jobs are still open.
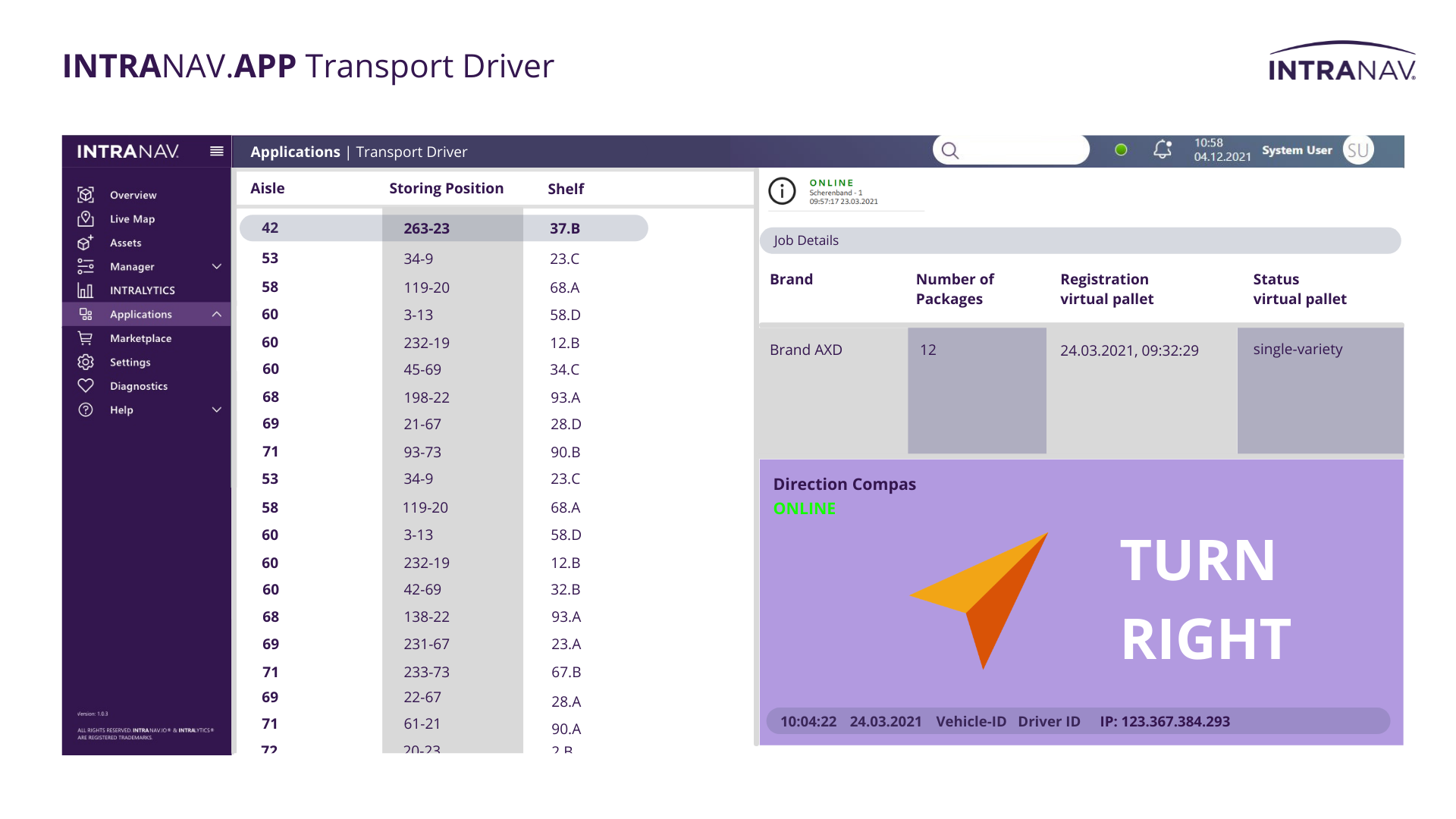
4. Improved access times: Collision Avoidance allows driving at increased speed: In block storage, stacking goods high often creates narrow aisles that can only be driven through with electric pallet trucks. Integrated safety sensors on the forks ensure that these can now also be driven through at higher speeds. In the event of a risk of collision, the speed of the vehicle is reduced significantly and in good time.
5. Scannerless goods transport for all other zones in the warehouse: Regardless of how many zones and buffers the goods have to pass through in the warehouse, INTRANAV automatically records and posts the last status of the goods in all areas in the warehouse.
6. Real-time transport orchestration reduces transport idle time: The INTRANAV.APP “Transport Pool” ensures the fast collection and allocation of all transport jobs to the vehicle fleet. Here, all transport jobs are collected from the SAP system and distributed to manned vehicles or Automated Guided Vehicles. The current location status of the respective vehicle is taken into account for the most efficient routes and the order quantity already allocated to the respective vehicle.
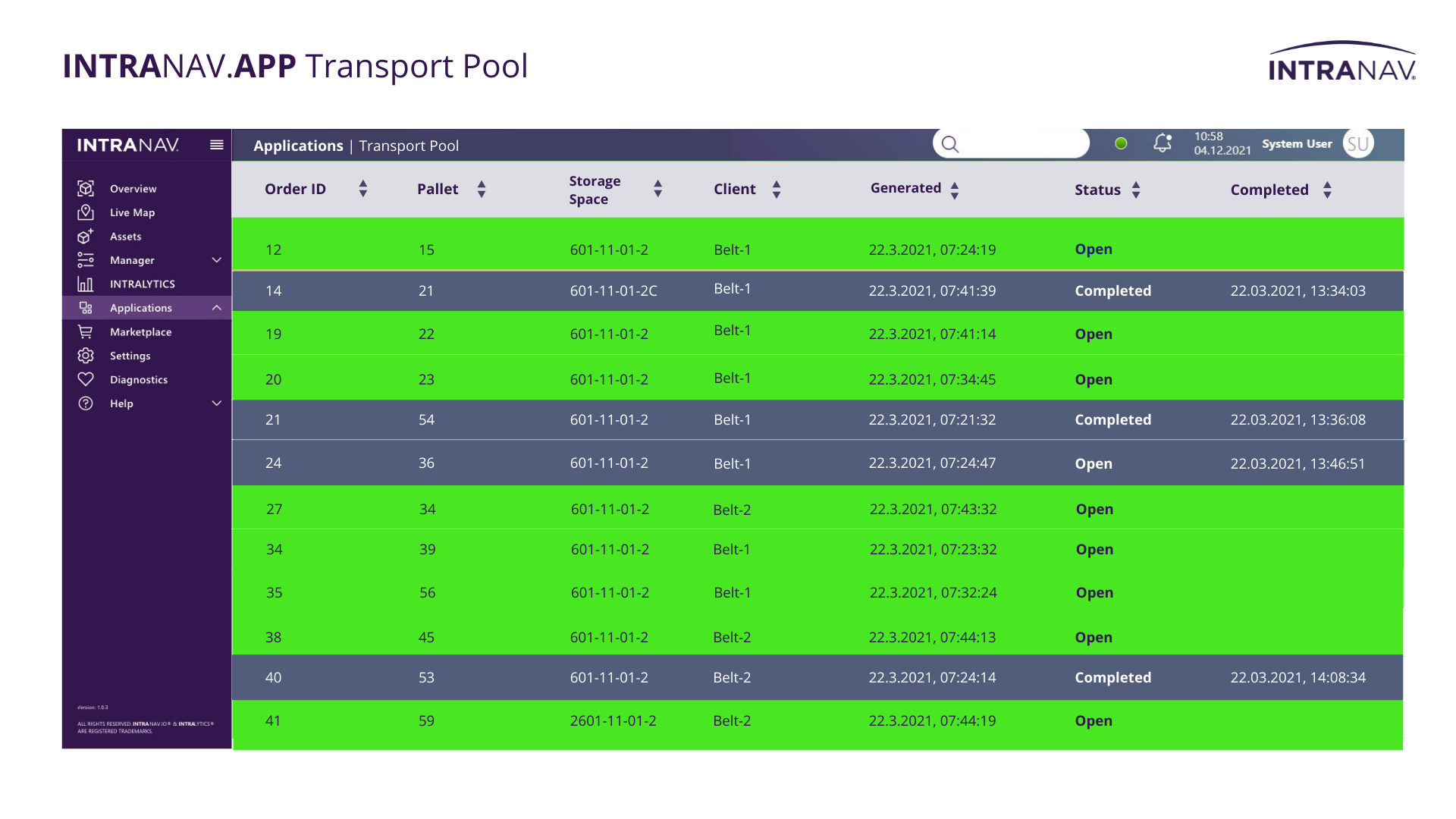
7. Warehouse event triggers replace manual handling processes: Through event triggers, each process is merged with the next by automatically triggering subsequent steps such as the creation of delivery bills, pickup order from the freight forwarder, printing of the shipping label, invoicing, customer notification of shipping notification, and much more, up to checking whether the goods are delivered to the correct door.
8. End-to-end tracking of goods and forklift fleet increases the control capability and optimization potential of all material flows and delivery processes: With the new automated processes and workflows through highly accurate real-time data, you are able to avoid bottlenecks, empty and throughput times, shortages, errors and significantly reduce search times. With an automated and intuitive database, retrograde analyses and calculations can be performed at any time. This gives you an overview of the past with the potential to minimize the planning effort and production forecast of the material flow in the future.
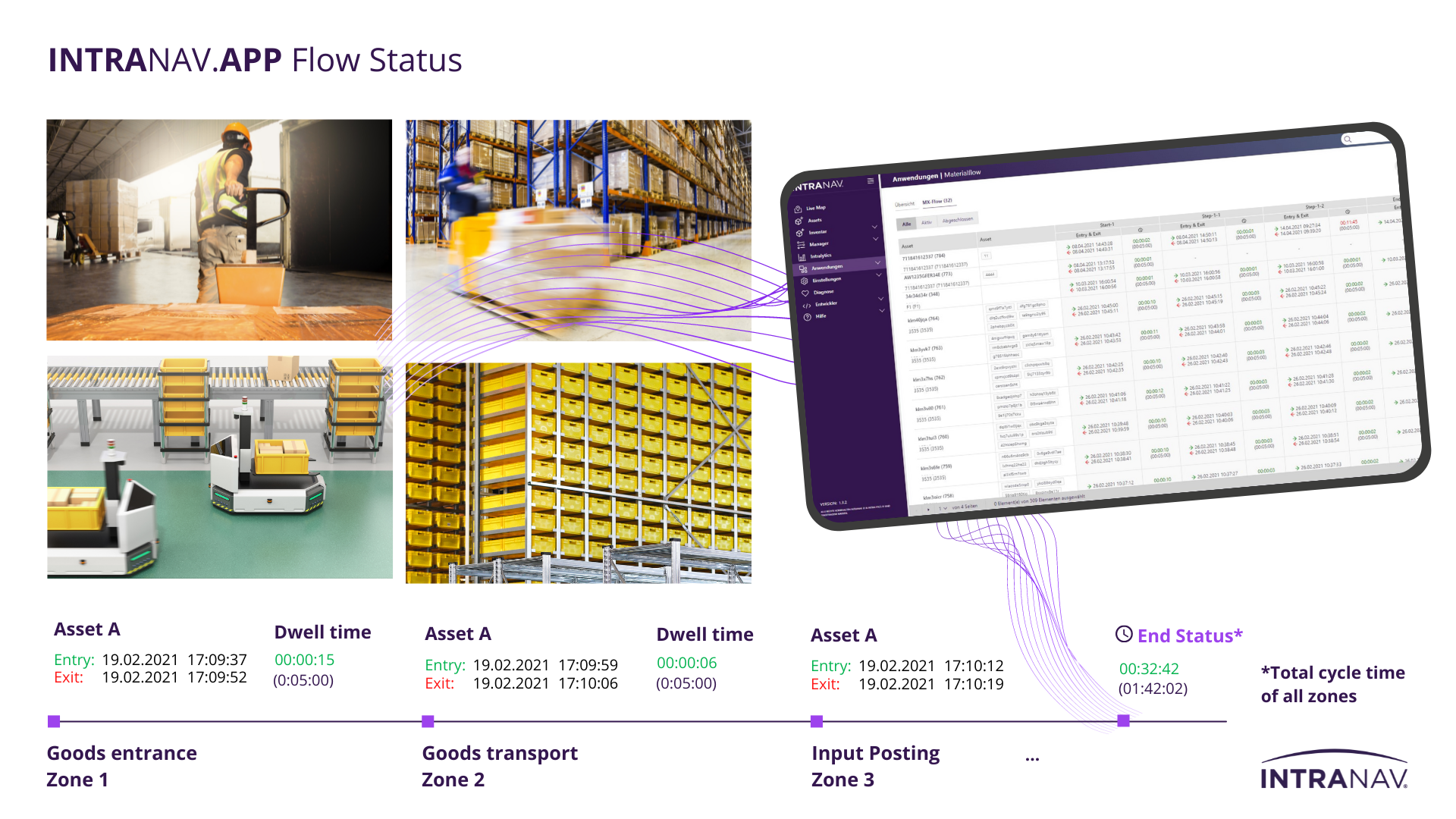
Digitizing your transports with the SMART Forklift Kit
- Orientation: Recognition of vehicle direction for process safety
- UWB: RTLS Optimization for process areas and safety zones
- GPS-Precise: Nathless process tracking in indoor and outdoor areas
- RFID: Scanner-less goods transport (incl. Virtual Pallets)
- Fork Sensor: Detection of loading status and fork height
- Open API: Readout and use of vehicle data for process automation
- INTRANAV.IO: Automatic order processing from the central system (ERP, WMS, MES) and virtual orchestration
Key benefits from automated processes and workflows in the block storage warehouse
- Increased picking productivity and clarity
- Reduces unproductive work such as manual scanning
- Virtualization and scannerless posting in the warehouse management system of the actual storage location in the block warehouse
- Automated warehouse control through process virtualization
- Reduction of search times
- Cost savings through reduction of transport idle times
- Reduction of manual control times
- Warehouse event triggers accelerate material handling
- Cost savings through Auto-Ident and integrated UWB & RFID technology.
- Increased flow of goods order processing through driver navigation
- Automatic order pool processing from central systems (ERP, WMS, MES)
- Safety sensors for increased safety in the warehouse
- Transport and material flow analyses as a prerequisite for optimized goods flows
- Industrial interfaces and API for implementing RTLS data into your warehouse applications
Regardless of the type of warehouse and technology you use to organize your warehouse, INTRANAV offers you the most economical solution to optimize your intralogistics processes with real-time data-driven process solutions. Our cost-effective enterprise solution can be flexibly integrated into warehouse or production management and adapted to other fields of application, such as virtual eCommerce logistics, dynamic material replenishment or production control.
Our INTRANAV VIRTUAL Warehouse Solution is also interesting for you, contact us to talk about optimization possibilities of your production and logistics workflows already today!