08.10.2020
eCommerce warehouse optimization through automatic goods posting and control
The digitalization of logistics is increasing rapidly, the advantages are obvious. The numerous added values such as error avoidance, time savings and forecasts for better planning are also proven and potential can be leveraged piece by piece.
A concrete example of this is the use of the INTRANAV multi-technology platform at a medium-sized logistics company in Hesse that handles international logistics for various online retailers and brands. The company has its finger on the pulse of the times, has recognized the added value of digitization, and relies on the flexibility and process reliability it provides. Employee fluctuations, booking errors, process changes, or even pandemics are some of the disruptive factors that can be compensated by modern digitization solutions.
The logistics company already relies on a modern ERP system from SAP (SAP Business One), operated on the Google Cloud, which makes the implementation of the INTRANAV.IO IoT platform very easy.
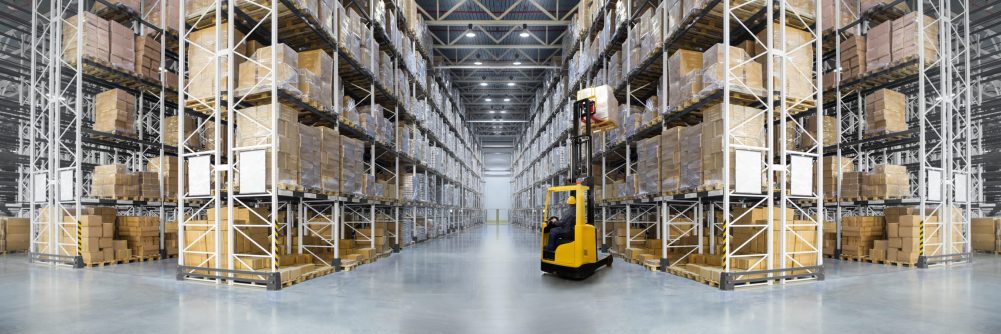
Challenges of our customers in the warehouse
-
1
Goods receipts should be automatically checked and booked
Not every piece of goods should have to be scanned individually, but only the cartons in which the individual pieces of goods are transported into the department store. The goods content must be recognized and booked in the SAP ERP system with reference to the carton.
-
2
Automatic completeness check of incoming goods
The cardboard boxes must be reliably checked for completeness in the inspection area without manual inspection.
-
3
Loading of unmixed packages on pallets without manual scanning
Individual packages are to be automatically recorded in the SAP ERP system as a package group, and at the same time it must be recognized where the package and forklift truck are located in real-time.
INTRANAV Solution
The challenge was to provide the goods coming from Asia with an RFID label so that incoming goods could be automatically checked and booked directly in the warehouse using RFID gates. Individual items are not tagged with an RFID TAG, but rather the cartons. By linking the NVE (number of the shipping unit) and carton number to the RFID TAG UID (Unique Identifier), a consistent number range is created, which creates the reference of the goods content to the RFID label.
The goods are delivered to the bridge and unloaded into the goods receiving area. In this process, the RFID gates recognize the cardboard boxes and check the delivery for completeness. In the next step, the unmixed packages are loaded onto the pallet. In this process, the scanning step has already been eliminated thanks to the Auto-ID technology. The finished package composites are also transferred to the ERP system as a virtual package composite. The INTRANAV.IO platform uses real-time data to generate the digital twin of the booking and warehouse processes. The data of the parcel network is then transmitted to the SAP Business One ERP system via INTRANAV.IO interfaces.
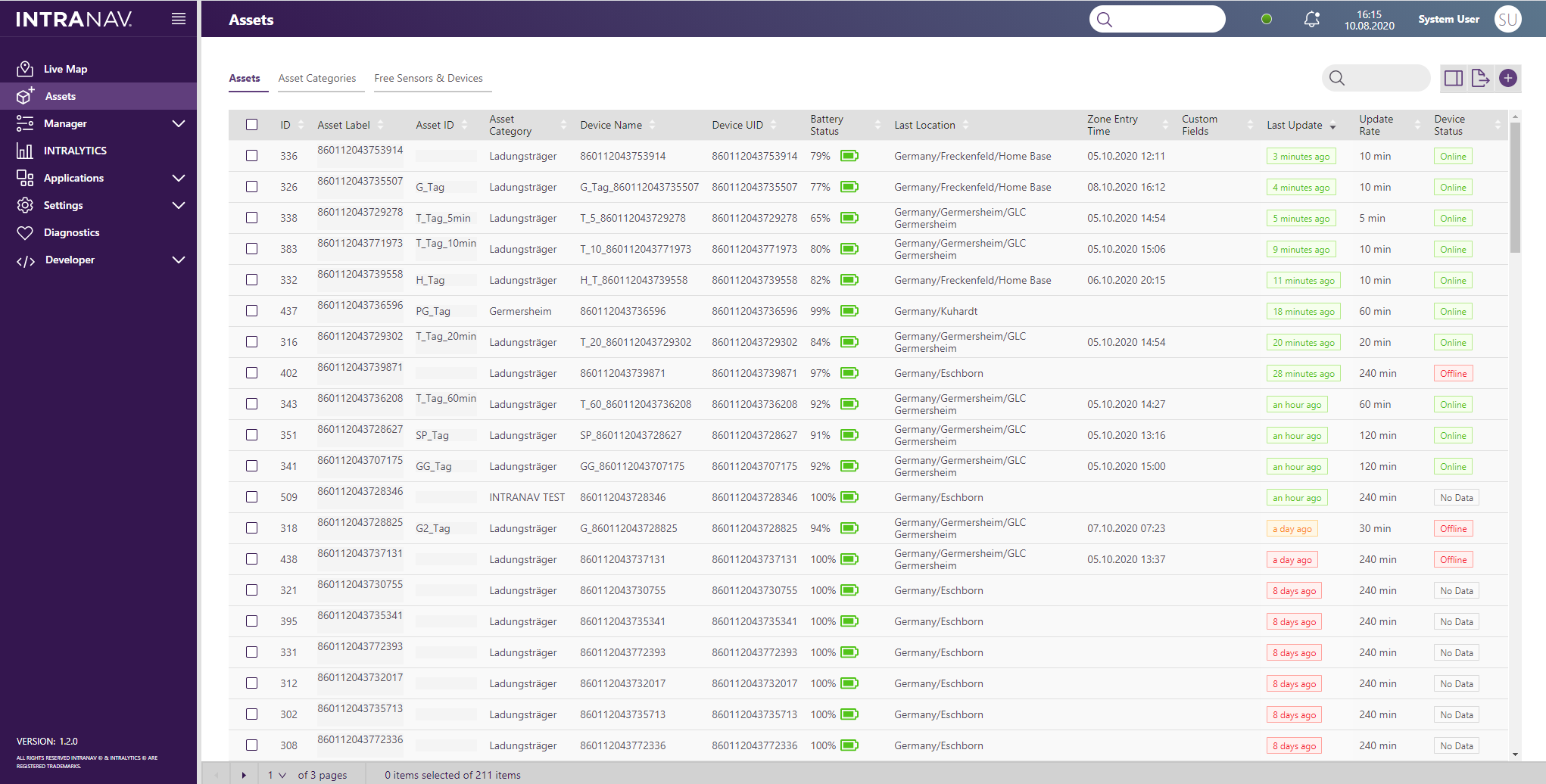
An interplay – optimization of the eCommerce warehouse process through automatic goods posting and control
The optimization does not stop at this point. Thanks to the centimeter-precise location and storage location identification, barcode scanning is now also no longer necessary when storing and retrieving the bundle in the high-bay warehouse system. The intelligent INTRANAV UWB VehicleTAG with external RFID sensors recognizes the package group as well as the storage location and posts them automatically and in real-time as “goods posting”.
Thanks to integrated fleet optimization, industrial trucks such as forklifts, ants, pallet conveyors are used in an optimized way. A compact and clear display shows, similar to a navigation system, the fastest and safest route to the destination. An OEE (Overall Equipment Efficiency) display also indicates optimization potential in the warehouse. The integrated collision warning also warns of dangerous situations and congestion.
This RTLS case was implemented for our customer TB International GmbH
The successful wholesaler TB International GmbH, with up to 15 textile and accessories brands selling its streetwear to more than 15,000 retailers worldwide, ensures its long-term competitive advantage by applying the latest INTRANAV Virtual Warehouse solution.
From goods receipt to shipping, TBInt. tracks and controls its intralogistics processes with the digitized forklift fleet powered by INTRANAV.RTLS VehicleTAGs+, based on a multi-RTLS layer with UWB and RFID technology. RFID sensors on the forklift enable the transport of pallets without scanning through all logistics zones on the shopfloor, including storage and retrieval to the RFID shelves. This eliminates manual steps, such as barcode scanning, and replaces them with AutoID – all done by the forklift!
Automatic order pool processing is controlled by a central system – the INTRANAV “Transport Pool”. This ensures process reliability, time-efficient transport orders, and vehicle orchestration. With the forklift cockpit “Transport Driver”, INTRANAV facilitates and accelerates order processing by indicating available transport jobs nearby the drivers.
Furthermore, the INTRANAV.IO platform APPs support employees with indications on how to load single-sorted pallets in order to avoid incorrect bookings and packing errors. Also, using events based on current location information and product identification, TBInt. ensures intelligent control of its processes, e.g. automatic initiation of transport orders by linking to SAP, creation of delivery slips, or the initiation of pick-up orders.
Request your use case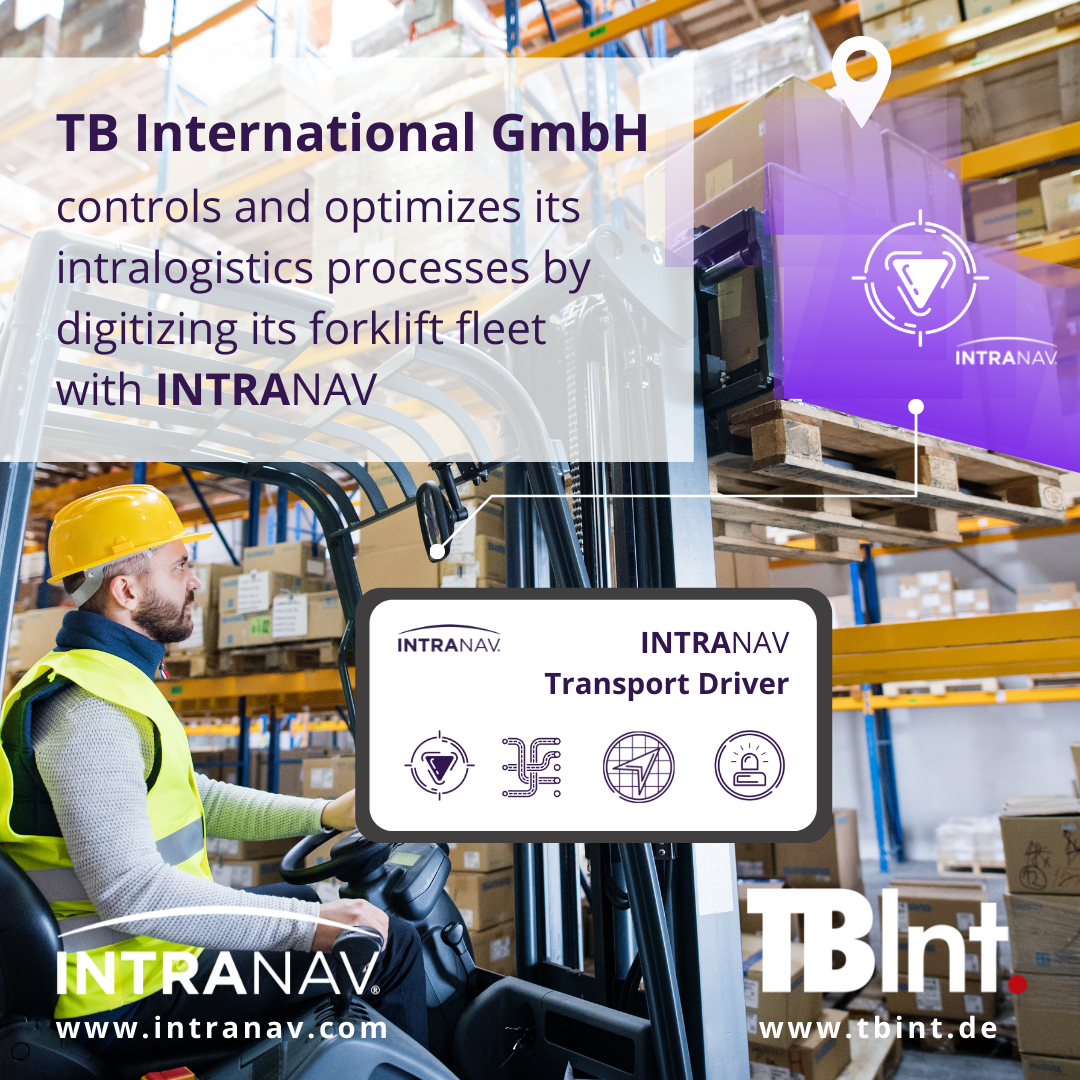
INTRANAV Benefits for eCommerce Logistic
-
- Automatic incoming goods inspection and booking of the entire carton using RFID gates
With the INTRANAV Warehouse “package compound” solution, an RFID label, a so-called RFID-TAG UID (Unique Identifier) and a consistent number range can be generated on the cardboard box. This generates the reference of the goods content to the RFID label, which is automatically posted in the SAP ERP system by INTRANAV real-time data.
- Significant reduction of scanning processes through Auto-ID technology
With the transport of the entire incoming goods cartons through RFID gates, the INTRANAV.IO IoT platform, coupled with SAP ERP, recognizes to what extent the delivery is complete and automatically posts it. Single-variety packages can thus be automatically recorded and booked. Individual, manual scanning processes are no longer necessary, which saves a lot of time. Thanks to the centimeter-precise location and storage location identification, barcode scanning is also no longer necessary when storing and retrieving the bundle in the high-bay warehouse system. This is because the intelligent INTRANAV UWB VehicleTAG with external RFID sensors recognizes the parcel compound as well as the storage location and posts them automatically and in real-time as “goods posting”. - Booking of finished package connections as “virtual package connection
The INTRANAV.IO platform uses real-time data to generate the digital twin of the posting and warehouse processes. The data of the parcel network is then transmitted to the SAP Business One ERP system via INTRANAV.IO interfaces.
- Transport flow optimization of the fleet by displaying the fastest and safest route
A compact and clear display shows, similar to a navigation system, the fastest and safest route to your destination. - OEE (Overall Equipment Efficiency) proposals via the INTRANAV.IO
An OEE (Overall Equipment Efficiency) display also indicates optimization potential in the warehouse. - Collision warning system
The integrated collision warning system also warns of dangerous situations and dust formation.
- Automatic incoming goods inspection and booking of the entire carton using RFID gates
Our INTRANAV Warehouse Solution is also interesting for you as a logistician. Contact us today to talk about optimization possibilities for your warehouse and logistics workflows!