31.03.2022
How Software-Driven Factories, Warehouses and
Supply Chains are the Future
The future of manufacturing, warehousing and distribution facilities are changing as we know them thanks to industry 4.0. With the rising digitization of these facilities and their processes, factories are becoming more efficient, flexible and agile than ever before. This digitization also means we’re getting more data and insight into operations, improving the decision-making process and fueling competition. In this blog, we’ll go over what software-driven factories, warehouses and supply chains are, and how they’re impacting the future.
What is a Software Driven Factory, Warehouse or Supply Chain?
Software-driven facilities (also known as smart or digital facilities) refer to different combinations of modern technologies and IT systems connected to each other, to create self-adapting and automated processes. These facilities are entirely interconnected by sensors and IT systems, collecting data and outputting it in software. Every asset, vehicle, industrial equipment and more will be tagged, and their location and performance data is connected and sent to IT systems where warehouse or manufacturing managers can see a high-level overview of how the facility is operating. The visibility and real-time information of workflows and process chains gained from software-driven factories and warehouses allow plant and lean managers verify if the material and transport flow requires to be designed more efficiently, if equipment needs to be replaced, where costs can be cut, where manual work steps can be replaced by for example Auto-ID or location-based automation, where costs can be cut, and more.
One of the most important aspects of software-driven facilities is being able to master the use of the data being gathered, which results in higher productivity, optimized costs, faster time-to-market, and can also be your biggest competitive advantage.
Example of warehouse automation control through a software-driven warehouse
by INTRANAV, an Inpixon company
How Can You Build a Software Driven Facility?
Throughout the entire process of setting up a digital factory, it’s crucial to have a team solely in charge of the transformation of the facility to take care of change management. Before you get to the point where you’re gathering data that helps you make better business decisions, there are a few steps to get through first. The first step requires introducing interfaces to the IT systems, so that the information being gathered is accessible. With that, introduce an IIoT strategy that connects to your ERP and logistics systems, and ensure you have IT systems that match your operations. This step may require you to change or extend current IT systems to properly connect the entire facility.
With the right IT systems in place, production information can then be put on dashboards and process engines can be introduced to test how processes can be changed. The next level is AI and machine learning, so that the data being collected can be used to predict and prevent errors.
To summarize, here are the different layers of technology you would need:
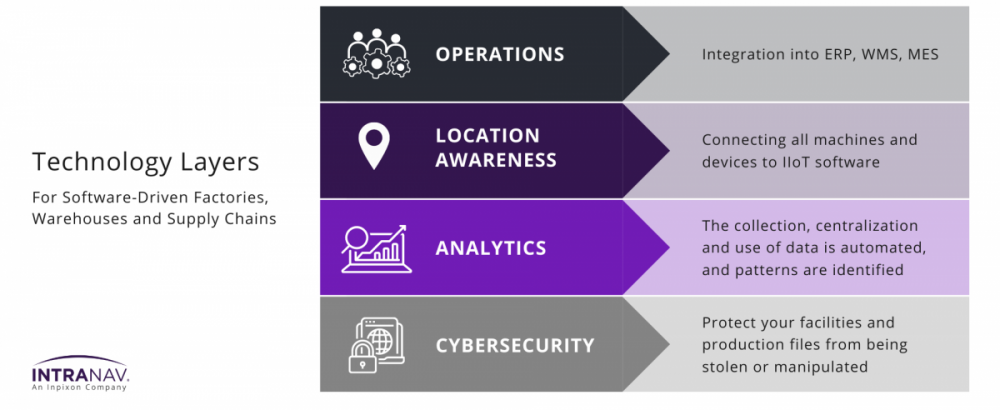
Operations: At the base, connected facilities need to be integrated by IT systems depending on the type of operation, such as the Enterprise Resource Planning (ERP) system and Warehouse Management System (WMS) or Manufacturing Executive System (MES).
Location Awareness: The next level is connecting all machines and devices to IIoT software, providing location awareness within the entire plant. With location-based networking, facilities can, for example, interact with each other automatically through geofencing and predetermined rules and initiate processes (e.g., initiate transport orders, posting and unposting goods into WMS/MES, trigger invoice printouts, start process chains, inform customers about shipments etc.), issue warning notifications, or block processes in critical situations or for quality assurance reasons. Here is an example for virtual manufacturing.
Analytics: Using artificial intelligence and machine learning, the processes to gather, centralize and make use of data is automated, and patterns are identified.
Cybersecurity: With the amount of data being collected, it’s crucial to have an added layer of security to protect your facilities and production files from being stolen or manipulated.
Key Differences Between Non-Software Driven Facilities and Soften-Driven Facilities
There are many differences between facilities that are driven by software and those that are not. Below, we’ve summarized the core differences into four aspects – how they store information, their reaction time to incidents, how they perform resource planning, and the insights each of them have on their equipment.
4 Key Differentiators Between Software and Non-Software Driven Facilities
Aspect | Non-Software Driven Facilities | Software Driven Facilities |
---|---|---|
Storing Information | All information was on paperwork such as printed excel sheets. There’s no cloud so if there’s a point of error, the entire system stops working. | Everything is digital and stored on cloud, so information is accessible to key employees. With cloud it’s easy to maintain software paths and information flows in case of error. |
Reaction Time | Reactive: When errors happen or machines shut down, you can only fix the problem after it happens. | Proactive: The facility runs on a model so you can simulate and modify how a factory operates, as well as predict errors and downtime. The digital twin enables also real-time reactiveness, detection of error sources and process blocks in real-time, and productivity monitoring of material handling figures ensures fast response to material supply fluctuations. |
Resource Planning | To make changes to the facility, personnel have to go onsite, locate the machine, measure the space, see how the machines are connected and how it gets its power supply completely manually. | With the digital twin, you can see a map view of your factory, warehouse and yard, simulate how new machines would work with others, and determine the right fit for your space. With AR or VR, remote experts can also see the facility digitally and make real-time decisions. |
Insights into Equipment | With the black-box model, you know what equipment and machines you have and what they do, but detailed information on their processes and how they’re being utilized is not accessible and would require inquiries with various stakeholders. | With IIoT, all equipment is connected by sensors that track their performance, temperature, process |
How are Software Driven Facilities Impacting the Future?
As more facilities adopt the software-driven model to make their operations as efficient as possible, the possibilities are endless. Here are some key themes in the industry for what’s to come.
Importance of Cybersecurity
The more data is being collected and stored in IT systems, the more vulnerable organizations become to ransomware, phishing, malware, DDOS attacks and more. With this, companies with software-driven facilities are expected to invest more in cybersecurity to protect their organization.
Changing Workforce
With the increase in manufacturing productivity, less workers are needed to achieve the same results. As automation becomes more popular, less personnel will be needed on site and jobs will be created around data science. There will be more job opportunities in IT, around agile technology, cyber-security practices, predictive analytics, coding and more. Remote workers will also be able to get real-time insights on operations using AR/VR, seeing the facility in the industrial metaverse.
Globalization
With the large-scale digitization being seen in factories, warehousing and manufacturing facilities, there is increasing demand for R&D and personalization. Consumer insights influencers can directly affect the way products are being produced (such as trending colors) and thanks to automation it’s easier than ever to customize products. Automation also gives smaller manufacturers the opportunity to compete with larger companies through customization. There also could be an increase of reshoring and a return to domestic manufacturing, reducing the reliance of foreign nations in the supply chain process.
Sustainability
Heightened consumer awareness is making sustainability an important factor in operations. Because of the next level of visibility gained in software-driven factories, it’s possible to be aware of your environmental impact, such as how much energy is being used, track water usage and ensure that your facility isn’t a major pollution source.
Factory & Warehouse Digitization
The increasing digitization of facilities will continue to see new technologies, from advanced robotics and additive manufacturing to 3D printing and self-driving vehicles. The use of IIoT sensors, predictive analytics, augmented and virtual reality, edge computing and more will be seen in more facilities as organizations become aware of the changing competitive landscape.
The Future is Digital and Connected
As digitization becomes an industry standard, software-driven factories will increase efficiency, customization, accuracy and reliability in operations. A boost in ROI in your organization will come from embracing the technology of the future, and taking the steps towards digital transformation. If you’re interested in starting your journey towards becoming a smart facility, contact us today!
Author
Ersan Guenes, SVP Product IIoT
Ersan Guenes is the Senior Vice President (SVP) of Product for IIOT (Industrial Internet of Things) at INTRANAV, an Inpixon company.
Learn more about Inpixon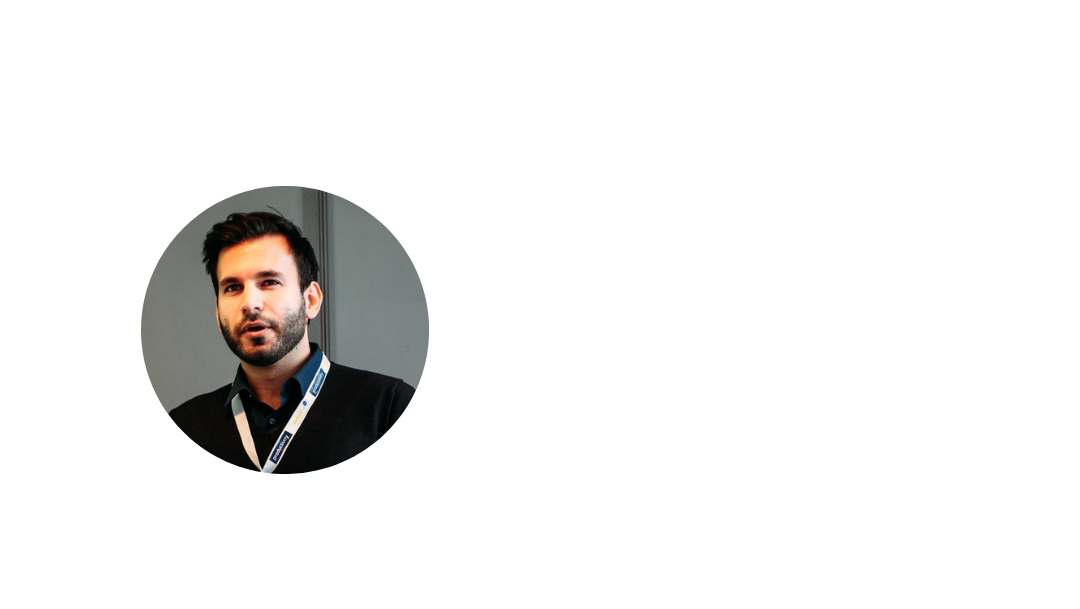