10.01.2022
Intelligent Production Digitization
How can sequencing efforts in production be minimized and transport orders intelligently controlled?
The complexity of production plants is constantly increasing, greater customer numbers and, above all, increasing numbers of products and variants, which go hand in hand with growing production sites and distribution centers, are expected in the coming years.
More than ever, therefore, the supply chain and production are focusing on the digitization and networking of process flows and their data evaluation in order to react more agile and resilient to production fluctuations, but also to be able to analyze time and resource wastage in production logistics and to densify these through intelligent automation solutions.
Challenges that are brought to us by production managers:
- ● Risk of component picking errors on the assembly line due to a high number of variants
- ● High time expenditure for the manual check of the matching components
- ● High material stock on the assembly line makes buffer zones cluttered
- ● High costs due to post-processing effort
- ● Delay in completion and delivery
- ● Cycle idle times and extended throughput times caused by asynchronous material supply of the transport vehicles
- ● No sufficient data basis for optimizing the material flow
Link between IT and Operations Technology:
Digitization of real-time location data with the INTRANAV RTLS platform and ERP systems
as a prerequisite for digitally connected production control
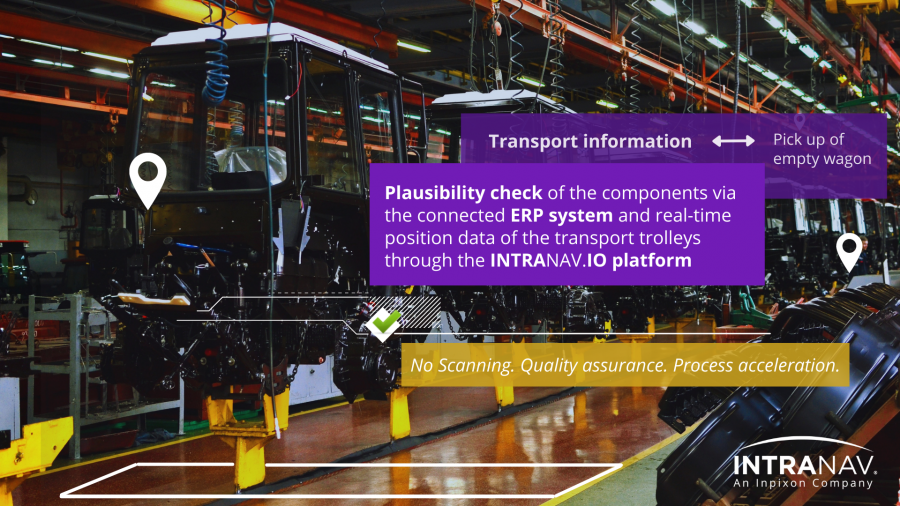
The central prerequisite for intelligent manufacturing is the interaction of ERP systems and RTLS sensor technologies, such as ultra-wideband, BLE or RFID, which track the real-time positions of load carriers, logistic vehicles such as AGVs, route trains or forklifts throughout the plant. With IoT systems such as the INTRANAV.IO platform, the position data is digitized, managed and allocated for process automation in connection with SAP or other ERP systems. The transport vehicles as well as the wagons, which are loaded with the corresponding material and component groups, can thus be virtually connected with each other. The interaction of the software systems makes the production intelligent, whereby the material flow can be designed sustainably and the overall plant efficiency can be increased.
Learn how INTRANAV RTLS Intelligence can be used in the production of an agricultural machinery manufacturer:
● Sequencing checks and plausibility checks can be implemented automatically, which avoids the reworking effort caused by the assembly of incorrect components
● Can save time (turnaround times) through automated quality checks
● The material supply is available at the required time, in the correct quantity, at the correct cycle, avoiding cycle idle times
● Empty and wasted runs of Route Trains can be minimized with Real-Time Transport-Order Matching
● How path and material flow analyses can be done to be able to analyze unused potentials and wastes via a standardized data basis