10.02.2022
How does IIoT work and what are the benefits for Industry 4.0?
The introduction of the Industrial Internet of Things (IIoT) as part of Industry 4.0 has revolutionized the way organizations use and analyze data. Throughout history, manufacturing has evolved from the creation of machines to boost production, to the use of computers to store information. Now in the 4th industrial revolution, we are in the era of smart machines, interconnectivity and near autonomy.
The Internet of Things (IoT) is a network of physical objects connected by the internet through sensors and software – this can be as simple as controlling a thermostat on your mobile device. Any object can become an IoT device as long as it is capable of connecting to the internet and communicating information.
IIoT follows the same principles as IoT but in industrial settings, where systems, people, and devices communicate with each other in a connected network. One such example are IoT sensors equipped to forklifts in a manufacturing facility, that communicate location information and detect nearby obstacles. The most significant benefit IIoT has had on the industrial revolution is its ability to provide data that we’ve never had before, allowing companies to make more informed decisions. Here are five specific ways that IIoT is changing the industry.
1) Increased Visibility
In factories of the past, visibility was often limited due to old processes and data. Organizations would know what they had in their factories, but not where their assets were and when they were moving. One of IIoT’s top benefits is its ability to give you unprecedented visibility over your operations. Through real-time information, organizations are gaining data that provides a 360 degree view of their organization.
Entire facilities can be connected, from vehicles and assets to personnel, just by wearing tags with sensors attached. The location and time stamped information can then be integrated with systems like Enterprise Resource Planning (ERP), allowing for greater connectivity. This information is also available on a consolidated user interface and on a variety of devices, taking operational awareness to new levels.
More specifically, IIoT can show an operations manager how production is running in real-time, with a great amount of detail. Through monthly or weekly reports, data can pinpoint if there are manufacturing errors or certain machines that are performing poorly. It allows operations managers to see what’s causing delays in production and to be able to make informed decisions to resolve those issues. In a growing competitive landscape, being able to quickly resolve any delays can help organizations stay ahead of the competition.
2) Higher Efficiency due to Automated Workflows
Workflow automation is key to boosting productivity and ROI, which is what IIoT provides. By automating mundane and simple tasks, work efficiency is improved, and your employees can focus on using their skills on more nuanced tasks that benefit your organization. Through IoT, automation also helps keep a wide range of devices connected, making processes more efficient.
In manufacturing or intralogistics settings, workflows include identifying materials with barcodes. In cases where people are manually scanning barcodes, it takes longer, and human error must be accounted for. With the use of smart machines, these processes can be done exactly how the organization wants. Additionally, since the machines are always connected, you’ll be able to identify if there is a malfunction happening before it’s too late. The ability to automate these manual tasks to streamline processes and get desired results is what drives IIoT projects.
3) Accurate Forecasting and Planning with Location Data
Location data helps organizations plan better than they ever have. Teams used to rely on historical data for forecasting, but another benefit of the IIoT is the ability to generate near real-time reporting. Location data is collected in a Real-Time Location System (RTLS) by attaching tracking tags with sensors to personnel, assets, and vehicles across your facilities. They then transmit their location data to fixed readers (RTLS anchors), which integrate the information into software and can be seen on various devices.
This data is also visualized on a digitized facility map, providing facility managers maximum control. A company struggling with supply chain issues, could use location information to pinpoint exactly where the delays are happening and make the decisions needed to fix errors and optimize processes. In addition, this data can help create faster routes for vehicles, efficient schedules for employees and machines, and as a result, make your processes more competitive.
4) Optimization of Operations and Processes
Manufacturers can take advantage of near real-time data for constant improvement in their operational efficiency. It all starts with IIoT being an ecosystem of connected devices, from forklifts to production equipment. Being able to see the entire facility holistically allows for better decision making and being able to set improved goals. It also increases transparency and accountability, with information easily accessible throughout multiple production stages.
Being able to see what machines are working on allows organizations to run as efficiently as possible, by maximizing equipment output. For example, a facility manager would be able to see which machines aren’t busy and assign additional production jobs to them, so time isn’t lost. Being able to see how your entire facility works allows you to make better decisions that create optimal routes and reduce traffic jams.
5) Avoid Process Errors
One of the biggest things holding organizations back is machine downtime, costing billions every year. Through older processes, equipment malfunction would result in defective products, costing time and resources. IIOT makes rapid detection possible and allows organizations to optimize production quality and get ahead of equipment failure.
It also minimizes human error, which accounts for a significant percentage of mistakes in manufacturing and industrial settings. These errors can happen due to exhaustion, which results in employees inputting data incorrectly or scanning the wrong barcode. With IIoT, if an employee is attempting to package a shipment and puts the wrong item, they can get a warning in real-time that they’re making an error. These alerts can be found by notification on a tablet, mobile phone or smart watch, and prevents customer complaints and the loss of resources. Data from IIOT allows for consistency and reliability in business processes, which is why this is an exceedingly popular use case.
Thinking of implementing a RTLS to bring greater connectivity into your industrial facilities? Watch our webinar on the top 5 challenges of implementing a RTLS and how to overcome them.
Author
Ersan Guenes, SVP Product IIoT
Ersan Guenes is the Senior Vice President (SVP) of Product for IIOT (Industrial Internet of Things) at INTRANAV, an Inpixon company.
Learn more about Inpixon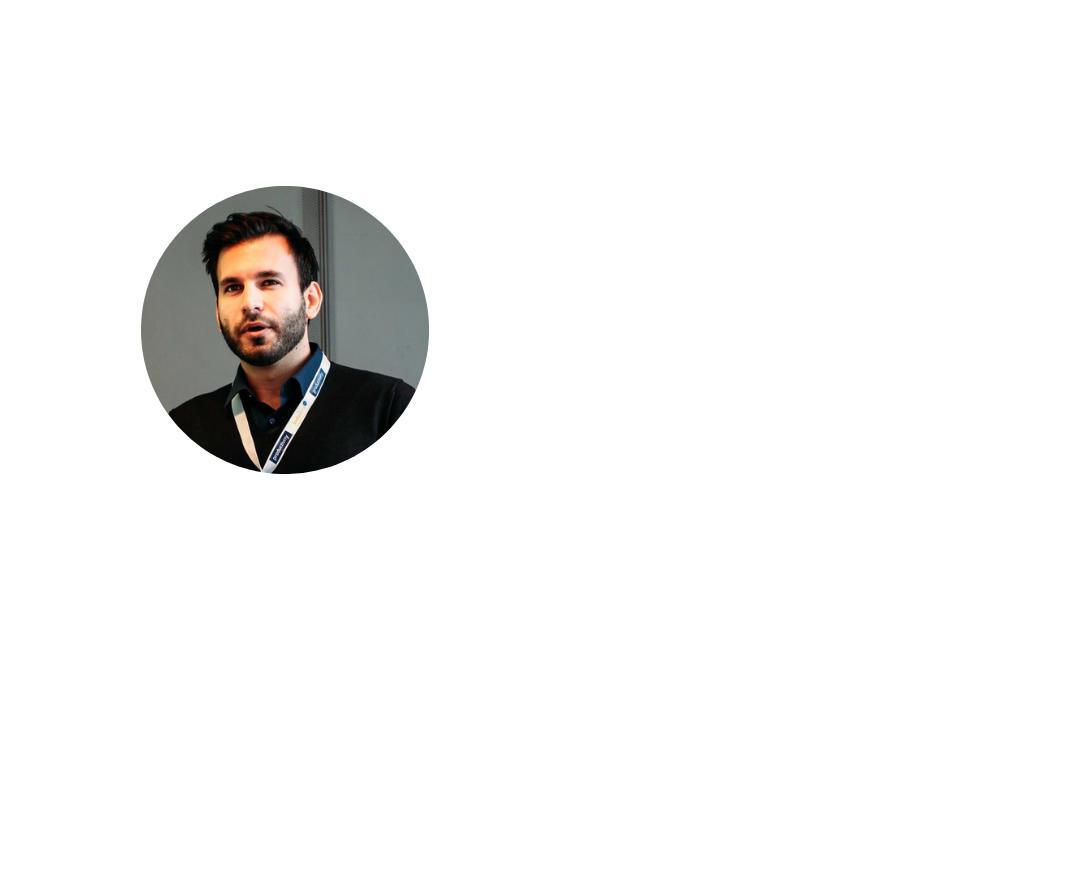