04.03.2022
The Digital Twin –
What it Is and Why It’s Important for Your IIoT Strategy
The digital twin is an important component of various IIoT projects, providing value that helps reach numerous business goals. A digital twin is the virtual representation of an object like a machine, or a process, like transportation; continuously updated with data to increase visibility in business operations. For example, in an industrial setting a piece of machinery, or equipment could be cloned and visualized as an icon on a digitized map. This icon, the digital twin, can be clicked and interacted with, enabling you to inspect and interpret the data associated with it that is collected by attached sensors.
The digital twin can represent a large variety of objects in a manufacturing facility, such as forklifts, boxes, pallets and more. It’s enriched with information on the object, such as its location, order ID, serial number and product manual; and sensor information such as temperature, humidity, acceleration, and more. In addition, it can represent a service (such as the movement of a truck dropping off merchandise) and provide information such as the date of the service, duration, quality of transport, etc. The contextual data provided by the digital twin creates enhanced visibility and is therefore incredibly useful in decision making.
How Does the Digital Twin Work?
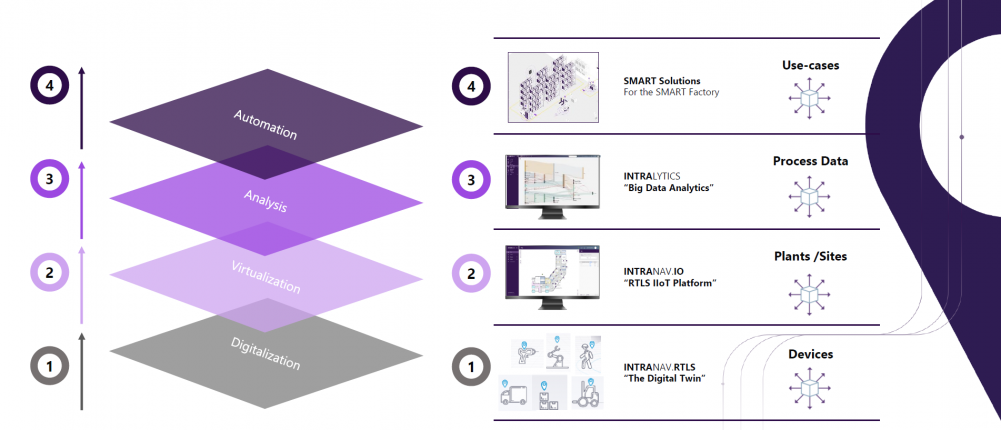
There are a couple components needed to get a physical object its own digital twin. The main components needed are different types of cyber-physical systems (CPS) such as sensors and IT systems that can transform information from an object to the virtual world. For example, to create the digital twin of a pallet to track it, you would attach a location sensor to the pallet, and connect it to software such as a Real-Time Location System (RTLS) or Indoor Positioning System (IPS), where the data gathered can be put in the right context.
With a digital twin, you can collect not only historical but current and near real-time data, depending on which IT system you choose to invest in. With an RTLS, it’s possible to get the near real-time location information needed to visualize data in the context of your facility.
What Makes Data Lakes Relevant to Digital Twins
With digital twins in your facility, a lot of data will be collected – and in order for it to be useful, it needs to be well structured. A data lake is where you can store all your data as is (in its raw format), before structuring it and running it through analytics. From that point you can choose to create dashboards or use machine learning to make the most out of your data in the way that makes the most sense for your organization. Being able to create value from the data collected creates a competitive advantage, by acting on business opportunities and cutting costs to outperform competitors.
Types of Digital Twins
There are diverse types of digital twins, so it’s important to learn which is the best match for your organization. While they all represent an object or process virtually, they vary by application.
● Component or Parts Twins: The twin of a single component or part in the whole system. For example, evaluating the durability of one machine.
● Asset Twins: The twin of two or more components (forming an asset) and tracking how they function together. For example, testing how the various components of an assembly line work to achieve better performance.
● System or Unit Twins: A combination of asset twins to see how the entire system works on a higher level. For example, evaluating how every part of the system is working to create a finished product, such as a laptop, to maximize performance.
● Process Twins: Twins that represent the entire facility, seeing how all systems work together. For example, determining the efficiency of a facility that manufactures cars, and seeing if there’s extra inventory that’s costing money.
Use Cases for the Digital Twin
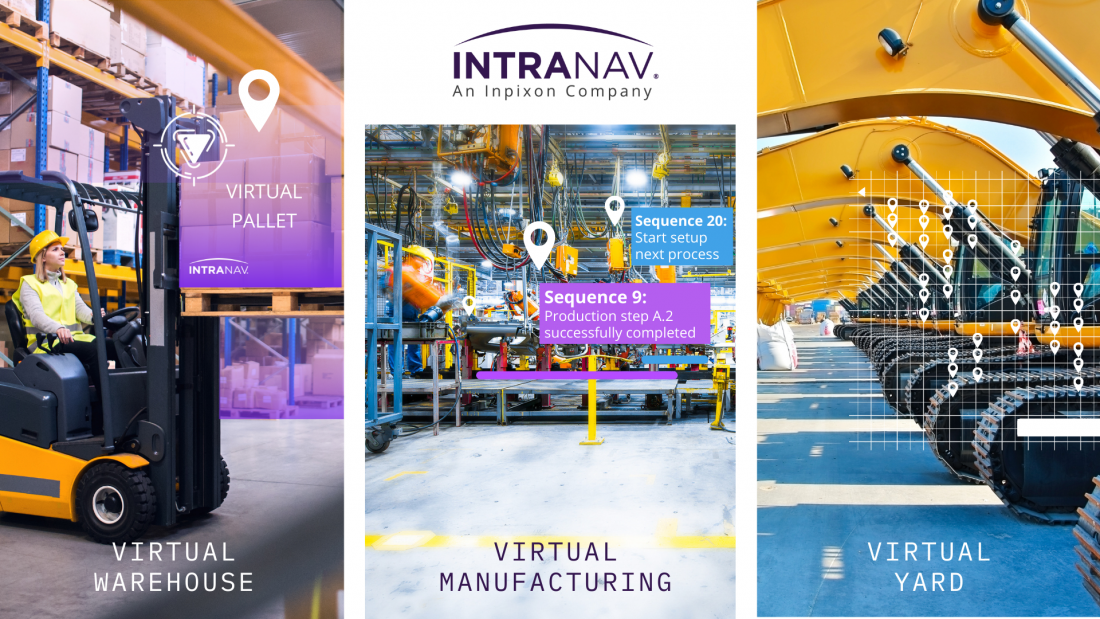
Boost Efficiency and Processes
Since the digital twin can mirror what is happening in the physical world, one of the most used applications is boosting efficiency in various facilities. The more data is collected from the digital twin, over time you can simulate processes virtually and test different conditions to create an optimized production methodology. That way you can test the best assembly line schedule or forklift route before it all goes out to production.
The consistent stream of accurate and near real-time information creates more efficient manufacturing operations. It also improves predictive analytics capabilities, as it standardizes data for those working on data analytics and dashboards. The more these processes are automated, the more time is saved and the less room there is for human error. Overall, the digital twin provides more visibility and faster, more reliable information.
Improve R&D and Product Creation
The use of digital twins allows for better design of products as well. Since you can simulate how different parts of a product work together, you can test numerous performance outcomes. It’s especially useful in mechanically complex projects, such as building large structures or power equipment. For example, with the digital twin of an airplane turbine, thanks to sensors you can track energy consumption, pressure, power and more. With a digital twin, manufacturers can develop a simulation to see the behavior of the turbine if they make certain changes, and that mimics the performance of the turbine in real life without making permanent decisions.
This refinement improves the quality of existing products, is useful for the creation of new products or helps decide what to do at the product end-of-life. By knowing that the ink for a printer lasts 6 months, companies provide subscription services so consumers get their ink before they run out. Or if the printers are prone to increased paper jams after 18 months, they can improve the printers in the next product generation. Because the digital twin also helps determine what product materials can be recycled, the same printer company gets extra support during the final processing.
Reduce Unnecessary Costs
By having more visibility over your operations, a digital twin can help reduce costs. With a process twin, seeing how the entire facility works together helps determine bottlenecks and spot inefficiencies that are costing the company. A simulation can be created of a facility to see what actions have an impact on energy consumption, maintenance costs, equipment capital investment and more. This can be compared to other facilities of the same company, or other competitors to gain a competitive edge.
The more data is collected, the more the digital twin helps predict what problems a machine may have and when, to prevent downtime that results in unnecessary losses. Predictive maintenance also comes into play, by determining the root cause and fixing small technical issues before they cause costly breakdowns. This helps in scheduling timeframes for regular maintenance, whether it’s power generation equipment or jet engines.
Interested in how you can benefit from digital twins in your facilities? Start by watching our webinar on the top 5 challenges of implementing an RTLS and how to overcome them, or contact us today.
Author
Ersan Guenes, SVP Product IIoT
Ersan Guenes is the Senior Vice President (SVP) of Product for IIOT (Industrial Internet of Things) at INTRANAV, an Inpixon company.
Learn more about Inpixon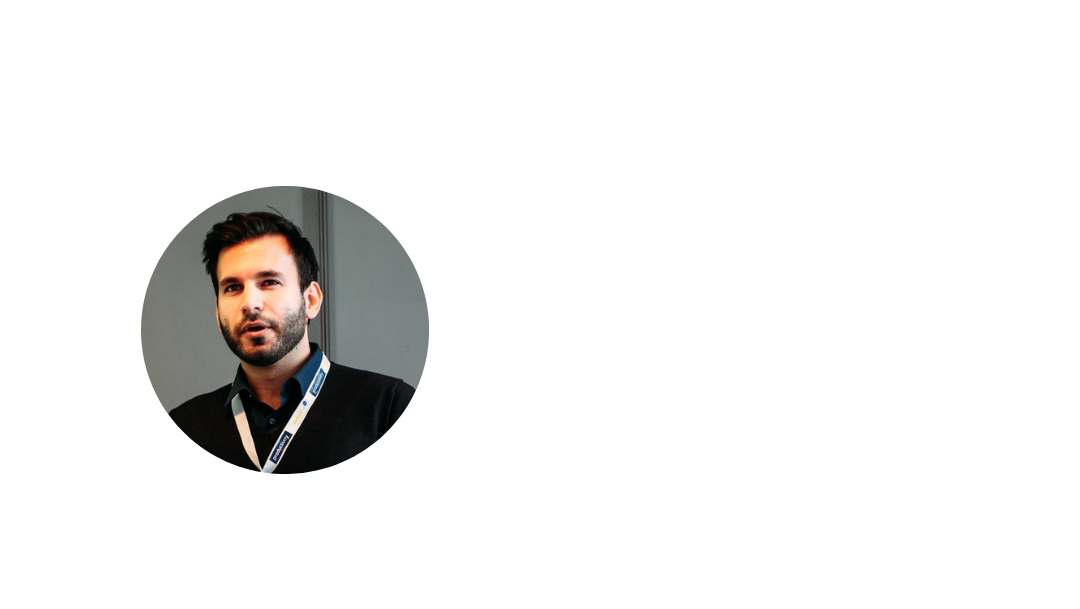