03.03.2021
Intelligent transport order control and reduced sequencing efforts
for lean production
In the tractor pre-assembly of our client from the agricultural machinery industry, pneumatic add-on modules for the axle are manufactured at one location and then transported by route train to the axle assembly line on the production site, where the axle is assembled. The manufacturer has a very high sequencing effort due to the large number of variance, which is why there is a risk of confusion in picking the components very quickly. The high volume often also makes buffering more confusing. In general, sequencing errors can quickly become expensive if they lead to high rework costs and thus to delays in the completion or delivery of the end products.
In-house production transport must also be planned cyclically to the production cycle so that empty or wasted runs of the route trains are reduced. Here, too, cycle idling or longer throughput times can be avoided and the transport capacity utilization and the transport flow can be optimized by means of a real-time location solution IoT solution from INTRANAV.
Therefore, the manufacturer turned to us to improve logistics control, through component and inventory tracking as well as route guidance from the pre-assembly areas, to minimize waste and to be able to significantly reduce rework costs. The real-time location data obtained is then used to analyze the throughput times of the material and to optimize the material flow.
For one of the leading international
manufacturer for agricultural technology and agricultural machinery
Our customer is one of the world’s leading manufacturers of agricultural machinery and equipment. The product portfolio includes forestry machinery, construction machinery and equipment for lawn and grounds maintenance.
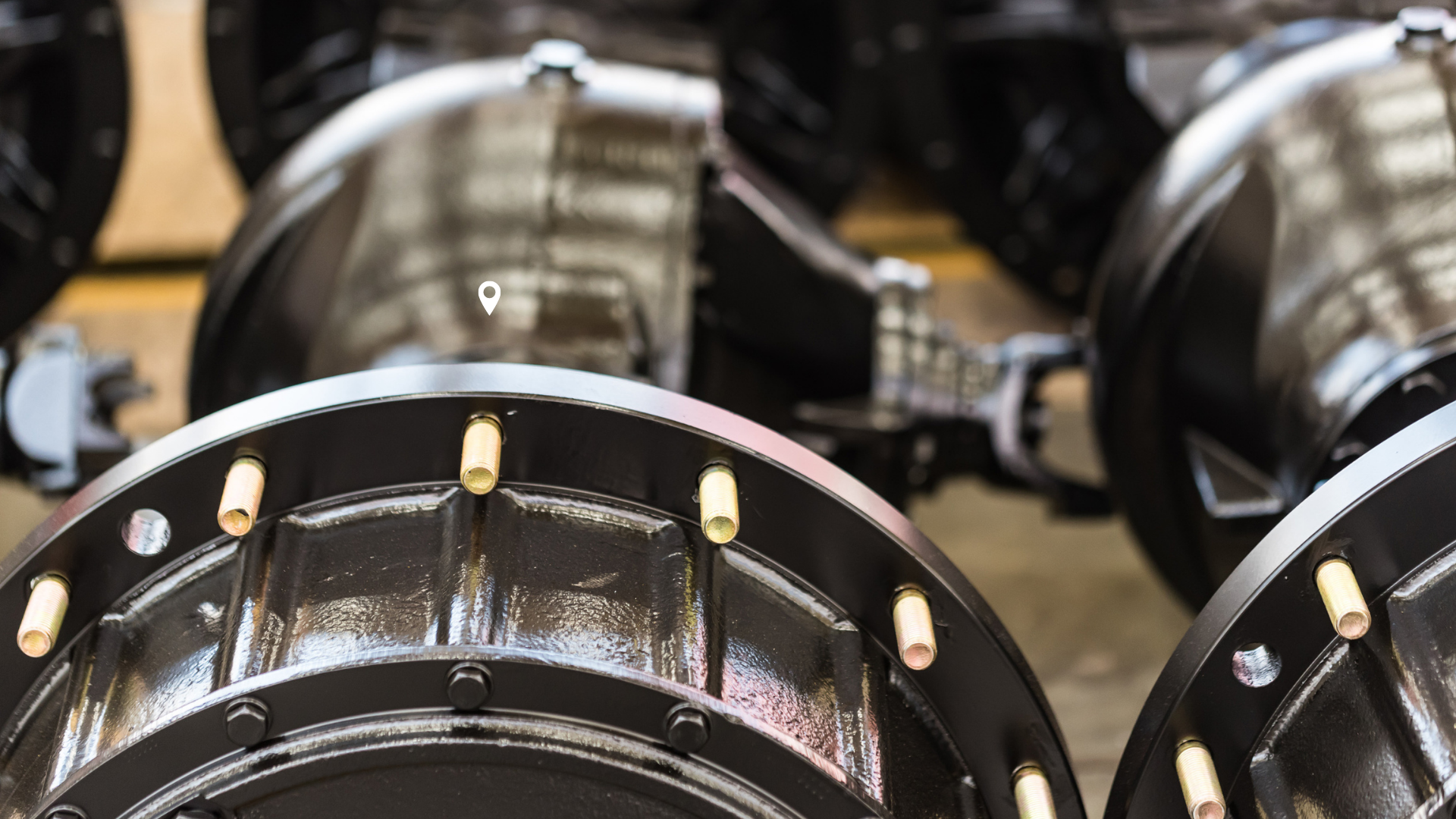
Requirements of our customer
-
1
Order-order matching of the components Load carrier
Due to the high variance in at the main assembly, the pneumatic assemblies must already be recorded in the MAS/SAP system during pre-assembly with the order and the load carrier.
-
2
Intelligent load carriers – INTRANAV SMART Sensors
Real-time location tracking of transport cars via the Digital Twin platform.
-
3
Sequencing/plausibility check during component picking at the assembly line
At the axis assembly, quality control must take place for automatic component picking by matching via a parts list resolution in main and subgroups in order to avoid incorrect assembly.
Solution of INTRANAV
INTRANAV serves with the Real-Time Location Solution at the production line of our agricultural customer all mentioned requirements, so we implemented the case:
Step 1: Assemblies Trolley – Order Matching during Model Production for the Axis
For real-time tracking of pneumatic assemblies, the assembly roundel, the picking crane as well as the transport carts are equipped with INTRANAV.RTLS TAGs. The TAG on the roundel receives the order number from the respective assembly component, which it is carrying on the conveyor at the time. Two geofences (virtual zones) are stored on the roundel itself, which are exclusively responsible for order matching. At the start point of the geofences, the order number of the component is systemically associated with the RTLS.TAG; this is done via an interface in the multi-agent system (MAS) or SAP system of the client. The component is tracked in real-time until the end of the cycle. At the end of the cycle, the assembled module is lifted by crane onto the transport trolley, which can hold a maximum of five different modules (= five different order numbers). A geofence is also stored in each trolley parking space, whereby the system recognizes which assembly module is in which trolley, a (transport-order) order matching has now taken place.
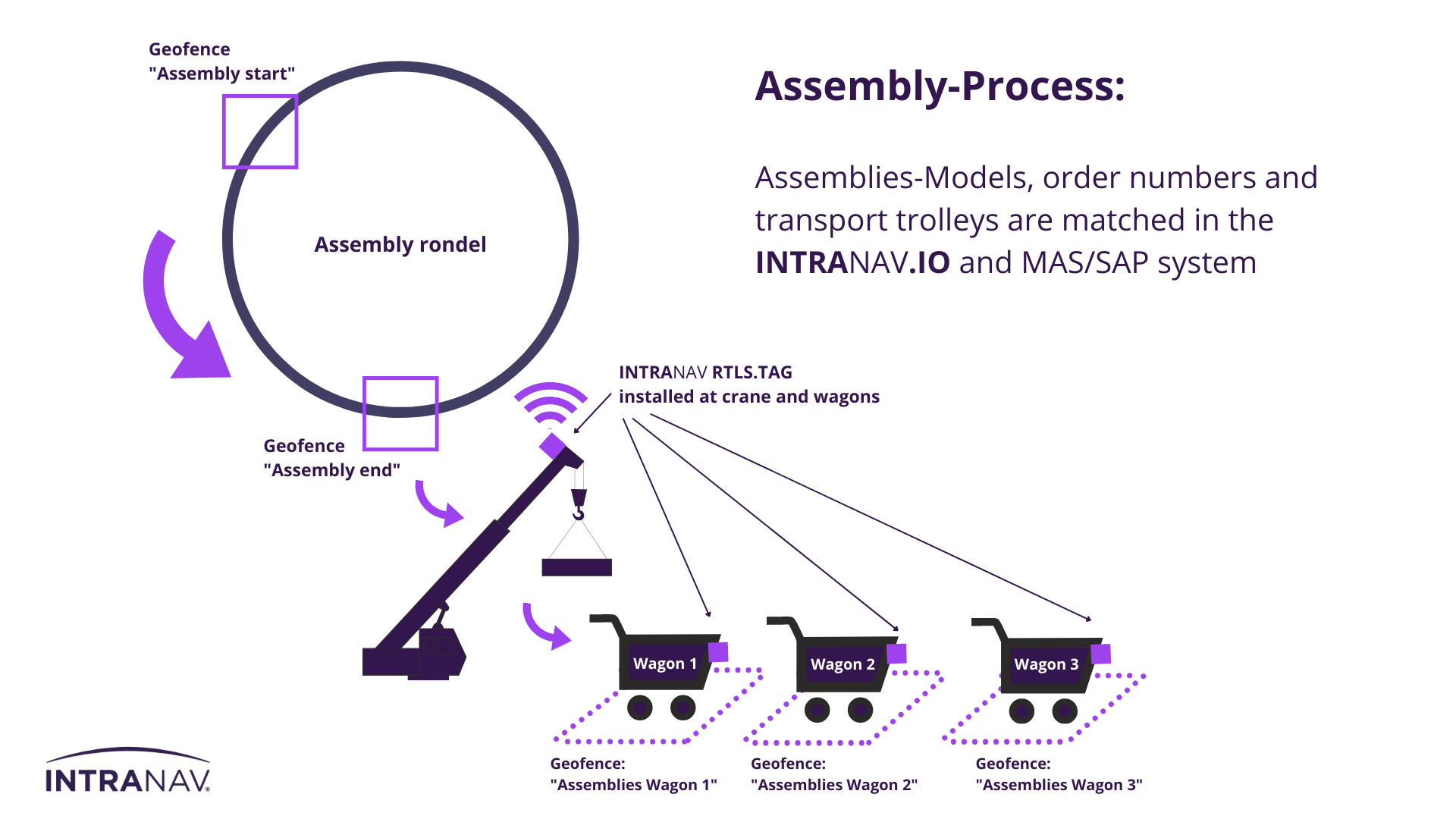
Step 2: Real-time plausibility check during assemblies-model assembly on the axis assembly line
After carriage matching, the assemblies-models are transported to the axle assembly line. Dynamic geofences are stored on the transmission skid via INTRANAV.IO, whereby a plausibility matching process takes place. The parent assembly number carries all of its child sub-assembly numbers in its BOM structure, which allows the system to match them to avoid installing the wrong components. The INTRANAV system checks if the assembly & order number from the skid matches the trolley. The crane picks according to a defined sequence (FiFo). The plausibility check is done by order number matching of the component skid. If the match is positive, the crane picks at the conveyor.
If the plausibility check is negative, this is indicated on the dashboard via INTRANAV, the incorrect order is recorded in the database and the model is booked as “cancelled” so that the order number is deleted from the crane TAG and the model is not picked.
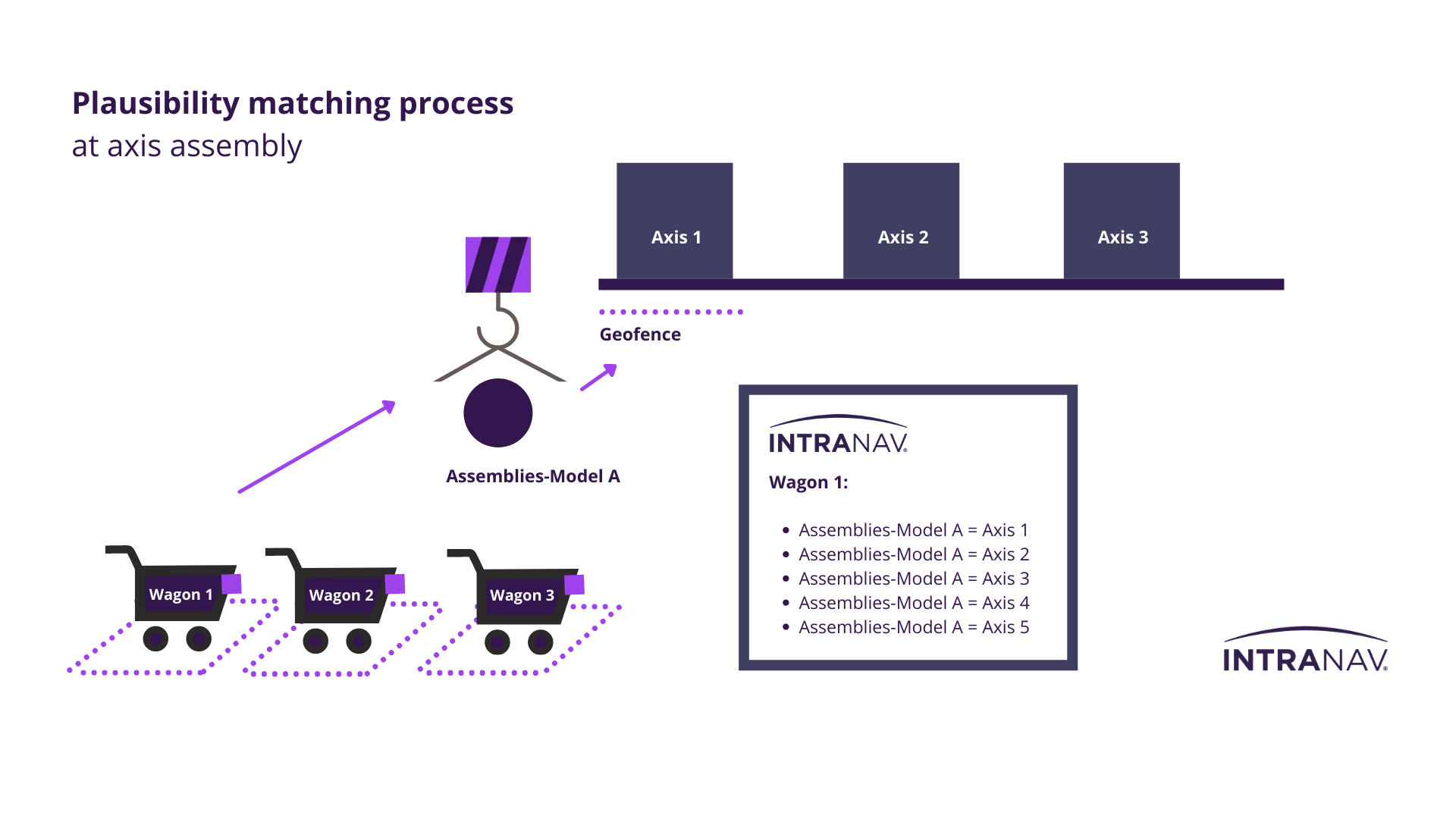
Potential Outlook:
➜ Real-Time Location Tracking of the Route Trains/Milkruns for a dynamic control to pick up the empty wagons. The driver is shown how much time is left for picking up the empty or full SCV wagons.
➜ Tool tracking, due to tool shrinkage caused by borrowing to other workstations or uncoordinated maintenance work. Special tools can be at the right place, at the right time, in the right quality through INTRANAV, because our IoT platform supports as well predictive maintenance.
➜ Path analyses for a lean production flow to be able to analyze unused potentials and wastes via a uniform data basis. For planning for granular time modules and optimization of the paths per analysis.
Results
With INTRANAV’s real-time material flow control and tracking solution at the two workstations, the agricultural machinery manufacturer is able to significantly reduce the high risk of confusion in picking processes.
Summary of the results achieved by our customer with INTRANAV:
● Quality control: High sequencing effort can be safely and reliably controlled by automatic order number matching
● Smart RTLS automation solution reduces the amount of rework required due to sequencing errors
● Reliable calculation of production costs, as there are fewer deviations and wastage
● Timely product completion and product delivery is increased through fluid material flow and proper picking
● Optimization of the transport flow: Empty and wasted runs of the route Trains/Milkruns are minimized with Real-Time Transport-Order Matching
● The Digital Twin reduces search times of the SCV models, as well as the transport trolleys
● Data analysis is the future basis for optimizing route & delivery frequency
● Reduction of belt stock and special load carrier costs
INTRANAV Benefits of order matching and plausibility check
- Digital Twin of components via INTRANAV.IO: Real-time component material flow tracking for maximum process reliability and reduction of search times
- Transport order matching / intelligent transport order assignment to avoid empty and wasteful runs
- Sequencing check and plausibility check to avoid the assembly of wrong components
- Real-time alerts for incorrect material placement from specified zones
- “Bundle” capture and association of individual models and associated transport carts in the INTRANAV.IO and SAP system
- Replacement of scanning activities by automated recording (booking in and out) by geofences in internal transports
- Coherent data acquisition and provision for analysis formats
- Various innovative interfaces enable connection to all common ERP, EWM and CRM systems and databases, as well as to Power BI, SQL Server and several others. With data coupling, further processing and use for optimizing logistics and supply chain processes as well as the entire information flow is possible.
INTRANAV offers a highly flexible and cost-effective enterprise solution, ideal for automotive, aerospace, logistics or production. Further fields of application are for example in the area of production line automation; automatic cycle feedback, line balancing/production leveling, “Just in Sequence” – provision for the right sequence, add-on for worker information system (Paperless Production) or zone-based control of automatic plant systems.
Our INTRANAV Production Solution is also interesting for you, contact us to talk about optimization possibilities of your production and logistics workflows already today!