01.08.2022
Optimizing Just-in-Time & Just-In-Sequence Processes with RTLS
In manufacturing, warehousing and logistics, using RTLS technology and strategies to optimize processes results in a large amount of time and money saved. In industry 4.0, automation is key to staying competitive in whichever industry you’re in, and making use of IoT technology moves items faster through facilities, results in fewer errors and keeps organizations in control of their operations. In this post, we’ll go over how to optimize just-in-time (JIT) and just-in-sequence (JIS) production.
What’s the Difference Between Just-in-Time (JIT) &
Just-in-Sequence (JIS)?
In the context of supply chains and facilities, just-in-time (JIT) refers to delivering goods at the right time, before they’re needed for assembly. For example, a candle manufacturer would like both the candle wax and glass jars to arrive at the assembly line, at the right time, so they can be combined to produce candles together. If any items are missing, it can result in long delays or products taking up space on warehouse floors, blocking production from moving forward.
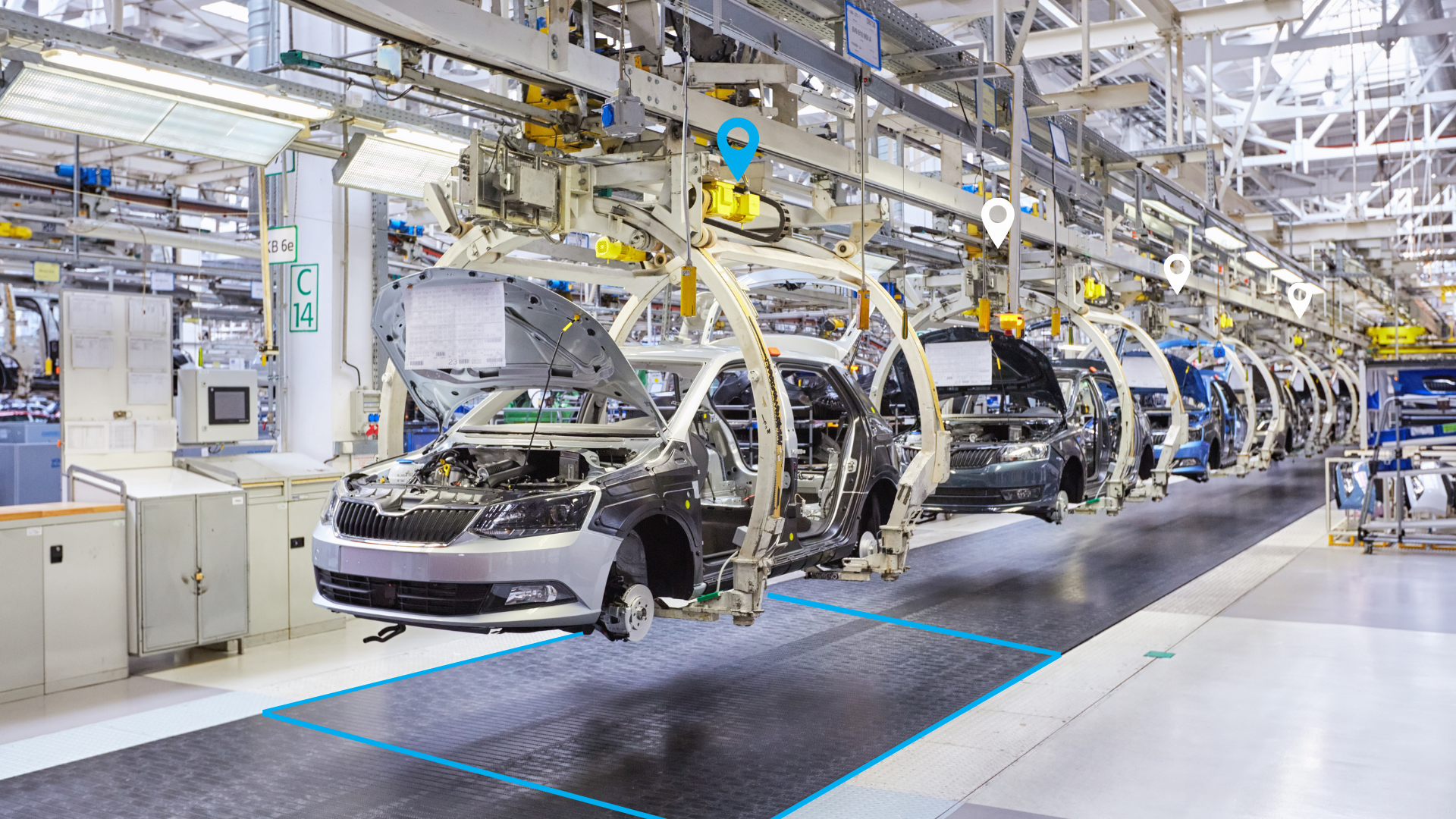
On the other hand, just-in-sequence (JIS) requires different parts to arrive in the specific order needed for assembly. For example, if the silver car is scheduled to be assembled first, parts for this car should be entered into the assembly before that of a blue or black car. If the order of parts are mixed up, this leads to errors in assembling products down the line.
Overall, there are 3 main types of JIS processes, including:
● Pick to sequence: Having inventory on-site and putting parts in order of sequence.
● Ship & receive to sequence: Ordering and receiving parts in the right sequence, for example, loading trucks with the parts in the right order and maintaining that order until they reach the assembly line.
● Assemble to sequence: This is the production process of putting together parts, happening in the exact sequence needed.
How Just-in-Time (JIS) Works with Rack Changes
A rack is a storage area that’s meant to hold a part or product that’s at a specific stage of the production process. As parts progress in the production cycle, the rack they are stored in changes. Rack changes are very common in warehouses, where items are placed in-between processes. As items are transferred to different racks as they progress through the production process, it’s important to maintain the right sequence or order in which they were made. Otherwise, errors may occur and may not be noticed until much later in the process. This can result in a lot of time and money needed to be spent fixing the error, which is why it’s important to continuously check that all parts are in the right order.
How to Optimize your Just-in-Sequence (JIS) and
Just-In-Time (JIT) Processes
To ensure JIT and JIS processes are running smoothly, positioning technology can provide organizations with a layer of visibility over their production. By adding location tracking tags & sensors to the various parts needed to be produced as well as machinery and forklifts, you can ascertain the exact position of each part and see how they’re all moving through the facility. With an IoT platform like INTRANAV.IO, optimized routes can be calculated to help items arrive at the right time for JIT processes, and location tracking and material flow can help organizations see the exact products entering an assembly line, making sure they’re JIS.
Case Study – How an Agricultural Machinery Manufacturer
Harnessed IoT to Optimize their JIS Production Process
A large agricultural machinery manufacturer turned to INTRANAV, an Inpixon company to optimize their JIS efforts because they had a wide variety of tractor parts. They needed to ensure that the right tractor components were being produced together, and to prevent any expensive sequencing errors. They used INTRANAV.IO for inventory control, material flow management and real-time location tracking using the digital twin.
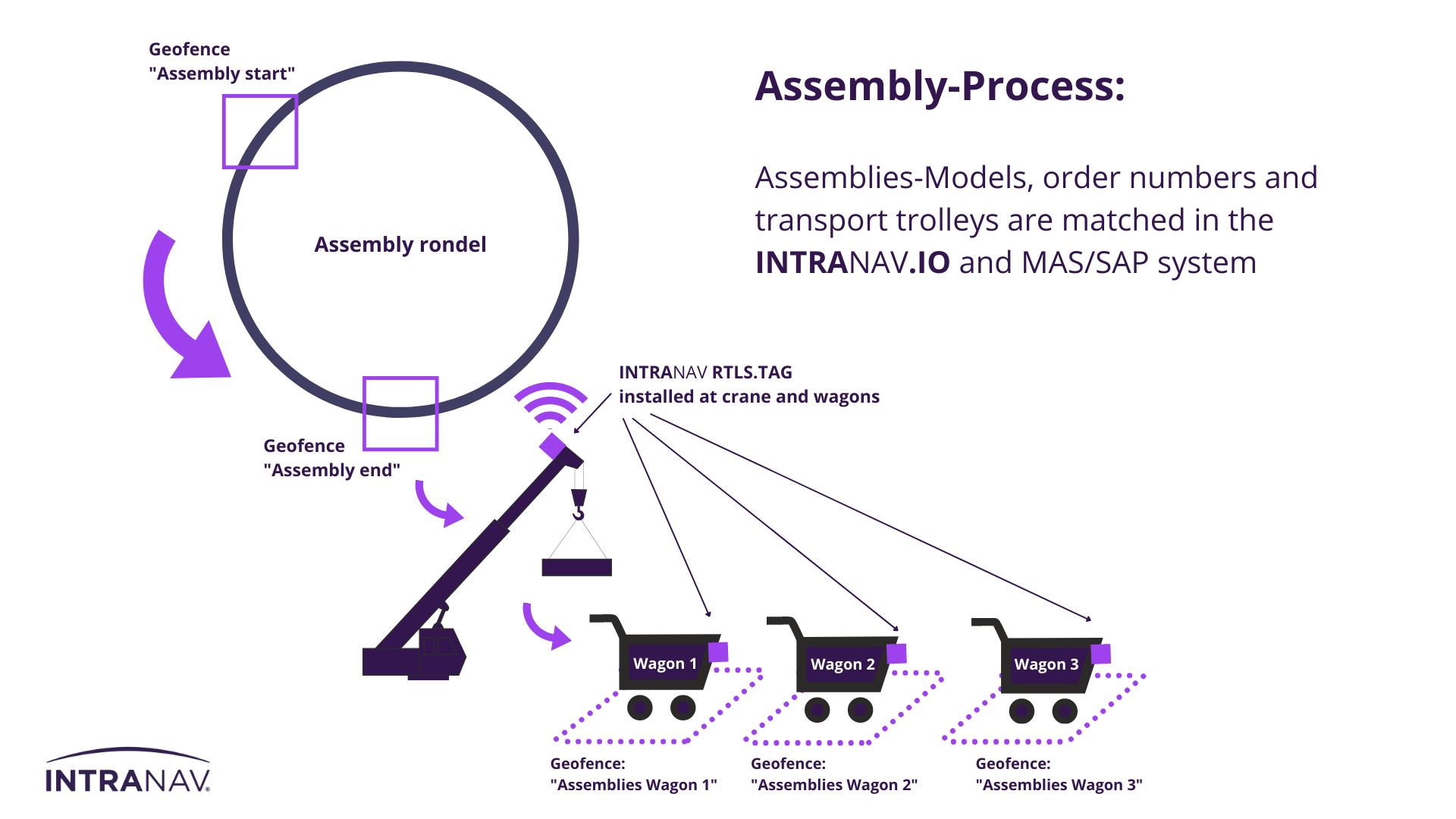
INTRANAV, an Inpixon company tagged all the parts involved in the production process, including pneumatic assemblies, the assembly roundel, the picking crane and the transport carts. They also had a geofence in each trolley parking space, so their system would recognize which assembly module is in which trolley. This resulted in carriage matching, so the right items arrived at the assembly line in the right order. If items are placed in the incorrect order, the system would cancel the order automatically and record it in the database so the organization could see exactly what happened and where.
As a result, the company achieved:
● Improved quality control with automatic order number matching
● Reduced amount of sequencing errors and reworking due to RTLS automation
● Timely production completion and product delivery through smooth material flow
Ready for a more in-depth exploration of how an IoT platform can optimize your JIT and JIS processes and boost ROI? Talk to our team today.
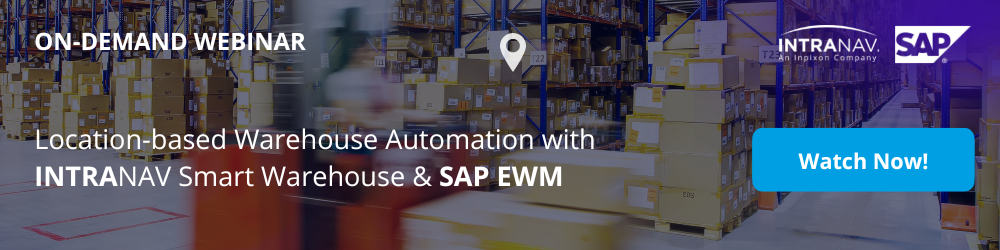
Author
Ersan Guenes, SVP Product IIoT
Ersan Guenes is Senior Vice President (SVP) of Product for IIOT (Industrial Internet of Things) at INTRANAV, an Inpixon company.
Learn more about Inpixon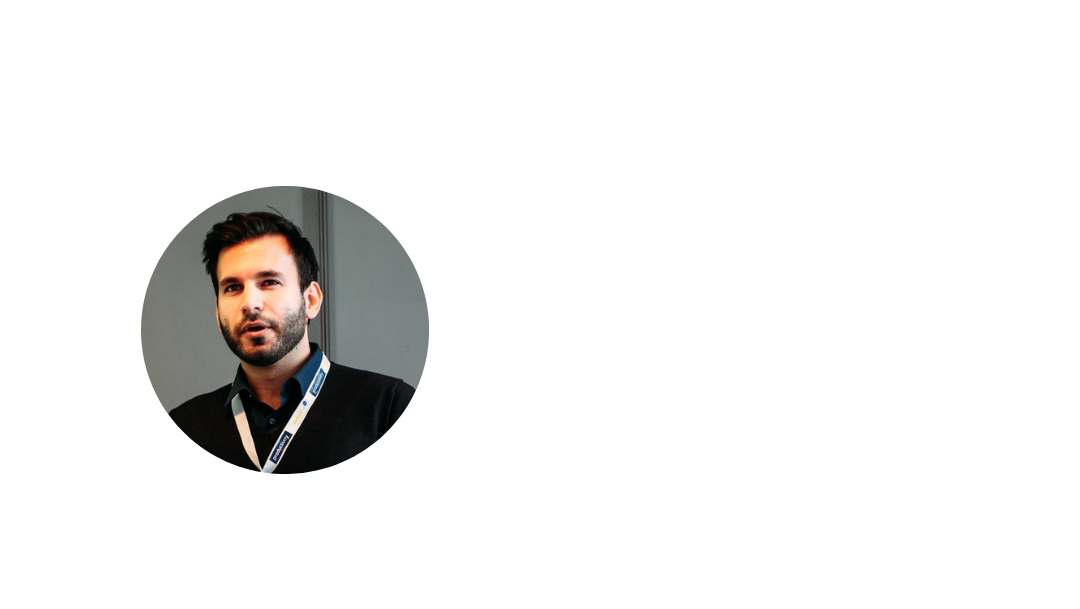