30.03.2023
The Future of Inventory Management:
How RTLS is Shaping the Industry
Inventory management is a complex task that requires a high level of accuracy and efficiency. Today, companies of all sizes face challenges triggered by rapid technological advances in inventory management and the accompanying demands on systems and processes.
Redundant workflows, errors in paper-based processes, disruptions in material deliveries, and inaccurate data collection can lead to time-consuming and costly follow-up activities, including rework, high inventory levels, poor on-time delivery, and material availability bottlenecks. Manually collecting and managing data can lead to a loss of control over inventory and the delivery process. Unoptimized inventory levels tie up capital unnecessarily and can lead to shortages, delays, and out-of-stocks.
To overcome these challenges, companies are looking for innovative solutions, such as Inpixon’s INTRANAV Inventory Manager, to help them ensure efficient and accurate inventory management, especially for rotating items in their inventory.
Another challenge in inventory management is keeping track of inventory and ensuring that the right item is available in the right place at the right time. This is where innovative solutions based on real-time location information can play a significant role.
Benefits of optimized inventory management through real-time location information
With a real-time location system (RTLS) solution, companies can not only optimize inventory levels but also automate their processes and reduce human error. Moreover, such a system can improve collaboration and communication within the supply chain and help ensure that orders and deliveries are made on time.
Additionally, RTLS solutions are able to support forecasting and sales planning, which in turn makes it easier to plan and forecast inventory levels.
Overall, it can be said that an innovative solution based on real-time location information can be an indispensable tool for efficient and successful inventory management.
What is INTRANAV Inventory Manager, and How Does it Work?
Inpixon provides advanced indoor and outdoor location-based technology solutions to enable location-aware IoT. Our RTLS technology, which uses a variety of RF standards, offers a wide range of applications and includes proprietary sensors and tags as well as third-party hardware. With our INTRANAV.IO platform, you have the ability to generate, manage and visualize real-time position data to provide a digital twin of your operations, ensuring full visibility and control in real-time.
INTRANAV.IO’s Inventory Manager module ends the tedious search for parts, equipment, load carriers, and tools, whether in the warehouse, on the production line, or in the yard. Through the system, items are quickly and specifically found, and new items are easily registered. Item location data is managed as a “digital twin” in a live map and database, providing an overview of the current location of inventory at all times. This leads to greater efficiency and reduced search times for employees, which in turn means time and cost savings for the company.
The inventory management system provides an automatic notification feature to alert staff about specific inventory items. It also has an advanced and simple search form that can be customized to meet specific client needs and provides the ability to search by various criteria such as identification numbers, tracker numbers, and item group types.
Using the search and filter functions, entire groups of items can be identified and moved around the system in bulk as needed. The system also has a geofence-based messaging system that alerts responsible staff when an object leaves the premises.
INTRANAV Inventory Manager helps users manage inventory of nearly any type, including raw materials, finished goods, equipment, containers, boxes, prototype models, rotating equipment, tools, loaners, and more.
How INTRANAV Technology Works for You:
- Real-time location overview of inventory
- Automation of workflows and optimization of processes
- Quick location determination of parts, equipment, load carriers, and tools
- Automatic inventory notifications to personnel
- Search and filter functions for quick searches
- Geofence-based messaging system for monitoring objects
How Will INTRANAV Inventory Manager Shape the Future of Inventory Management?
The rise of real-time location systems is changing the way companies manage their inventory. This technology offers increased accuracy and advanced features that will greatly impact inventory management in the future.
Inventory management is an important part of supply chain management, which involves monitoring, organizing, and optimizing the movement of goods as well as industrial inventory. In recent years, inventory management has evolved significantly due to technological advances and changes in customer behavior. Here are some of the current trends in inventory management:
- Digital transformation: digitalization has fundamentally changed the way companies manage inventory. Companies are turning to digital tools such as enterprise resource planning (ERP) and warehouse management systems (WMS) to automate and streamline their inventory processes.
- Real-time monitoring: using IoT sensors and Wirepas technology, companies can track and monitor their inventory in real time. This enables quick response to changes in inventory and helps avoid overstocking and shortages.
- Predictive models: Machine learning-based predictive models enable companies to improve their inventory forecasts, allowing them to make better decisions regarding inventory, orders, and production.
- On-demand deliveries: Customers expect fast and reliable delivery. To achieve this, companies need to optimize their inventory processes and ensure they always have the products they need.
- Sustainability: More and more companies are focusing on sustainability and are adopting environmentally friendly solutions in inventory management, such as the use of recycled materials and energy-saving storage methods.
Inpixon, with its INTRANAV Inventory Manager, plays an important role in the future of inventory management. It offers improved tracking and locating capabilities, greater visibility, streamlined processes, and increased accuracy. With its advanced technology, automatic notification capabilities, and geofence-based messaging systems, Intranav is a valuable solution for companies looking to optimize their inventory processes.
Case Study: Success Story of BMW Group with INTRANAV Inventory Manager
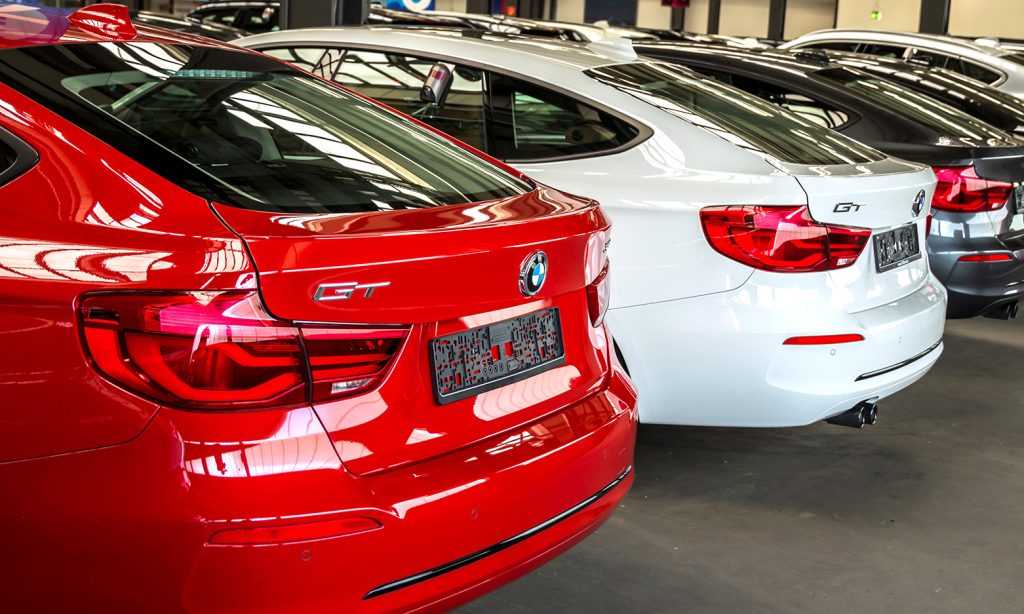
German multinational luxury vehicles and motorcycles manufacturer Bayerische Motoren Werke AG, commonly referred to as BMW, has a dedicated team to deploy, manage, and store design models of BMW Group vehicles. This team requires simple and efficient inventory management and retrieval of multiple models of BMW Group vehicles across numerous warehouse locations. As their previous inventory management system became outdated, they searched for new technology to fulfill their growing needs and streamline their process.
Before discovering Inpixon’s RTLS solution, BMW Group faced many challenges with the software and hardware components of its legacy inventory management system. First, their legacy software was facing end-of-life. This meant that they would no longer get support from the vendor to maintain their inventory management system and that there would be no further updates or development of its features. Moreover, their former inventory management system relied on barcode readers that were no longer being manufactured, so they could not be replaced in case of loss or damage.
Aside from the issues stemming from their legacy vendor, BMW Group was also looking for:
- A more advanced solution that would go beyond barcode readers and could track their assets’ location in real time.
- A new hardware system that would not interfere with existing frequencies. Their new solution needed to operate on separate frequency stations so it would not affect the functionality of existing systems.
- More battery capacity than is standard for most companies.
- A superior technological platform and hardware solution that was location-aware but understandably showed concerns surrounding installation complexities, cost, and potential hindrances.
After reviewing multiple vendors, the solution BMW Group chose and implemented was Inpixon’s INTRANAV.IO Inventory Manager. These were the results:
- Greater efficiency for more than 500 employees utilizing the system. This led to considerable time and money savings for the company.
- A fast, smooth, and successful installation process of the initial solution within two days, with no disruptions to their current operations
- The complete shutdown of their legacy system. They are currently powering down their old process, citing that there was no comparison between their previous method and Inpixion’s INTRANAV.
- Daily time saving due to fewer errors in inventory management. Since fewer vehicles are lost, there is a lower need to deploy personnel to relocate and return prototypes to their proper location.
- Greater cost savings, efficiency, and simplicity in the ability to search for and track down each vehicle. Employees no longer need to carry a device with them at all times – they can use the INTRANAV.IO mobile app to search for vehicles on their phones. This leads to a much faster process, making it easier for employees to be productive. It also leads to significant cost savings for BMW Group because they no longer need to maintain and replace scanning/reader devices for their employees, as everyone is already equipped with a smartphone.
- A fully functional inventory management tracking solution that operates on a frequency that doesn’t interfere with other operations. This ensures the smoother operations of all new and existing systems in their facilities.
Read more about the Inventory Management Use Case in the Success Story about BMW Group!
If INTRANAV Inventory Manager or any of our other services are of interest to you, contact us to discuss optimization possibilities for your manufacturing and logistics workflows today!
Autor
Ersan Guenes, SVP Product IIoT
Ersan Guenes is the Senior Vice President (SVP) of Product for IIOT (Industrial Internet of Things) at Inpixon.
Mehr über Inpixon erfahren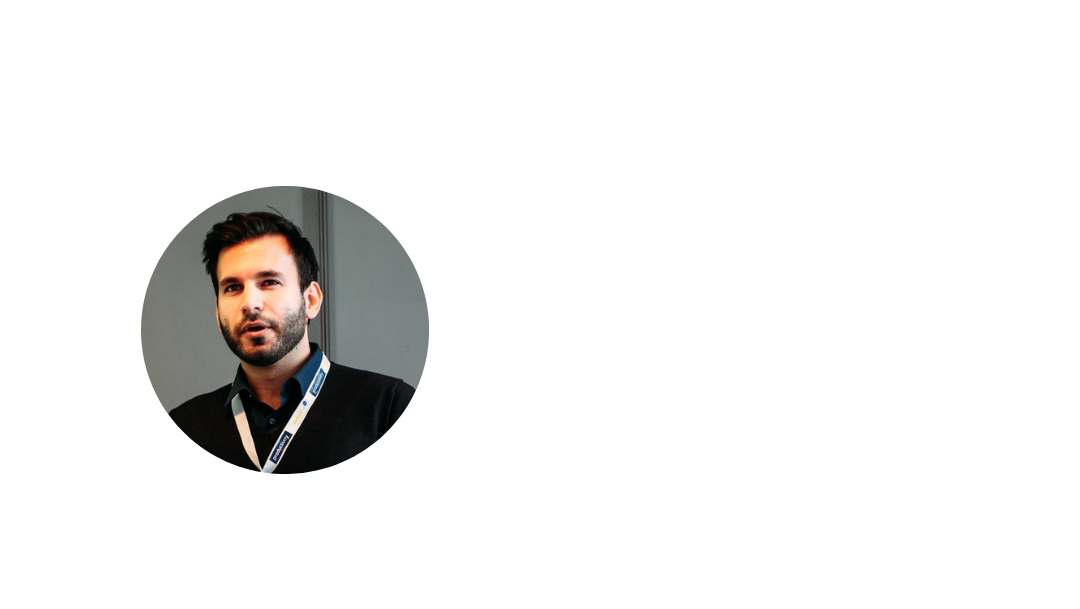