05.02.2023
How TB International GmbH increased productivity by 40% with INTRANAV Smart Warehouse and the integration of RFID, UWB and SAP
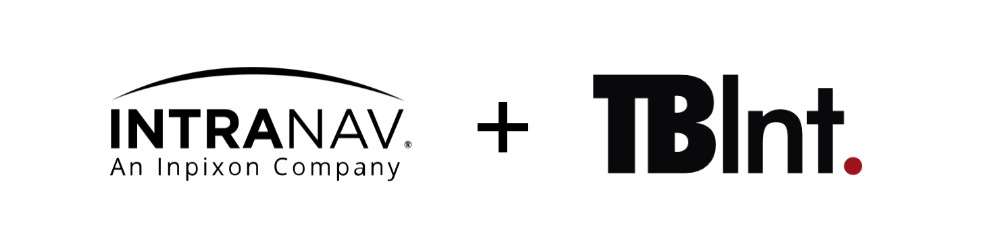
The Company
TB International GmbH (TBInt.), one of Germany’s leading fashion wholesalers
TB International GmbH (TBInt.) distributes over 15 textile and accessories brands, selling its fashionwear to more than 15,000 retailers worldwide. Dedicated investment into technologies that drive digitization and automation of their logistics processes is an important pillar of their corporate strategy. With Inpixon’s INTRANAV Smart Warehouse solution, TB International helps ensure the company’s long-term competitive advantage.
The Challenge
Across 25,000 square meters of logistics space in their large Groß Gerau warehouse, where dozens of 40-foot containers are delivered daily and up to 1.3 million cartons leave the warehouse each year, TBInt. had to introduce a new process for goods registration, processing, intralogistics transport and preparation of outgoing goods in order to be able to continue to overcome growing cost pressures and guarantee fast delivery times.
Here are some of the biggest warehouse challenges this organization was facing:
- High number of manual identification and confirmation steps
Many manual logistics workflow steps from inbound to outbound, such as sorting, searching, and manually scanning cartons, across all logistics zones of the warehouse. - Mispostings and packing errors
From time to time, incorrect bookings and packing errors occur, which result in costly process reworks and additional time expenditures. - Transport orders cause long search times for forklift drivers
Forklift drivers often can’t quickly find where available transport orders are located, resulting in empty runs, bottlenecks and delays. - Inefficient routes and lack of storage space, transport and goods flow transparency
Forklift drivers attempt to navigate the dynamic environment with little visibility into what’s the best route to take to their destination or where’s the most efficient and available storage space to take certain goods. - Errors in storage and retrieval processes
Forklift drivers store a pallet in the wrong location or pick up the wrong goods, resulting in critical inefficiencies and errors for outbound and retrieval processes. - High sorting effort
High manual sorting effort in goods receipt processing.
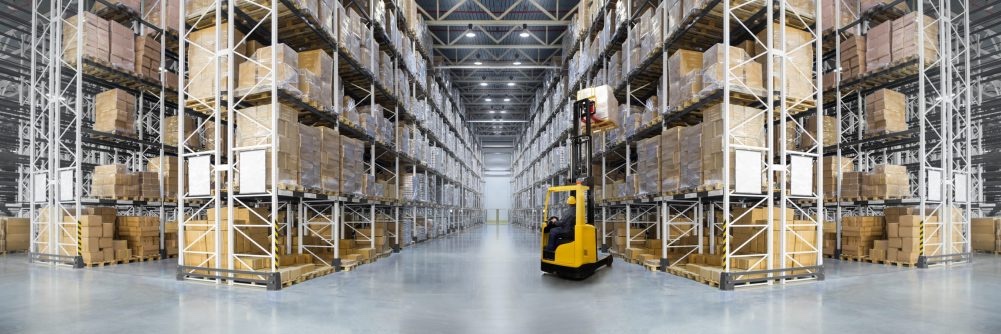
The Solution
INTRANAV Smart Warehouse Module with RFID and UWB Technology
TBInt. partnered with INTRANAV to create an agile approach for smart warehouse processes and within just a few months, the first field tests were up and running.
The prerequisite for the solution, in this case, is that the goods, which are delivered in cartons, are already labeled with RFID labels by the manufacturer. As soon as the cartons arrive at the warehouse in Groß Gerau, an automated process chain based on IIoT software and RFID, as well as UWB, starts.
1. Automatic control and posting of goods receipts
The cartons are placed by employees on a conveyor belt, which is equipped with RFID readers. Each carton is identified/recorded by the RFID reader and the contents are retrieved in the INTRANAV Smart Warehouse software.
➜ Instead of manually registering each incoming carton with a hand scanner, RFID technology automatically registers the cartons in the goods receiving area.
2. Real-time digital employee instructions for faster sorting and palletization of incoming goods
At the end of the conveyor, another employee sorts the cartons by type onto pallets. The employee is again supported by the INTRANAV Smart Warehouse system; a monitor shows how many cartons have to be loaded onto which pallets as well as the current pallet loading progress. A finished packed pallet is completed by confirmation in the INTRANAV Smart Warehouse application from the employee. A completed digital pallet bundle is generated by the system.
INTRANAV Smart Warehouse automatically creates a transport order, which is assigned to the next available forklift driver.
➜ This saves employees time, especially when palletizing the goods. The automated triggering of the transport order also saves another work step.
3. INTRANAV Smart Warehouse forklift application supports more efficient order processing
A forklift driver receives real-time information via tablet about what transport orders are ready to be picked up, where they are and where they need to be taken.
➜ Reduces search times and speeds up transport job processing
When picking up the pallet with the forklift, the INTRANAV Smart Warehouse system recognizes which pallet bundle it is via RFID reader on the forklift.
➜ The driver can thus see whether he has picked up the right goods, transport errors can be avoided
The driver is now shown the nearest free storage location (other criteria also possible).
4. Scannerless storage and retrieval of pallets in the RFID rack storage system
The pallet is stored in the rack without a scanner by automatic identification with RFID tags on the rack. The INTRANAV Smart Warehouse system books the pallet in SAP®, ERP or WMS. The driver is also notified if the pallet is stored in the wrong rack.
➜ This step again saves valuable time by eliminating the need to get out of the operator’s cab for checks and scanning operations and ensures correct storage.
5. Real-time warehouse overview of shelf occupancies
The real-time warehouse overview shows how the racks are occupied in real time and if a driver is already heading for a rack location.
➜ Delivers transparency and a comprehensive overview of storage utilization and
availability
The Results
INTRANAV Smart Warehouse Module and UWB + RFID technology helps TB International increase efficiency by nearly 40%.
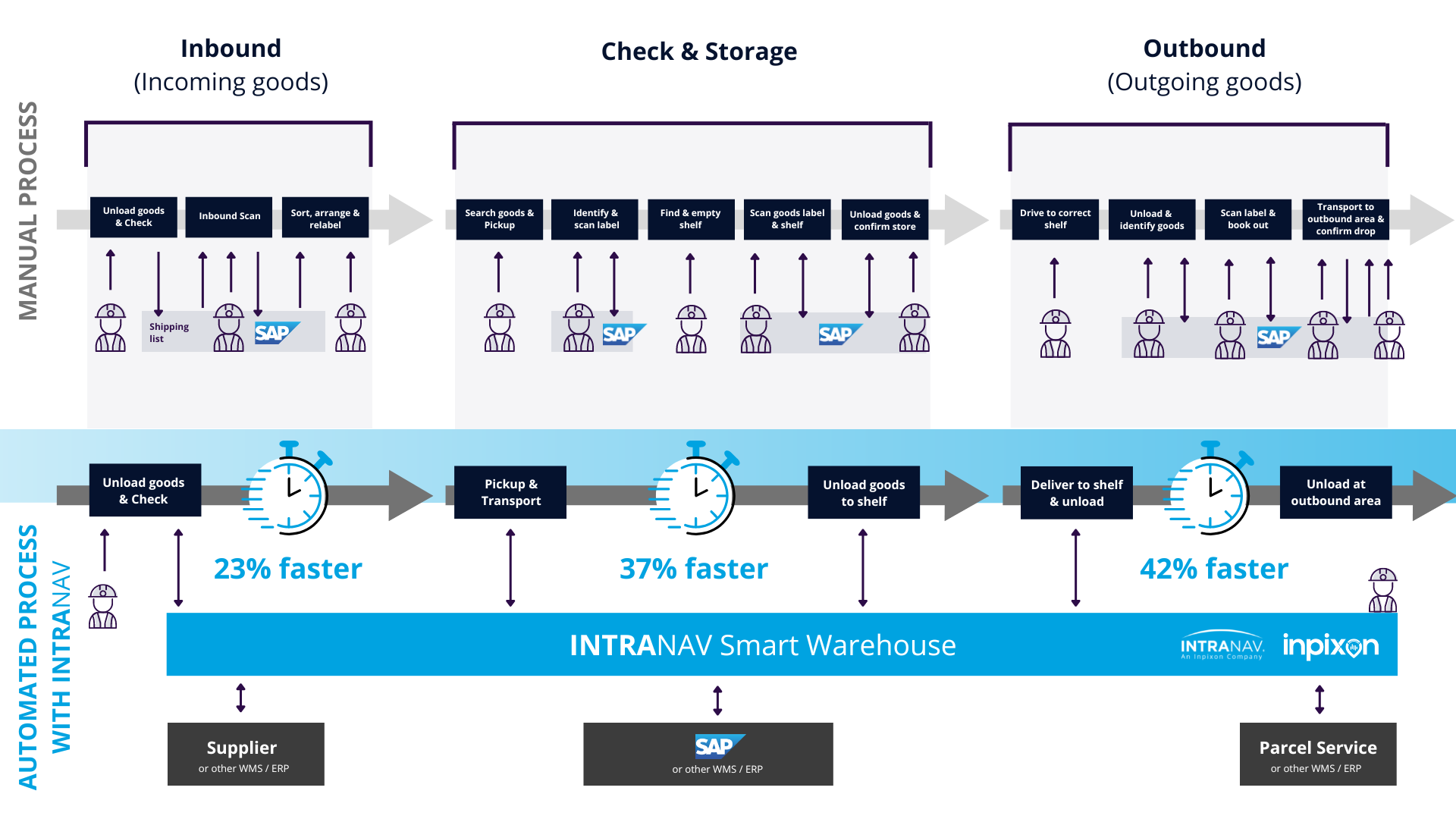
TBInt. monitors and controls its entire intralogistics process, from receipt of goods to shipping, through multi-RTLS layers with UWB and RFID technology. They have eliminated many manual processes and implemented an automatic transport order processing system controlled by INTRANAV Smart Warehouse software, to ensure superior reliability and efficiency.
- Elimination of scanning processes
- Real-time optimization of transport orders
- Reduction of empty runs
- Optimization of routes and capacity utilization
The RFID implementation of whole-carton handling increased efficiency by nearly 40% and increased productivity while reducing processing time. The Smart Warehouse solution will also enable TBInt. to sustainably increase efficiency at its other logistics locations – an important milestone for the company and its digital supply chain strategy.
TBInt. über INTRANAV Smart Warehouse Solution
Benefits for eCommerce Logistics
Intelligent Forklift
- Real-time tracking of forklifts
- Application for processing transport orders for drivers
- Route-optimized destination indication to the shelf
- Automatic assignment of transport orders to the fleet
Automatic identification and confirmation
- Automatic (scannerless) goods receipt and goods issue recording and posting in SAP
- Automatic and reliable sorting processes
Transparent warehouse
- Digital twin of the physical warehouse stock
- Transparency about occupied and free warehouse space